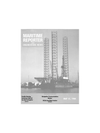
Page 27: of Maritime Reporter Magazine (May 1984)
Read this page in Pdf, Flash or Html5 edition of May 1984 Maritime Reporter Magazine
In independent field tests,
Coastal Science Associates com- pared the Butterworth 20,000-psi
Liqua-Blaster with abrasive-blasted surfaces. They reported, "At 20,000 psi, we got to white metal . . . clean of hidder corrosion cells."
Butterworth Inc. has been a leader in high-pressure water jet- ting technology for more than 20 years. With equipment offering pressures from 3,000 to 20,000 psi and a variety of flow rates, the ap- plications are unlimited.
BYWATER COATINGS
Circle 26 on Reader Service Card
Bywater Coatings Company of
Belle Chasse, La., is now a mem- ber of the Brink/Molyn Group of the Netherlands and its subsidi- ary, MCS Marine Coatings and
Services. This came about through the recent acquisition of Bywater by Brink/Molyn Beheer N.V.
The Byco-MCS marine line will continue as before with the addi- tion of MCS products, along with the availability of the combination on a worldwide basis.
Two new products of interest to
High maintenance costs due to corrosion
Intershield abrasion resistant coatings proof...
The problem:
The 'Corner Brook' a 7,722 dwt Ro-Ro, owned by Sig
Bergesen d.y. and Co of
Norway suffers severe corrosion from ice abrasion for approximately 5 months of the year.
The solution:
Intershield
The proof:
At drydocking in September 1983, after 25 months trading with Intershield on the bow area, the coating was 99% intact (fig 2).
Areas coated with traditional anticorrosive were 75% corroded (fig 1). The rest of the underwater hull has now been blasted and coated with Intershield. This is the second vessel for Sig Bergesen d.y. and
Co., to be coated with Intershield on the entire underwater hull. ft: -Sfpl
The problem:
Decks, particularly in work areas, suffer from corrosion caused by mechanical damage (fig 1).
This requires frequent maintenance, may be hazardous and is unsightly.
The solution:
Intershield
The proof:
Intershield was applied to selected deck areas, including around the manifold area, of a 20,000 dwt coastal tanker in April 1982.
After 9 months the vessel was inspected and the Intershield coated areas were reported to be 100% intact (fig 2) in spite of numerous loadings and unloadings of cargo.
The problem:
Corrosion in holds caused by cargo damage necessitates frequent and costly maintenance and can lead to cargo contamination.
The solution:
Intershield
The proof:
In May 1982, half No 5 hold in 'Star World', managed by World-Wide (Shipping)
Hong Kong was coated with Intershield, the remainder with a standard epoxy coating.
Within 3 months these latter areas were showing corrosion (fig 1), while the
Intershield areas were 100% intact. In June 1983, the superior and near perfect condition of Intershield is clearly evident as seen below (fig 2). As a result holds in both 'Star Hong Kong' and 'Star Magnate' are now coated with Intershield.
Inter
Eiiiiili
Abrasion resistant coatings
Already proven on more than 6 million dwt of world shipping
K
International
Paint
Circle 135 on Reader Service Card the marine user are 316 epoxy mastic and 950 urethane/alumi- num primer. Both products exhib- ited excellent adhesion to margin- ally cleaned steel surfaces (ST-3) along with a low moisture vapor transmission rate.
Byco-MCS 316 epoxy mastic is manufactured in two colors, red oxide and aluminum. It can be ap- plied in a single coat to 16 mils dry, and does not need a primer.
Its high solids (84 percent) make it economical to apply. The 316 can be used in both ballast and cargo tanks.
Byco-MCS 950 is a single-pack- age urethane/aluminum primer.
Topcoats of epoxies and urethanes make it a superior barrier coat system.
Byco-MCS Moluspeed 593 is the latest addition to the company's antifouling line. It was developed with the latest technology in co- polymers and toxicants. The 950 is based upon the combination of slight paint-film solubility and leaching.
CHESTERTON
Circle 27 on Reader Service Card
The Industrial & Marine Prod- ucts Division of A.W. Chesterton
Company of Stoneham, Mass., has developed, over a seven-year pe- riod, the antifouling coating OMP, which effectively retards growth of marine organisms and algae on ship hulls.
Three different coatings have been formulated: #210 OMP, which has the slowest extraction rate. It is designed for strong currents and/or when a vessel is in contin- uous service. A thickness of 150 microns should be applied. #220 OMP is designed for use in moderate currents and for vessels at sea half the time. A thickness of 245 microns is recommended. #230
OMP has the fastest extraction rate, and should be used where there is little or no current, and on vessels that are anchored most of the time. A thickness of 295 mi- crons should be applied.
OMP coatings can be applied by brush, roller, or spray. Its effec- tiveness is traced to a controlled release of an organometallic anti- foulant that is part of the prod- uct's binder system, and, unlike conventional coatings, is not mixed into the product.
CHUGOKU MARINE
Circle 28 on Reader Service Card
Chugoku Marine Paints, Ltd. of
Japan recently introduced a new family of self-polishing, antifoul- ing hull coatings. These new prod- ucts are based on the formulation technology of the company's AF-
SEAFLO Z-100 paint that was de- veloped five years ago and is now (continued on page 30) 29