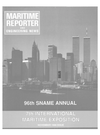
Page 78: of Maritime Reporter Magazine (November 1988)
Read this page in Pdf, Flash or Html5 edition of November 1988 Maritime Reporter Magazine
Modern Cargo Pumps
For Tankers And Barges by
Dipl. Ing. Heinrich Moller and Asmus W. Feck, P.E.* $12.3-Million Hyundai
Import Facility To Be
Built In Portland, Ore.
Hyundai Motor America and the
Port of Portland recently an- nounced that a $12.3-million facility dedicated to the importation of
Hyundai automobiles will be built in Portland, Ore. Construction of the facility is scheduled to begin early next year, with completion set for February 1990.
A minimum of 100,000 cars a year are expected to be moved through the port each year by Hyundai, which imported some 65,000 cars through Portland last year.
The facility, which will be leased by Hyundai for 15 years with an option for two additional five-year leases, will include a dock, a 60,000- square-foot processing building and holding lot for incoming cars. *Editor's Note: Dipl. Ing. Heinrich
Moller is general manager and technical director of Bornemann
Pumps, Obernkirchen, West Ger- many. Asmus W. Feck, P.E., based in Pawleys Island, S.C., is an international marine engineering consultant. This article has been excerpted from a technical paper written by Mr. Moller and Mr.
Feck.
Accurate cost estimating is a fun- damental part of operating a profit- able vessel. Nowadays, sea voyage time can be estimated fairly accu- rately. However, one area that con- tinues to defy accurate cost esti- mates is the time spent after the ship docks at a tanker terminal.
Generally speaking, the docking time of a tanker or barge is inher- ently dictated by the shore facilities and the design of the cargo pumping and loading systems, as well as the type and size of the main cargo pumps and drivers installed on board. Naturally, shipowners want to keep docking times as short as possible.
For this reason, every shipowner should guide the shipbuilder in se- lecting the best main cargo pumps for his needs. Ideally, they should be from a well-established, experi- enced manufacturer with an iden- tifiable presence in the marine in- dustry and a worldwide after-sale/ service network. And, as we believe, the external gear two-screw pump is the pump all modern tankers and barges should be using for their main cargo loading/unloading and stripping services.
In practice, it is difficult to esti- mate the discharge time of a tanker or barge equipped with reciprocat- ing duplex piston cargo pumps. One problem is the inherent cargo prod- uct vaporization of highly volatile solvents as benzene, benzol and sim- ilar fluids. This characteristic tends to vapor lock cargo pumps suctions, and when it does, it automatically voids all unloading time estimates.
It is common marine engineering knowledge that piston-type cargo pumps cannot cope with high-vol- ume percentages of vapors and air bubbles entrained in pump suction lines. From the very first moment of "lost suction" conditions, all recip- rocating piston cargo pumps are ex- posed to "dry running" conditions if not stopped immediately. Contin- uous dry running operation wears piston rings, cylinder liners and pump valve chest suction valve ser- vices. It can take more than 30 min- utes before a piston-type cargo pump is able to regain suction flow.
Under these dry running conditions, i.e., with little or no suction flow passing through the piston pump liquid cylinders, it will be impossi- ble to control or estimate the overall unloading time of the vessel.
Not all conventional centrifugal cargo pumps are self-priming. This means that if exposed even momen- tarily to lost suction conditions, they will not be able to pick up suc- tion quickly. Hence, continued car- go unloading is not possible. The end result in most of these lost suc- tion cases is that unacceptable de- lays in cargo unloading have to be accepted.
However, there are modern cargo pumps available that offer more ef- ficient, versatile and economical op- eration. Twin-screw main cargo pumps have been successfully used on board European motor tankers for many years.
The twin-screw cargo pump is a self-priming, positive displacement pump designed for cargo loading/ unloading and capable of tank strip- ping service. They combine the characteristics of a piston pump (positive displacement) with the characteristics of a centrifugal pump (rotating, pulse-free delivery) but without the inherent operating disadvantages of both.
Twin-screw pumps can be oper- ated at speeds of up to 2,000 rpm.
Space requirements for them are relatively small, requiring as little as 50 percent of the space required for otherwise equal capacity piston pumps. And, equally important, the twin-screw pump offers absolutely continuous performance with suc- tion line capability of up to 95 per- cent by volume of entrained air or gases. One of the biggest advantages a twin-screw cargo pump offers is the capability of extremely high suc- tion lifts.
In the case of light viscosity car- goes, such as solvents, benzene, ben- zol, or even seawater, the two-screw pump can lift a suction vacuum of 24 in. Hg (about 27.5 feet). Further- more, when pumping viscous car- goes, a viscous fluid film is formed around the pump screws. This film acts as a sealant and serves to increase the pump suction lift to 27.3 in. Hg (about 31 feet).
It is, of course, true that any amounts of entrained air or gas will reduce the actual flow at the pump discharge. These actual losses in discharge flow rates cannot be elim- inated. However, even under these trying suction conditions, unloading with twin-screw cargo pumps will never be disrupted unless the vol- ume percentage of air or gases ex- ceeds 95 percent.
It is also important to note that with their inherently balanced de- sign, two-screw cargo pumps are far quieter running than equivalently sized piston or centrifugal pumps operating under the same condi- tions. The observed noise level will be about the same as a well-bal- anced electric motor sized to drive the pump. And while it is possible to observe higher noise levels when pumping through too small suction
Unless, that is, you're a WATERCOM" subscriber. With WATERCOM, you're always in touch with your tows. You can speak immediately with your captains. You can find out where they are and what's happening to them.
And you can make informed judgments about pickups and deliveries.
But there's more. You not only get communications - you get the inland marine industry's only direct dial telephone system. For confidential communications, free of the problems of party lines. Consistent communications, without the dead spots of other systems. And FAX capabilities, for almost instant transmission of printed information
Maybe Gerry Brown said it best: "WATERCOM is good in the good times.
And they're great in the bad times. That's why it's on all our boats:'
WATERCOM. It's quick. It's clear. And whether the current's swift or the dredges are digging, your communications will always flow smoothly.
TELECOMMUNICATIONS FOR VESSELS AND SHORE. "During the drought of '88, about all that flowed was comm unica tions!'
Gerry Brown
Cargo Carriers, Minneapolis, M!\
To Gerry Brown - to everyone who does business on the river, for that matter - "drought" is a dirty word. It means channels drained to the dregs. Tows stranded up and down the waterway.
Confusion.
WATERCOM' is a registered trademark of Waterway
Communications System, Inc.
Waterway Communications System, Inc. 453 East Park Place
Jeffersonville, IN 47130 812-288-0300 80
Circle 183 on Reader Service Card Maritime Reporter/Engineering News