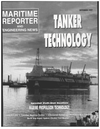
Page 84: of Maritime Reporter Magazine (September 1997)
Read this page in Pdf, Flash or Html5 edition of September 1997 Maritime Reporter Magazine
PROPULSION GUIDE (Continued from page 72) 4 (Bottom right, page 72) is the fuel oil system showing piping 50mm and larger. Machinery unitization and packaging was not heavily emphasized during this particular design, as vendor relationships were still being formed. The team felt, though, that this would be an eventual source for pushing advances in machinery packaging and unitization.
Process
At the beginning of the design process the team had already reached the "Norming" stage of the four stages of team development — "Forming, Storming, Norming and
Performing." As the team was still developing there were many occa- sions where the team would regress to the storming stage.
During this phase of the project the team was continuing to work as individuals with an increasing transfer of information between the individuals as the design pro- gressed. Although the team was working effectively, the high syner- gistic output levels that are charac- teristic of a true IPPD team did not occur during the SSD#1 design.
This level of teaming was to be expected, in that traditionally teams experience a six-month learning curve to reach the 'per- forming' stage. Near the end of this first design, the team had reached the performing stage although they had not yet matured to being a 'self-directed' team.
Many of the team processes that the team would embrace at the end of the project had their foundation laid during this period.
Tools by which team progress could be developed, referred to as "metrics," were developed during the SDM process. This area, more than any other, remained a bone of contention between the Steering
Committee and core team through- out the entire design effort.
The team decided to divide process metrics into two categories, the first being a set of team dynam- ics measures and the second relat- ed to the design process itself.
The team dynamic measures of equal team participation, clear understanding of the deliverables, basic team process development, rapid decision making, good listen- ing skills, mutual respect, commit- ment to making the team work, technical skills and open-minded spirit, were used in a team analysis format with decent results.
The actual design process metrics devised to assess how well the design process was performing became a nagging sore point with the team.
These metrics consisted of: value- addedability, repeatability, useabil- ity, definability, adaptability, vali- dateability, fundability and sanc- tionability. Primarily because these metrics were subjective in nature and that the team had no basis for comparison other than the design process through which they were constructing, these metrics were never used on SSD#1. The product metrics developed during the SDM process were: affordability, pro- ducibility, reliability, performabili- ty, maitainability, flexibility, avail- ability, and operability. Although these metrics appeared on the sur- face to be easily measured, the application to SSD#1 divided the team and was a significant prob- lem between the team and the
Steering Committee.
Design Process
During the design of SSD#1, the basic design processes for the pro- ject were developed. As a first step the team reviewed the processes used at each of the participating shipyards. The basic approaches were similar for the foreign and domestic yards. One significant difference was that the foreign shipyards all started from a base- line design with customer require- ments and operational and produc- tion improvements added to enhance the competitive nature of the design.
Throughout the project, chief engineers from Maersk Lines and
Crowley Marine were part of the team on a two-week rotating basis.
Their input throughout the design process was invaluable in introduc- ing characteristics that consider- ably improved the life cycle" cost as well as the operational and mainte- nance aspects of the SSD#1 design.
Early in the design, it was realized that the best product could only be created if it were an improvement over a truly operational world-class ship. Therefore, the team selected
MA/ Betelguese, a Brazilian designed RoRo/LoLo convertible ship, as the baseline because the design details were readily avail- able, the horsepower was similar to the COM 20 requirements and it was a state-of-the-art, competitive design. The team retained the use of the PD-337 hull envelope. The first phase of the process (a two- week period) was to select the main engine and develop the system con- cepts. The second phase of the pro- ject (a one-week period) was the development of multiple engine room arrangements. These arrangements were developed by hand sketching on 2D computer- generated plans and elevations.
The first step was locating the main engine and generators. The second step was the identification of the major volume drivers. This included the engine control room, workshop, purifier room, air com- ^—.1