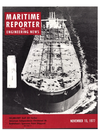
Page 15: of Maritime Reporter Magazine (November 15, 1977)
Read this page in Pdf, Flash or Html5 edition of November 15, 1977 Maritime Reporter Magazine
Ongoing R&D Effort Will Improve
Marine Boiler Reliability
John R. Brinser and Carl F. Horlitz Jr.*
During the past 15 to 20 years, the shipbuilding industry has placed increasing demands upon the manufacturers of main steam propulsion machinery to produce equipment of increasing reliabil- ity and efficiency. During this time period, the plant power re- quirements have steadily in- creased, machinery space avail- able has steadily decreased, cycle conditions have become more ex- treme, bunkering fuels have been gradually deteriorating in quality and, with the emergency of the energy crunch a few years ago, a renewed emphasis has been placed upon high efficiencies.
These requirements have placed an increasing burden on the al- ready harsh environment typical of the firesides and watersides of marine steam propulsion boilers.
To investigate the phenomena which affect boiler reliability, the
Maritime Administration in early 1975 funded the first phase of a program entitled "Improved Ma- rine Boiler Reliability." The ob- jective of this initial effort was to investigate the main problem areas encountered in the design and operation of a marine boiler and, through an investigation of recent technical papers, ships' op- erating records, boiler design pa- rameters, and fuel-oil analyses, to identify and research certain ba- sic concepts and parameters and to explore their effect upon boiler reliability. This phase was com- pleted in April 1976.
As a result of the investiga- tions carried out in the initial phase, several items relating to specific areas of marine boiler re- liability were chosen for labora- tory-type testing both on board ship and in land-based facilities.
This second phase also was funded by the Maritime Administration and began in July 1976 and will continue until early 1978. Items under investigation in this second phase include high- and low-tem- perature corrosion rates of vari- ous superheater and economizer heat-transfer surfaces, investiga- tion of superheater steam flow patterns, and analysis of marine boiler stack gas. *Mr. Brinser, project engineer, and
Mr. Horlitz, assistant manager, Com- bustion Engineering, Inc., C-E Marine
Power Systems, Windsor, Conn., pre- sented the paper abstracted here be- fore the recent Annual Meeting of
The Society of Naval Architects and
Marine Engineers. A complete copy of the paper may be obtained from the Society, One World Trade Center,
Suite 1369, New York, N.Y. 10048.
Superheater
The primary cause of super- heater tubing failure is high- temperature corrosion which is preceded by the formation of complex vanadium-based slags on tubing surfaces.
Consideration of the factors contributing to high-temperature slag corrosion of superheaters al- lows several recommendations to increase marine boiler superheat- er reliability. The objective for ships presently in service is to minimize the problems within the boiler operating and design con- straints, whereas the objective for future installations could include design features, material selec- tions and component configura- tions which may minimize the causes of the problem. There is no single optimum solution to the high-temperature slag corrosion problem; however, the first steps must include the specification of the superheater tubing environ- ment and reliability requirements by the boiler purchaser. The en- vironment is specified by the qual- ity of fuel available in the ship's operating area and the excess air level, both of which are ship- owner inputs and superheater con- figuration and material selections by the boiler manufacturer to suit reliability requirements.
Particular attention should be given to the maintenance of ex- cess air level in accordance with the operation and design require- ments of marine boilers presently in service. Design and testing programs in the area of low ex- cess air combustion equipment should continue and boiler de- signs should incorporate this equipment.
Superheater tubing material se- lection should be determined by the environment and reliability requirements of the purchaser.
Although the use of more exotic materials enhances superheater reliability, their use may not be cost effective due to significant higher initial costs and generally longer material and fabrication lead times.
Superheater reliability also can be improved through configuration modifications or "over design."
Configuration modifications in- clude the installation of additional screen rows and the selection of multistage superheaters. The first alternative reduces the radiant heat input to the superheater and results in minor reductions of maximum tube metal tempera- tures ; selection of this alternative might be warranted if the use of very poor quality fuels is antici- pated and if the boiler envelope will tolerate the coincident in- crease in superheater size. The orientation of the superheater elements themselves has a sig- nificant effect on superheater re- liability. Vertically oriented su- perheaters have been proven to be less susceptible to slagging and therefore are affected to a lesser degree by high-temperature corrosion than a horizontally con- figured arrangement. Superheater slagging also is directly affected by soot blower orientation, and in this regard it is important to have soot blower lance configured in a perpendicular fashion to the axis of the superheater elements.
The utilization of fuel-oil addi- tives is the one remaining choice to be considered for superheater reliability improvement. Although the use of fuel-oil additives has been shown to be effective in re- ducing the formation of highly corrosive slags and, hence, in re- ducing high-temperature corro- sion, an important consideration prior to their widespread accept- ance and application is that of fireside cleanliness. Experience has shown that the use of fuel- oil additives greatly increases the solids burden of the flue gases.
It is recommended that sufficient sootblowing capacity be proved through testing prior to the en- dorsement of the fuel-oil additive technique to reduce high-temper- ature corrosion. Additionally, it is recommended that chemical additives be tested to determine which ones of those presently available and advertised commer- cially are the most beneficial.
Superheater material corrosion rates are presently being deter- mined through the exposure of two multimaterial controlled-tem- perature corrosion probes located in the port boiler of the Stonewall
Jackson, a Waterman Steamship
Company LASH vessel. The high- temperature corrosion probes will be removed for analysis at six- month intervals.
At the present time, the au- thors' company is designing and constructing a superheater air- flow model. The model will be tested to provide quantitative data on superheater steam-side flow distribution for various modeled steaming loads and superheater configurations. The major vari- ables include location of the sat- urated-steam inlet, superheater pass size, desuperheater location and model flow rates.
During model flow tests, super- heater element flow distribution will be monitored by pressure transducers and continuously re- corded. Results of the testing program will be used to formu- late a computer-based mathemat- ical flow model whose validity will be checked by flow model testing.
After the satisfactory mathemat- ical flow model has been devel- oped, existing heat-transfer and tube-material temperature calcu- lation programs will be used to establish correlations among tube metal temperatures, superheater flow distribution and boiler load- ings for allowable superheater tubing materials.
Stack Gas Testing
In order to define more clearly a typical corrosion environment for cold-end heat exchangers, a program of stack-gas analysis was undertaken on an operating
LASH vessel. The major thrust of this investigation was to ob- tain sufficient information to per- mit the calculation of sulfuric- acid dewpoints at various boiler loadings and excess-air levels. In order to accomplish this, tests for sulfur dioxide, sulfur trioxide, oxygen, and water-vapor concen- tration in the stack gas were con- ducted over a wide range of boiler loadings and excess-air levels. The boiler used for the test was a
Combustion Engineering V2M8 welded-wall boiler equipped with two downward-firing steam-atom- izing marine oil burners, a steam air heater, and an economizer.
Over the course of five days, extensive testing and shipboard analyses were conducted at a va- riety of boiler loads and excess air levels, including a series of tests during minimum load conditions in port. Two representatives from
Combustion Engineering's Field
Testing and Performance Results
Group performed the highly spe- cialized gas analysis tests. A third technical representative coordi- nated the test program with the ship's engineering staff and main- tained boiler performance records.
While the dewpoint tempera- ture of sulfuric acid vapor may be an important parameter in de- termining the temperature below which condensation of acid is ex- pected to occur, the most signifi- cant factor determining the serv- ice life of heat-recovery equip- ment is the rate of corrosion of the heat-exchanger surface.
There are, however, no accepted methods for predicting by calcu- (continued on page 18)
November 15, 1977 17