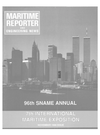
Page 79: of Maritime Reporter Magazine (November 1988)
Read this page in Pdf, Flash or Html5 edition of November 1988 Maritime Reporter Magazine
or discharge piping, or with high air or vapor bond fluids, the increase in noise levels from these conditions will be less for two-screw pumps than for the other types of cargo pumps mentioned.
At present, over 20,000 twin- screw pumps are in service on board modern European coastal tankers and barges.
What is generally not well known is that over 5,000 twin-screw cargo pumps are installed in Europe in land-based tanker off-loading ter- minals to serve river barges not equipped with their own cargo un- loading pumps. These pumps are often driven by reversible rotation drivers and fitted with special pip- ing so they can be used for both loading and unloading.
Many tankers and barges are equipped with independent main suctions and separate cargo strip- ping lines of smaller nominal diame- ters. In those cases, it is possible to switch twin-screw cargo pumps from the main lines to the cargo stripping lines and continue strip- ping the cargo tanks with the main cargo pumps. In essence, the main cargo pumps can be used as high- capacity strippers.
In the case of moderate-size tank- ers (about 50,000 dwt), when fitted with twin-screw cargo pumps, only three or four twin-screw cargo pumps are recommended per ship set. This excludes independent car- go stripping pumps but retains in- dependent cargo stripping lines of smaller diameter, which are re- quired for future tank cleaning ser- vices by the main cargo pumps.
Twin-screw cargo pumps can be driven by electric motors, diesel en- gines, steam turbines, gas turbines, turbo generators, hydraulic motors,
PTOs from main engines or gear boxes.
They are preferably operated at speeds ranging from 1,000-2,000 rpm. Thus, shipboard 60 Hz AC power supply is suitable to operate electric motor-driven twin-screw pumps at 1,150- or 1,750-rpm speeds.In all cases, it is always rec- ommended to provide amble driver bhp so in the event of lost cargo heating, when liquid viscosity and absorbed pump bhp gradually in- crease, adequate horsepower is still available
In practice, cargo pump drivers are installed in the engine room or on the main deck in a deckhouse.
The pumps, either in a pump room or submerged in a cargo tank-well, are driven by jack shafts or cardan shafts via the bulkhead or engine room flats. The drive shafts are sealed by gas-tight, self-aligning bulkhead stuffing boxes. It is not essential to place twin-screw pump suctions close to the ship's bottom, i.e., inside a pump room. It is, how- ever, still good engineering practice to locate cargo pump suctions as low as possible in a pump room or cargo tank suction well so the main pumps can be used for tank cleaning and cargo stripping.
Twin-screw pumps can also be installed directly into a cargo tank.
There may also be a choice between single- or two-speed motors, if so desired. Deck space required for
November, 1988 these arrangements are minimal.
For the transportation of heavy viscous crudes, Exxon Corp. in- stalled aboard several existing 40- 51,000-dwt steam tankers three to four horizontal twin-screw cargo pumps per ship set to replace cen- trifugal cargo pumps. The new units have a cargo discharge capacity of 5,000 gpm each, at 1,200 rpm pump speed driven by 1,000-hp geared steam turbines capable of speeds from 250 to 1,200 rpm. All units were retrofitted by a major East
Coast shipyard in 1980/81. The large twin-screw pumps are also used to strip the cargo tanks dry at low pump speeds and eliminated the need for special self-priming air pumps. The cargo pumps were in- stalled at the lowest possible level in the main pump room aft. By request of the shipowner, the ships were refurbished with vertical positive displacement cargo stripping pumps. The independent cargo stripping pumps serve a separate cargo stripping piping system for cargo tank cleaning.
Some U.S.-flag shipowners have been looking for main cargo oil pumps suitable for handling an ever-increasing range of cargo prod- ucts—from the lightest to the heav- iest viscosities. Others are inter- (continued)
Twin-Screw SCHOTTEL-Tugs Improve Tugboat Operations
The service-proven SCHOTTEL-Rudderpro- peller facilitated the development of robust, reliable and very economical tugs with a high degree of safety and seaworthiness. In all ports of the world where SCHOTTEL-Tugs are used their excellent manoeuvrability and outstanding operational safety have brought decisive improvements in tugboat operation and assistance to sea-going vessels.
SCHOTTEL-Systems have proved them- selves for more than 35 years, and are avail- able in numerous propulsion and steering units and manoeuvring aids in the range 15 - 5,000 kW. To date over 19,000 SCHOTTEL units with more than 6 million hp propulsion capacity have been delivered all over the world. If you plan a newbuilding or conver- sion - get in touch with one of the world-wide
SCHOTTEL companies or representatives.
SCHOTTEL-WERFT, D-5401 Spay / West Germany, Tel.: (02628) 610, Teletex: (17) 262891 SW SPAY
SCHOTTEL OF AMERICA, INC., 8375 N.W. 56 Street, Miami/Florida 33166,Tel.(305) 592-7350
The SCHOTTEL-Group offers world-wide sales and service through SCHOTTEL companies located in Hamburg, The Hague, London, Paris, Genoa, Basle, Vienna, Miami, Buenos
Aires, Porto Alegre, Singapore, Sydney, and representatives throughout the world.
Circle 196 on Reader Service Card 81
SCHOTTEL for progressive propulsion