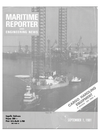
Page 29: of Maritime Reporter Magazine (September 1981)
Read this page in Pdf, Flash or Html5 edition of September 1981 Maritime Reporter Magazine
representing storage of about 80,000 tons.
This is one of two unloading systems serving a highly com- plex coal-handling facility. FMC of Canada's Material Handling
Systems Division in Scarboro,
Ontario, designed and built the new coal-handling and stockpil- ing system, which includes a dock hopper with dust hood, two 84- inch-wide belt conveyors totaling 1,750 feet, and FMC's massive luffing and slewing coal stacker.
The stacker is unique in many respects. It is impressive for its dimensions as well as the 7,000- tph capacity. It stands 92 feet high, and the base covers an area of 2,403 square feet. The boom is 173 feet overall, and the 84- inch-wide boom belt can be luffed from a ^/o-degree declined po- sition to an 11-degree incline. The belt travels at a speed of 750 feet per minute.
With the exception of the con- veyor drive, the stacker is en- tirely hydraulically driven. Luf- fing action is by hydraulic cyl- inder, and slew action by vari- able-speed drives transmitting torque to a rotating mast struc- ture.
The operator's cabin is located on the rotating mast structure, well above the luff axis, provid- ing a wide field of view. Cabin controls provide for either man- ual or automatic operation. Con- trol also can be transferred to the central control room, but manda- tory manual control is established during critical phases of the stock- ing-out operation — for example, where the pile is reaching maxi- mum height.
Automatic control is achieved by a programmable controller that is linked to all safety de- vices and monitoring systems. It is capable of initiating sequential startup or shutdown of the en- tire system or portions of it. Tel- ephone communication is avail- able from all main points to the self-unloading vessel.
Safety devices and detectors include plugged chute detectors, motion sensors to insure correct sequencing, belt side-travel switches, and belt penetration devices to detect possible belt damage. The integrity of the hy- draulic systems is monitored by a series of temperature and pres- sure detectors.
For additional information,
Write 31 on Reader Service Card
HAGGLUNDS
AB Hagglund and Soner, Swe- dish manufacturer of hydraulic motors and deck machinery, is one of the world's leading sup- pliers of marine cargo deck cranes. Represented in the United
States by Stal-Laval, Inc., Elms- ford, N.Y., the Hagglund crane has become known as the U.S. crane—all Hagglund marine car- go cranes installed on ships built in the United States in the last 10 years have been contracted,
September 1, 1981 installed, and serviced by Stal-
Laval. A variety of crane types, including single, twin, team, and grab, as well as ice class, are now operational on American-built ships. More than 1,200 ships worldwide have been equipped with deck cranes by Hagglunds.
The company has a continuing de- velopment program resulting in new designs and practical solu- tions to unique cargo problems.
The weakest link in the Arctic cargo handling chain is the ste- vedore. Human beings experience serious trouble when tempera- tures fall much below —25° C, or sooner if it is windy as well as cold. Some type of unit load han- dled by automatic cargo handling equipment is therefore a prereq- uisite for efficient cargo handling in the Arctic. Hagglunds manu- facturing methods, quality con- trol, materials, etc., make it pos- sible to use standard deck cranes at temperatures down to —25 C, or down to —30° C with extra heating and different hydraulic oil. Hagglunds experts have the know-how and the experience of cargo handling in Arctic climate, enabling them to offer cranes and cargo handling equipment suited to operation at temperatures of — 40° C or even lower. Hagglunds tests all new hydraulic crane com- ponents under winter conditions to determine reliability at low temperatures.
It may seem that a special (continued on page 32)
Challenging projects are routine with us.
Every day, architects, general contractors and building customers just like you turn to Mitchell building systems with their construction problems.
And we've built a reputation for solving even the toughest ones....quickly, efficiently and economically.
With a Mitchell building you'll choose from a wide range of structural systems, all designed to meet your specific needs. Wide clear-span buildings give you large, unobstructed floor areas. Overhead material handling equipment can be easily installed.
Best of all, your Mitchell builder will have your building up and ready for production in weeks, not months.
If you've got a challenging project....look to your local Mitchell builder, he's listed in the Yellow
Pages under Buildings - Metal. Or call (601) 328-6722 for immediate action.
Mitchell Engineering Company
Division of The Ceco Corporation, Chicago
P.O. Box 72
Mount Pleasant,
Iowa 52641 (319) 385-8001
P.O. Drawer 2387
Rocky Mount,
North Carolina 27801 (919) 977-2131
P.O. Drawer 911
Columbus,
Mississippi 39701 (601) 328-6722
Write 138 on Reader Service Card 31