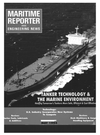
Page 22: of Maritime Reporter Magazine (May 1994)
Read this page in Pdf, Flash or Html5 edition of May 1994 Maritime Reporter Magazine
Buying Into The Future: U.S. Industry Changing To Compete late 1995 to attract a multi-ship deal. While the final goal is to build commercial vessels, Mr. Fortin claims the yard will maintain ties to the Navy. "Commercial work at
Bath Iron Works will not replace
Navy work, it will supplement our core business, which is and prob- ably always will be, Navy shipbuild- ing." Yet he maintains a direct benefit will be the capability to build
Navy ships even more efficiently.
It also means that BIW must inte- grate processes and systems which work best in a dual use—commer- cial and military—facility.
Phase one of the technology trans- fer, already completed, involved sending small, cross-functional groups from BIW to the two partici- pating yards to observe. Phase two will entail taking the acquired knowl- edge from phase one, and sending back specific people to witness spe- cific process technologies.
In BIW's case, the term "technol- ogy transfer" does not specifically equate to the purchasing of a piece of equipment, but rather to the trans- fer of process improvement tech- niques, leading to executable ship- building plans, from market analy- sis, to design, to a design and con- struction plan, to facilities modern- ization.
NASSCO is another shipyard looking overseas, while making fa- cility enhancements, in an attempt to win commercial business. Ac- cording to Fred Hallett, senior vice president and chief financial officer, the shipyard signed a technology transfer agreement with Kawasaki
Heavy Industries Shipbuilding Div. (KHI). The agreement provides for employees from both yards to make visits, in particular looking at lay- out, accuracy control, equipment and the general processes incorpo- rated to put an orderbook through the facility. He noted that the yards are very similar in many ways, and have been working together infor- mally for the past 10 years, just recently formalizing the relation- ship with the technology transfer agreement. In essence, NASSCO wants to build "relatively simple, large, ocean-going ships," according to Mr. Hallett—such as tankers, container ships and car carriers.
However, Mr. Hallett maintains that "defense conversion" is in fact a misnomer for NASSCO, because of the yard's history of involvement in the commercial market. He refers to it more as a return to a strong commercial base, and maintains that the following areas must be ad- dressed to do so: • Yard Modernization: Must meet the standards to compete on an in- ternational level. Ongoing projects include the Ways 2 project, a $5 million project which is the yard's biggest facility upgrade, intended to help perfect its on-block outfit- ting techniques. The company hopes to use MarAd Title XI funds here. • Technology Update: NASSCO believes its relationship with KHI can help it "leap frog" up to the technology level it desires. • Market Access: Simply put, the creation of a level playing field (i.e. subsidy elimination), and in the event that never comes to fruition, teaming with foreign competitors.
On the subject of subsidies, Mr.
Hallett is doubtful that they will ever be eliminated: "If I was a foreign government and you were asking me to give up jobs, why would
I do it?"
For skeptics who doubt the abil- ity of U.S. shipbuilders to become competitive on the international level, Mr. Hallett suggests that the state of the U.S. steel industry years ago serves as a strong example to the contrary. "Ten to 15 years ago the U.S. steel industry was written off as old and non-competitive. There was a structure put in place to allow them to compete, and today's cost- per-ton is competitive worldwide."
For additional information from any of the companies mentioned in this story, circle the appropri- ate number on the Reader Service
Card.
Bath Iron Works 59
CYBO Robots 60
NASSCO 1
Newport News Shipbuilding 62
U.S. Shipbuilding Corporation 3
Westinghouse Electro-Mechanical Division.... 118
Ashland Chemical
Drew Ameroid Marine Division Ashland Chemical Company
Division of
Ashland Oil, Inc.
Address Reply:
One Drew Plaza
Boonton, NJ 07005
Phone:(201)263-7600
Fax: (201) 263-4491
RE: Corrosion Inhibitors and Soft Coatings — A Case of Mistaken Identity
Dear Customers and Marine Industry Associates:
Over the past twenty years, ballast tanks and void spaces on several thousand ships have been treated with our
MAGNAKOTE® or MAGNAKOTE PLUS rust preventatives. These extremely effective corrosion inhibitors offer unsurpassed long-term protection backed by our LIFE PRESERVERSM inspection program and warranties of up to five years. In fact, the top ratings earned by MAGNAKOTE PLUS in the recent Marintek study make it the premier corrosion inhibitor, outperforming all other non-hard coatings. For all of you who have chosen the
MAGNAKOTE solution, we want you to know, YOU HAVE MADE THE RIGHT CHOICE!
In a class all their own, corrosion inhibitors are sometimes mistaken for soft coatings and mislabeled as such.
There has been a movement recently to restrict the use of soft coatings by imposing additional inspection requirements and limiting their use to void spaces and permanent ballast tanks. The stated concerns are that these coatings: do not stop corrosion; are temporary; and are thick, slippery and usually opaque, creating hazards for inspectors and making inspection of existing conditions difficult. In most cases, these statements are true of barrier-type soft coatings. However, they are not true for corrosion inhibitors.
CORROSION PREVENTION
Coatings and corrosion inhibitors work in entirely different ways. Barrier-type soft coatings function by preventing oxygen from reaching the metal surface, with the disadvantage that any moisture present prior to application may supply oxygen or chlorides resulting in corrosion beneath the barrier. (The same problem can occur with inadequate surface preparation or improper application of hard coatings, such as two-part epoxies.)
Corrosion inhibitors such as MAGNAKOTE and MAGNAKOTE PLUS rust preventatives penetrate rusted surfaces to form an electrochemical bond to the steel. As they descale any existing rust, they also interact with any oxides present to prevent further corrosion.
DURABILITY
All corrosion protection products are temporary if applied with no follow-up; and reputable manufacturers should have programs in place for inspecting ballast tanks. With Drew's regular inspections of MAGNAKOTE and
MAGNAKOTE PLUS applications and touch-ups as needed, these corrosion inhibitors can protect a ballast tank indefinitely. (And, unlike epoxies, corrosion inhibitors are easily applied and repaired by the ship's crew, saving hundreds of thousands of dollars in preparation and application costs.)
SAFETY AND INSPECTION CONDITIONS
Although soft coatings are applied in opaque layers as thick as 1,600 microns, corrosion inhibitors are normally applied as thin film. The MAGNAKOTE rust preventatives are applied at a thickness of 75 microns (even thinner than a typical epoxy) in a transparent film that makes the steel underneath the treatment clearly visible.
Independent and class society surveyors as well as Drew's service engineers have conducted thousands of inspections of ships treated with our corrosion inhibitors. These inspections have been easy and accurate, with no reports of any difficulties.
Drew welcomes the debate about methods to protect ballast tanks. We believe all will benefit from a better understanding of the available technologies. While we encourage the classification societies in their quest to ensure the integrity of ships' ballast tanks, we ask that they also respect the technologies offered by corrosion inhibitors such as MAGNAKOTE and MAGNAKOTE PLUS. Corrosion inhibitors have earned a prominent place in effective corrosion protection programs, along with judicious use of hard coatings and cathodic methods.
The marine industry needs regulations that give ship owners/managers the flexibility to make choices that will ensure optimal performance at cost levels they can afford.
Very truly yours,
John R. Wolf
Vice President, Marketing
Circle 263 on Reader Service Card 24 Maritime Reporter/Engineering News