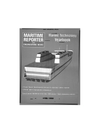
Page 56: of Maritime Reporter Magazine (April 1995)
Read this page in Pdf, Flash or Html5 edition of April 1995 Maritime Reporter Magazine
Rising Sun Engine Project
Engine to package 10 to 15% fuel savings with 40 to 50% specific weight reduction (Continued from page 64) been tested exhaustively, and does not at least match the competition in economy.
The long gestation of this engine can be explained by the aims of the project and the very high working parameters necessary to attain these aims — far above existing practice.
The prototype being test run is a six-cylinder
V-form, with a 300mm bore and a 480mm piston stroke, developing 4,340 kW (5,900 bhp) at 750 rpm. This performance corre- sponds to a bmep of 31.4 bar (495 lb./in.2) and a mean piston speed of 12 m/s (2,360 ft./m), both quite exceptional figures for an engine with these cylinder dimensions. Only the lightweight engines for fast naval craft and running at up to 1,300 rpm reach 12 m/s; and 10 m/s would be a very good figure for a contemporary 750-rpm engine.
This has been made possible by the exten- sive use of ceramic materials, not hitherto reported as being used in ic engines of more than chainsaw size. A ceramic material has been applied, by plasma-coating, to the cylinder liners and piston rings. This com- bination has a very low coefficient of friction and high anti-wear properties. The lubri- cant works under much less severe condi- tions in spite of the higher rating. Further, a porous form of ceramic, diffusion-bonded to the piston crown, acts as an insulating layer to reduce heat stress. The porosity affords a flexibility to prevent cracking and damage to the liner, while these layers, together, reduce heat dissipation to the cooling water and piston oil, retaining it in the combustion chamber for conversion to extra work and recovery in the high-effi- ciency compound turbochargers.
Side-mounted fuel injectors work at up to 2,000 bar and the single inlet and exhaust valves are hydraulically operated, with com- puter-controlled Mechatronics which in- tervene to alter the fuel injection and gas valve timing to suit altered loadings, nota- bly at lower power and starting; normally problems with very highly rated engines.
The results claimed include fuel consump- tion reduction by 10 to 15 percent, to- gether with a specific output (mean cylin- der pressure x mean piston speed) in- creased by 50 to 80 percent. The specific weight is reduced by 40 to 50 percent.
Reliability must be measured after some years in actual service, but measurements suggest long life of wearing components.
SAMPUNG MADE
SIMPLE!
Circle 332 on Reader Service Card 66
MMC International Corp. 60 Inip Drive
Inwood, NY 11096-0664 U.S.A.
Phone: 800-645-7339 1-718-327-3430 • 1-516-239-7339
Telex: 96-0140 MAMCAF INND
Fax: 516-371-3134
MMC (Europe) Ltd.
South Nelson Road
South Nelson Industrial Estate
Cramlington
Northumberland NE23 9HL UK
Phone:(01670) 738111
Telex: 537005 MARINE G
Fax: (01670) 738789
MMC (Asia) Ltd. 7-7, 2-Chome, Kotonoo-Cho
Chuo-ku, Kobe 651
Japan
Phone: (078) 251-1033
Telex: 5624163 OPECK J
Fax: (078) 252-0265
WITH
KA-SPEED PROF.
FROM 40" UP TO 140" DIAM.
TOTALLY HYDRODINAMIC SECTION * MAXIMUM FUEL SAVING * 6% MORE THRUST * 10% MORE FREE RUNNING
OVER KORT 19-A NOZZLE
RICE PROPELLERS
AV. RIOS ESPINOZA # 88
MAZATLAN, MEXICO 82180
TEL: 011(526)983-6552
FAX: 011(526)984-2533
MMC CL0SEP3AMPUNG
GET THE NOZZLE SYSTEM THAT
WON'T DRAG YOUR BOAT
RICE SPEED NOZZLE
Circle 326 on Reader Service Card
Maritime Reporter/Engineering News
Keeping You in Control
MMC's new
Closed Sampling Tape has its own built-in sampling port.
Take a look. The sampling port is located at the base of the barrel. Just put the tape in place on any one of a wide range of existing MMC deck valves, twist the collar and you're ready*to go. (There's even a handy adaptor to make it fit non-MMC valves.)
Its closed construction keeps emissions from escaping into the atmosphere so you're in compliance with all applicable vapor-control regulations. A return hose assembly even directs vapors displaced from the sample bottle back into the system.
The sample bottle is then quickly and neatly removed, and capped for testing and/or laboratory analysis.
One final point: It's all made in the USA by MMC, a name you've learned to trust for over 50 years.