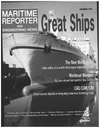
Page 33: of Maritime Reporter Magazine (December 1997)
Read this page in Pdf, Flash or Html5 edition of December 1997 Maritime Reporter Magazine
SHIP & BOATBUILDING TECHNOLOGY
CAD/CAM/CIM : Using Today's High-Tech Tools For State-Of-The-Art
Shipbuilding
World-class shipyards and design firms are focusing on how best to use computers in the ship design and production process. The key to their success in areas such as design, factory automation and systems integration is enhanced computer-aided design/computer- aided manufacturing/computer- integrated manufacturing (CAD/CAM/CIM).
CAD/CAM/CIM systems are found in all leading shipyards today. The systems may comprise commercial software such as
FORAN, TRIBON and CATIA, or software that was developed in house, such as HICADEC and
MATES. The application may be for quick-turnaround initial design, one-off production design or the production design of a series of ships. The following paragraphs address selected CAD/CAM/CIM systems in world-class shipyards.
DESIGN
In-House Development/
Series Production
The HICADEC CAD/CAM sys- tem is typically used to support the design and production of series
VLCC and containerships. While
HICADEC is important in the design phase, perhaps its greatest strengths are evident during pro- duction. HICADEC, initially developed by Hitachi Zosen, is used at the Ariake Works, one of the most modern shipyards in
Japan. The system is also in use at
Denmark's Odense Steel Shipyard.
Hitachi Zosen and Odense share ongoing development work and have tailored the system to the individual needs of each yard. At the Ariake Works, HICADEC cur- rently enables detail design and most of production design to be accomplished in seven to eight months between completion of the basic design and first cutting of steel. The production planning (block divisions and fabrication sequence planning) is done inde- pendently.
In-House Development/
One-Off Production
As with HICADEC, Mitsubishi
Heavy Industry (MHI) developed its MATES system in-house.
However, the system is tailored to
December, 1997 one-off designs in support of the yard's business strategy of build- ing one-off rather than series prod- ucts. MATES focuses on the design phase of shipbuilding. Key features of the MATES hull sys- tem, which permits rapid develop- ment of new ship product defini-
Oil Level
Vehicle
Fuel Tank tions, are the topological modeling capabilities and libraries of para- metric-defined regional structural (Continued on page 35)
NO DRAIN
NO PA IN . 4,000 hours between oil changes!
Now it's easy with the new CENTINEL™
Advanced Engine Oil Management System, an innovation that can save you a lot of time and money, hour after hour.
How CENTINEL Works:
CENTINEL is an onboard continuous replacement system that operates according to the engine's actual duty cycle. Using proprietary electronic controls, the CENTINEL system monitors fuel rate and replaces oil at rates engineered for continued reliability and durability of the engine.
CENTINEL's continuous oil replacement process stabilizes engine oil quality and allows oil and filter change intervals to be extended to unprecedented levels. With CENTINEL, you can: • Extend oil change intervals to 4,000 hours • Extend oil filter change intervals to 1,000 hours • Reduce oil and oil filter disposal costs • Reduce downtime • Increase productivity and profitability
Low
Sen
Oil Control
Valve
Fuel/Lube Oil
Blend to
Engine
CENTINEL is available exclusively through Cummins distributors and dealers. For details, contact your nearest Cummins location or phone 1 -800-DIESELS (1 -800-343-7357). ©1997 Cummins Engine Company, Inc., Box 3005, Columbus, IN 47202-3005, U.S.A.
Circle 226 on Reader Service Card 33