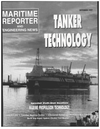
Page 85: of Maritime Reporter Magazine (September 1997)
Read this page in Pdf, Flash or Html5 edition of September 1997 Maritime Reporter Magazine
pressors, seawater pumps and heat exchangers, fresh water pumps, main engine lube oil pumps and coolers, fuel and lube oil transfer pumps, refrigeration system and fuel oil and lube oil tanks. The major volume drivers were located in relation to the major connections to the main engine and generators.
Eight arrangements were devel- oped, reviewed in a meeting setting to capitalize on the synergism of the multi-national composition of the team and revised according to recommendations. The modified arrangements were reviewed using a QFD analysis tool that rated the physical "locational" and the 'rela- tional' aspects of each of the arrangements against an ideal matrix for both of those aspects.
The selected arrangement was then modified to incorporate as many of the positive aspects of the other arrangements as possible.
The third phase (a 24-week peri- od) included trade-off studies to determine equipment vendors, detailed development of the sys- tems and the 3D product model development
Conclusions
The physical separation of ERAM core team members from their par- ent organizations was one of the elements of the project's success.
Overall, the sources of training for the team were excellent. However, the order in which the training was provided to the team could have been improved. The teambuilding training should have preceded the
IPPD, SDM and QFD training.
The team would have gotten much more out of its subsequent training if it had been educated on basic teaming skills at the beginning of the project.
Shipyard involvement and that of equipment suppliers from around the world proved invaluable.
Equipment suppliers were far more forthcoming about state-of-the-art equipment technology than first anticipated. Overall, additional involvement of commercial ship- builders would have been helpful.
The team realized that they had lacked adequate structural design support and cost engineering input throughout the course of this design. The request for a full-time structural design person was not fully responded to as only an increased presence of a part-time structural engineer was provided.
The team attempted to use a com- bination of IPPD and SDM as the basis for its unique design process.
Both methods have strengths and weaknesses. IPPD as presented relied heavily on the use of QFD techniques. QFD is extremely labor and time consuming and should be used sparingly. IPPD did bring a proven discipline to the team that was used throughout the project.
The SDM approach, which has been used successfully by the auto- motive industry, was also applied throughout the project. The major drawback of SDM was the formula- tion and application of in-process metrics of performance for the design team. The concept and use of in-process design reviews was realized as an important element of the IPPD process by the ERAM design team. The goal was to min- imize the design review prepara- tion time and present results taken from natural breakpoints in the chosen design process. The concept of using in-process data as a progress report to be reviewed for buy-in at an "In-Process Design
Review" carried very little favor with the Steering Committee dur- ing this period of the project.
Preparation for the management team had to remain open to the In-
Process Design Review process in order to fully realize the gains available from the IPPD process.
The IPPD User's Guide was to the ERAM process what the 3-D
CAD product model was to the
ERAM product. It represented the best identified approaches tried and used by the team and can act as a valuable reference in giving future teams a head start on what processes work and which should be avoided. Upon completion of this design, the team remained intact with the exception that the slow speed diesel engine represen- tative returned to his parent com- pany, MAN B&W. The team conse- quently needed to reorganize the workload, and also felt the need for additional teaming improvements, which was accomplished through a facilitated peer review process.
The team improved upon the baseline design of M/V Betelgeuse by: strategically routing distribu- tive systems; eliminating systems and components wherever possible; consolidating systems and compo- nents; carefully justifying the use of redundancy; and minimizing exotic material types. Most of these improvements can be traced to the upfront time spent by the team developing multiple engine room arrangements. The process developed by the team to eliminate, or amalgamate, these arrange- ments into the final design proved to be a distinct advantage over pre- vious practice and led to significant improvements over the baseline ship, in the areas identified above.
The importance of a good vendor library in developing equipment product models is essential to a successful product model develop- ment. The lack of vendor supplied 3D equipment models required an extensive expenditure of time to develop a suitable suite of 3D equipment models.
Computer software to support an
The ENERSYN range of lubricating oils marketed by BP Marine are high performance synthetic oils designed to provide optimum protection against wear for machinery operating under severe conditions.
All our synthetics have been specifically designed to meet the exact performance requirements of critical pieces of machinery operating at extreme temperatures and where low deposits are an essential operation requirement.
The use of synthetics can be cost effective in the following applications: Air Compressors, Refrigeration
Compressors, Turbochargers, Gas Compressors and
Centrifuge Gearboxes.
If you would like further information please contact us - or fill in the coupon.
To: BP Marine Ltd., Synthetics Brochure, Breakspear Park,
Breakspear Way, Hemel Hempstead, Herts HP2 4UL, UK.
Telephone: +44 (0) 1442 224474 Fax: +44 (0) 1442 225934
E-Mail: [email protected] Internet: www.bp.com/bpmarine
Name
Title
Company
Address
MR 9/97
BP Marine. Where the people make the difference.