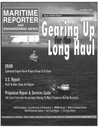
Page 41: of Maritime Reporter Magazine (October 1998)
Read this page in Pdf, Flash or Html5 edition of October 1998 Maritime Reporter Magazine
PROPULSION REPAIR & SERVICES GUIDE
MAN B&W—Hamburg service (enter
As a vibrant element of the city port's industrial infrastructure, the extremely versatile MAN B&W
Service Center in Hamburg plays a key role in supporting the huge population of own brand machin- ery while repairing and servicing a wide range of other marques and equipment.
The premises at the Rosshafen
Terminal in the inner dock estate provide alongside berthing for ships up to 90,000 dwt and embrace a large-scale manufactur- ing capability which extends beyond engine components, spares and crankshafts to a range of pre- cision and specialized engineering tasks.
The operating remit of Service
Center Werk Hamburg thereby includes repairs, overhaul and modernization of MAN B&W engines and other makes, spare parts production, supply and depot function, engine parts exchange and reconditioning, turbocharger service, and boiler and turbine plant repairs. Such is the remark- able diversity of the undertaking that it includes a materials testing and research laboratory, and around-the-clock troubleshooter service, while also acting as a gen- eral contractor for hull work and other shipboard jobs.
Equipped with a whole array of specialized machine tools and accredited facilities, the company propounds powerful arguments for having repairs to highly stressed engine components performed exclusively by the engine maker or licenser. For instance, its in-situ repairs of crankshafts, including shrink-fitting of new throws, repo- sitioning of webs and grinding of crankshafts, is based on the designer's quality criteria and decades of experience in crank- shaft manufacture.
The Service Center employs high-grade and component-com- patible materials as part of its welding technology in recondition- ing the exhaust valves of advanced two-stroke engines operating at high ignition pressures.
Dependable and safe engine opera- tion is allied to proper account being accorded to applicable load factors. It abhors the practice sometimes employed in the indus- try to use filler pieces in the repair of combustion system components, with the aim of saving costs or out of ignorance of the working loads imposed on such parts.
As part of the original design and licenser group, the Hamburg enterprise claims that it is far bet- ter placed to carry out extensive and intricate procedures such as heat treatment to cast steel or forged steel cylinder covers follow- ing major welding repairs.
Innovative reconditioning processes, including long-term component protection against both hot corrosion and dew point corro- sion, are offered by the Service
Center.
This is particularly salient to exhaust valve housing, wherein gas channel walls are susceptible to aggressive exhaust gases and temperatures below the dew point.
Indicative of the shipboard plant modernization scope of the
Hamburg works, worn piston rods of long-serving GF and GB-type engines can be hardened and ground to an undersize dimension and the stuffing boxes upgraded to the latest design status of the cur- rent generation of MAN B&W MC- series two-stroke diesels.
The in-house materials and test- ing laboratory not only supports the MAN B&W service operations, but also handles a great variety of orders placed by outside firms. It undertakes technological and met- allographic tests, chemical and non-destructive tests, damage analysis, general linear measuring technology, and balancing opera- tions and provides a material advi- sory service.
Ongoing research into repair procedures is reflected in the level of service it provides. For example, it advocates the repair of the seat- ings of the exhaust valve housings in four-stroke engine cylinder cov- ers by a special method.
This entails a defined and tem- perature-controlled, circular, semi- automatic welding procedure, using alloy-optimized weld metals.
It categorically dismisses local welding as a recipe for a recur- rence of damage. — DT
Port Weller Invests In Future by Alan Thorpe, international editor
Canadian Shipbuilding & Engineering Ltd. (CS&E) currently operates two yards on the
Great Lakes — Port Weller Dry Docks (PWDD), located at St. Catherines on Lake Ontario, and
Pascol Engineering at Thunder Bay on Lake
Superior. CS&E is owned by a consortium of shipowning companies including 50 percent by
CSL Equity Investments Ltd., which is a joint venture between CSL and Fednav, and 50 per- cent by Upper Lakes Group Inc. (ULGI).
Earlier this year, Canada Steamship Lines,
Inc. (CSL) awarded PWDD an approximately $92 million contract for three option two con- version projects involving the installation of new forebodies on exisiting sterns, all ships for the Great Lakes' trade. Each vessel will arrive in the yard during the same period each year, when the St. Lawrence Seaway closes due to ice coverage. The first vessel to undergo this con- version will be the 33,100-dwt J W McGiffin, which is due to arrive at the yard during
December this year and will be completed by
May 1999. For this contract, PWDD is current- ly upgrading its steel production plant at the yard utilizing a new TTS panel line and various new robotic welding systems. This investment, worth some $4 million, is part of a $13 million investment program over a 10 year period. It will result in a 25 percent increase in steel throughput at the yard. At the same time a new five year agreement with the workforce will also allow the yard to complete this contract to the given schedule of five years.
Apart from the CSL conversion project,
CS&E has recently completed two other conver- sion projects - the first involving the conversion to self-unloader of the 32,600-dwt Algowest, the fifth such conversion carried out by the yard in recent years. The yard has also recently com- pleted the 'cut and stick' conversion of the
Canadian Transfer. The vessel comprises the aft section of the 26,390-dwt Canadian
Explorer, the forward section of the Hamilton
Transfer and a new 23 ft. (7 m) mid-body sec- tion.
Meanwhile, the Thunder Bay facility (Pascol
Engineering) is currently busy with hull repairs to the 33,660-dwt Canadian Olympic, which is currently in the yard for rudder damage and some steel replacement work. Also currently at the yard is the 28,200-dwt Algonorth, which has been laid up since repairs were completed dur- ing last winter. The largest repair contract han- dled last winter season involved the 30,100-dwt
Halifax, which under-went $1.6 million of steel renewal. The new TTS panel line being installed at Port Weller. The Canadian Transfer after conversion.
October, 1998 41