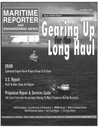
Page 48: of Maritime Reporter Magazine (October 1998)
Read this page in Pdf, Flash or Html5 edition of October 1998 Maritime Reporter Magazine
Software Solutions; CAD/CAM/CAE
ERAM Draws To Conclusion At DTMB
For more than a year, Maritime
Reporter & Engineering News has tracked the progress of a multi- national team working to develop an optimized engine room arrange- ment. This is the final article in a four-part series describing the pro- ject executed by the U.S. Navy in partnership with domestic and international shipyards, shipown- er/operators and marine equip- ment vendors.
As mentioned in the first article, the project was an Engine Room
Arrangement Model (ERAM) study, sponsored by the Mid-Term
Strategic Sealift Technology
Development Program (MTSST-
DP) and orchestrated by the
Shipbuilding Technology
Department of the David Taylor
Model Basin (DTMB).
The vision of the project was to initiate a customer-focused process that would enable the U.S. ship- building industry to design and build engine rooms that would pro- mote internationally competitive commercial ships. The objectives were: • To provide a forum for U.S. shipbuilders to present their views and needs for product and process design. • Within 12 months, develop a process using Integrated Process and Product Development (IPPD) for industry use, to design engine room arrangements that provides the basis for the design of interna- tionally competitive commercial
ERAM (core) team participants for the SSD#3 design were:
Country
U.S.
U.S.
U.S.
U.S.
Brazil
U.S.
U.S.
U.S.
U.S.
U.S.
Denmark
Company
D&P
D&P
DTMB
Avondale Shipyard
CONSUNAV
D&P
D&P
Bath Iron Works
D&P
NASSCO
Brix & Kamp A/S
Name
Richard DeVries
Dan Gallagher
Ben Kassel
Watson Perrin, II
Jorge Ribeiro
Kevin Prince
Frank Woronkowicz
Mark Cote
Jack Guilfoyle
Lee Duneclift
Morton Sandvej
Expertise
Team Leader
Structure
MIS Manager
Arrangements & HVAC
Arrangements & Piping
Arrangements & Metrics
Control Systems
Arrangements & Piping
Electrical
Arrangements & Piping
Arrangements & Piping
CAD Team participants were:
Rusty Dupont
Chris Jones
Gene Rice
Paul Rakow
Jesse Rose
Bob Ramsey
Jake Robinson
Nancy Russell
InfoTech
InfoTech
InfoTech
D&P
JJMA
NAVSEA
D&P
NSWCCD
Other resources/expertise utilized on a part-time or rotating basis included: A&T/Vector Research (man- agement consulting); Alfa Laval (fuel treatment);
Allweiler (pumps); Boll & Kirch (filters and strainers);
Crowley Marine (ship operator); D&P (electrical and structural engineering); Maersk Lines (ship opera- tor); and Tranter (heat exchangers). ships. • Within 24 months, to demonstrate the process by design- ing three (later increased to four) world-class engine room arrange- ments. • To achieve customer-focus and buy-in of product design. • To achieve U.S. shipbuild- ing industry-focus and buy-in of process design. • To establish baseline com- mercial ship engine room designs as benchmarks for evaluation of future government-initiated stud- ies. • To document both the prod- uct and process design with ratio- nale for use and further refine-
Structural Machinery Unit utilizing standard secondary structural components; the support structure for the equipment, piping, and electri- cal cabling and components is added. ment.
One medium-speed diesel (MSD) and three slow-speed diesel (SSD) engine rooms were designed in the course of two years. Each article focused on one of the four engine room design products, the evolution of applying the IPPD methodology process, and the lessons learned from each stage of the project.
The first article focused on
SSD#1. The SSD#1 design was a first step in achieving the project goals, which were to develop prod- uct (ship) designs that could be built with a construction schedule reduction of 40 percent (down to 18 months) and acquisition cost
Structural Machinery Unit with Secondary
Support Structure.
Partial Grand Unit fO^V1 tyo*"
Current SSD3
Fuel Oil Piping Arrangement 48 Maritime Reporter/Engineering News