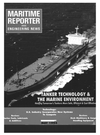
Page 21: of Maritime Reporter Magazine (May 1994)
Read this page in Pdf, Flash or Html5 edition of May 1994 Maritime Reporter Magazine
Buying Into The Future: U.S. Industry Changing To Compete
But the real benefit, he believes, is the program's focus on commer- cially viable products. "(With this project) we're not focused on build- ing a product for the government; we are building a product for the commercial market which also fits the government's needs."
WEMD Takes Two TRP
Awards
The Westinghouse Electro-Me- chanical Division (WEMD) was the first privately owned design and manufacturing facility devoted ex- clusively to the production of criti- cal components for nuclear reac- tors. Formed in 1952, the division is fully owned and operated by the
Westinghouse Electric Corporation, in Cheswick, Pa. The initial focus of the facility was to provide reactor main coolant pumps with integral motors for the U.S. Naval Nuclear
Propulsion Program. WEMD sup- plied the main coolant pumps for the world's first nuclear-powered submarine, the U.S.S. Nautilus.
ARPA received more than 80 pro- posals addressing shipbuilding and provided five awards. Of these five awards for the shipbuilding indus- trial infrastructure category,
WEMD received two: Development of the Submerged Electric Cargo
Pumping System, and Demonstra- tion of the Integral Motor/Propeller
Propulsion system for commercial ships. According to WEMD, a sub- merged electric drive pump would be a major step forward in liquid cargo handling technology for prod- uct tankers and liquid chemical car- riers. The critical issue of opera- tional safety has been thoroughly addressed in the design. The WEMD concept has received positive feed- back from shipyards, ship opera- tors, maritime architects and con- sultants.
The WEMD Submerged Electric
Drive cargo pump would be a direct substitute for either of the currently available technologies: submerged hydraulic pumps or deck-mounted electric deep well pumps. The de- sign was conceived to provide ad- vantages, including: eliminating the hydraulic power supply and high-pressure deck manifold of the submerged hydraulic system, and eliminating the long shaft and mul- tiple bearings of the deck-mounted electrical system.
Foreign Partnerships: importing Technology =
Exporting Ships
The Maritime Administration has entered into a cooperative agree- ment with Bath Iron Works (BIW) to develop the capability to construct competitive ships for export. The two-year, $13.9 million project is in essence designed to transfer man- agement and production process technologies to create a globally com- petitive shipyard. Specifically, tech- nologies to be transferred could in- clude computer-aided design and process simulation, advanced auto- mated fabrication processes, flex- ible automation/robotics, real time measurement systems for process control, production planning, mate- rial control and estimating, and pol- lution abatement. These process technologies, it is maintained, will help improve both production of com- mercial vessels and warships for the U.S. Navy.
Of the total $13.9 million cost, the government will provide up to $4.5 million, with Bath Iron Works and its partners contributing $5.7 mil- lion in cash and $3.7 million in in- kind services. Partners in the project include Great American Lines, Inc. and American Automar, Inc. Also participating are Kvaerner Masa-
Yards and Mitsui Engineering and
Shipbuilding.
The TRP award is just one piece of BIW's attempt to modify technol- ogy, modernize facilities and de- velop human resources to become a competitive commercial ship- builder, according to Joseph
Fortin, director of commercial ship- building. According to him, BIW had a five-year plan to commercial- ize before TRP. The primary goal of the program was, and is, to save jobs and retain a skilled workforce.
The end goal of the five-year plan is to build RoRo-type ships, said Mr.
Fortin, a vessel type chosen be- cause of the complexity factor. "BIW's strength is in our ability to outfit complex ships," he said. The goal at Bath is to be in a position by
Now there's a comprehensive way to assess a tanker's hull structural condition, along with its machinery and operating equipment.
It's our ABS SafeHulf Condition
Assessment Services.
Surveyors can cany out an on-board Condition Assessment
Survey and Verification of Gaugings to assess the tanker's physical condition. Then, using advanced design criteria and software, an ABS
SafeHull Structural Evaluation is performed. This is done to assess real-life dynamic loads.
Using the gaugings data and historical trading profile information, identification of critical areas and suggested enhancements are made.
AQQ MARINE
SERVICES, INC.
AN AFFILIATE OF THE AMERICAN BUREAU OF SHIPPING
Houston 713 873-2101
Piraeus 30 1 429-3804
London 44 71377-4422
Singapore 65 732-3230
ABS SafeHull Condition
Assessment Services help manage the risk of structural failure. They can help lower life cycle maintenance and repair costs. Technological evaluation helps inform underwriters and charterers and may boost resale value.
And only ABS SafeHull offers you a technical analysis that incorporates fatigue evaluation as part of a condition assessment service. You can ask for the Condition Assessment
Survey, Verification of Gaugings and the ABS SafeHull Structural Evaluation, or just the structural evaluation alone.
For more information about ABS
SafeHull Condition Assessment
Services, contact your nearest ABS
Marine Services office.
Circle 203 on Reader Service Card
May, 1994 23