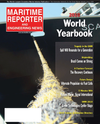
Page 59: of Maritime Reporter Magazine (June 2, 2010)
Read this page in Pdf, Flash or Html5 edition of June 2, 2010 Maritime Reporter Magazine
tanks as it boils off from the cargo tanks.
The gas can then be used in the fuel cells.
Should the contents of the supply tank become low, and BOG is not being pro- duced in sufficient quantities in the cargo tanks, a supply will be created by stimu- lating boil off of the cargo. This involves pumping some LNG out of the tank and passing it through a seawater heat ex- changer to boil it.
With the added power produced from the waste heat recovery system, we pre- dict that we can produce 408 kW per fuel cell stack. Designing to our goal of 23
MW gives us a fuel cell system that in- cludes 56 DFC-3000 fuel cell stacks. The combined weight of the 56 fuel cell stacks is 680 tonnes. Estimating the weight of the auxiliary systems for the fuel cell system, including the fuel, water, reformation, and electrical conditioning equipment, we get a total combined weight of 800 tonnes for the fuel cell sys- tem. So, in terms of weight, it is feasible to use fuel cells for shipboard power.
The weight of the fuel cell system is comparable to that of other power pro- duction plants for the same power output.
Four medium-speed, marine diesel en- gines with the required power output weigh about 576 tonnes. However, this is the dry weight of the engines alone, and does not include the weight of support- ing systems, oils, and fuels. Because of this, we estimate that our fuel cell system will not weigh much more than the total diesel engine system, and may even weigh less. With the rapidly improving technology in this field that leads to more power-dense cells, it is increasingly likely that the fuel cell system will see further reductions in weight before the first commercial application.
For a laden voyage, we predict that 117% of our total required fuel supply is produced by natural boil off gas. This means that the natural BOG will be more than sufficient to power the voyage. The additional BOG can be stored for the re- turn voyage in the holding tanks, burned in the boiler to increase efficiency, or in- cinerated. All of this BOG is accounted for in our economic analysis.
For the ballasted return voyage, we pre- dict that 72% of our total fuel supply will come from natural boil off gas. This means that additional BOG will have to be stimulated. On the return voyage, a “heel”, or small amount of cargo, is left in the tanks of an LNG carrier to main- tain their temperature so as to avoid ther- mal cracking and minimize boil-off during the next cargo loading operation.
Our design requires that a slightly larger amount remain in the tanks, with the extra being allocated for power genera- tion during the return voyage. In addition to stimulated BOG on the return voyage, extra BOG may be left over from the laden voyage and stored in the holding tanks. This could reduce the amount of retained LNG needed for the ballast voy- age, thereby increasing the amount of cargo delivered.
On a round trip voyage, we have esti- mated that approximately 3% of the total cargo loaded is ultimately used as fuel.
This can effectively be treated as a 3% re- duction in the cargo carrying capacity of the vessel, but the cost is offset by the fact that no money is spent on traditional fuel for the round-trip voyage. The ship in Van
Doren’s thesis seems to act similarly, as he makes the assumption that no HFO will be burned in the engines on the round trip voyage and power will be sup- plied primarily from BOG. For our pur- poses we are assuming similar amounts of cargo delivery between the two cases.
Van Doren’s thesis estimated that a
DFDE system would spend approxi-
June 2010 www.marinelink.com 59