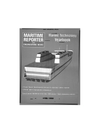
Page 58: of Maritime Reporter Magazine (April 1995)
Read this page in Pdf, Flash or Html5 edition of April 1995 Maritime Reporter Magazine
New Propellers Help Make M/V Dixie
Commander Quieter & Faster
Dixie Carriers Inc., Offshore Div. purchased the Dixie Commander/
DXE 1640 OS in late 1992 and started operating the tug/barge unit in mid-1993. During the first year and a half of operation, the vessel did not perform up to the company's expectations, as it vibrated severely when the main engines reached maximum rated rpm.
The boat entered Norshipco in
January for propeller replacement.
A pair of Bird Johnson New Genera- tion Workwheel propellers was in- stalled, and today the vessel can reach full rated rpm with no vibra- tion. It is currently under contract operating from Marcus Hook, Pa. up the eastern seaboard, the owner reports.
From Two To One
It seems the Dixie Commander has a unique history. It was built from two 1941 military single-screw tugboat hulls. The forward section and the superstructure were re- moved from both hulls, and the two after sections were fitted together.
A new forebody and superstructure were fitted, making a twin-screw boat.
Dixie Carriers reports there were two contributing factors in the vessel's poor performance: the unique hull design and the wide skags on the barge — both believed to cause cavitation in the propel- lers. As it was deemed expensive to rectify these problems, the vessel cavitational vibration.
New Propellers,
Less Vibration
Bird Johnson approached Dixie
Carriers with its new propeller de- sign, and claimed the props would eliminate 40 to 50 percent of the cavitational vibration on the vessel.
The five-bladed New Generation
Workwheel was designed using the latest technologies, and incorporates five blades to reduce unsteady blade forces. The propeller's pitch distri- bution was developed to minimize cavitation while maintaining opti- mal efficiency. The series also boasts modified VLR blade sections, of ad- vanced airfoil type for optimal cavi- tation performance. The combina- tion of advanced blade sections, vari- able pitch distribution, increased number of blades and blade skew allows the manufacturer to quote significant vibration reduction.
Following installation of the new propellers at Norshipco, the boat made its trial run from Norfolk to
Philadelphia via the Chesapeake
Bay. The crew was reportedly amazed at the vibration reduction, and the vessel steamed up the bay averaging 10.2 knots with a ballast barge.
For more information from Bird Johnson
Circle 105 on Reader Service Card
For more information on Norshipco
Circle 106 on Reader Service Card was instead relegated to operating below its full potential. At maxi- mum, the two diesel engines onboard were able to produce 800 to 810 rpm before the vibration became so strong that the crew feared mechanical fail- ure. The average speed of the boat was between 8.5 and 9 knots with a loaded barge or in a ballast condi- tion, and the operator was able to use only about 75 percent of the 7,200 hp available due to the
Environmental Hazards Kept In
Check With Ultrasonic Technology
As cargo ships grow larger and environmen-tal laws get tougher, the use of ultrasonic instruments to test for gas leaks and fugi- tive emissions is steadily growing in popularity.
The simplicity of these tools as well as their ability to adapt to many different types of situa- tions and inspection requirements have helped shipowners save time and money, maintain the quality of product, and ensure the safety of employees and the environment.
Ultrasound allows an operator to check the watertightness of hatchcovers and doors in place of using conventional hose testing.
Ultrasonic testing reduces the number of maintenance and repair hours logged in by a vessel because it allows operators to identify and arrest leaks rapidly and efficiently, eliminating the need for less efficient visual inspection meth- ods.
Other uses of ultrasound include testing the gas pressure or vacuum leakages of cargo tanks, as well as inspections of steam traps and valves, bearings, bulkheads, the engine room and the main deck.
Ultrasonic testing is extremely helpful in keep- ing vessels compliant with vapor recovery laws.
Ships carrying petroleum products are required to prevent fugitive emissions from entering the atmosphere, and vapor recovery zones are set up by locale to enforce these regulations.
If a vessel employs ultrasonic testing to check for unlawful atmospheric emissions, the safety of the vessel and the environment can be efficiently maintained, avoiding mandated, costly slow- downs by air quality control boards.
It has been reported that ultrasonic technol- ogy is spreading worldwide, used by companies such as U.S.-based Chevron Shipping, Stolt Par- cel Tankers, Inc., South African-based A.R. Brink & Associates, Antwerp-based Sparks & Co., and
London-based Aalmar Surveys.
Complying With Vapor Recovery Laws
San Francisco-based Chevron Shipping oper- ates a fleet of 40 company-owned vessels both internationally and nationally. The ships carry
Ultrasonic testing gun in action. petroleum products such as crude oils and gaso- line blends that are covered under vapor recov- ery regulations.
For the past three years, Chevron has been using ultrasonic testing as part of its preventive maintenance program to eliminate or minimize 60 Maritime Reporter/Engineering News