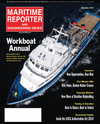
Page 36: of Maritime Reporter Magazine (November 2010)
Workboat Annual
Read this page in Pdf, Flash or Html5 edition of November 2010 Maritime Reporter Magazine
36 Maritime Reporter & Engineering News
The cost of welding plays a crucial role in shipbuilding decisions. Many differ- ent variables affect the total cost of weld- ing, including labor, equipment, consumables, and energy costs. Like in many other industries, the most signifi- cant cost to shipbuilding is labor, where it can represent 80% of the overall manu- facturing cost. For this reason many com- panies focus on this dominant factor when trying to cut costs and increase ef- ficiency. Equipment selection, procedure development, welder training, and au- tomation can be used to significant effect.
As owners demand and designers pro- vide lighter and lower cost solutions, to optimize the in-service life cycle and op- erational costs, shipbuilders need to move to more advanced joining technologies that not only optimize production but also ensure high quality welds that minimize distortion. Distortion can reduce final product quality and increase component assembly cost by increasing labor and corrective actions. Joining procedure and technology investments to improve pro- duction quality (reducing distortion) can be effectively recovered through im- provements in the downline operations.
Aaron Dinovitzer, President, Executive
Engineer at BMT Fleet Technology ex- plains how ship builders can achieve their efficiency and quality goals in the fabri- cation, by designing procedures and prac- tices that produce cost effective results without sacrificing weld or ship build cost and quality.
The common weld is a much maligned beast. Despite the preconception to the layman that welding is a rough, unsubtle industrial process, it is a complex proce- dure where all the parameters must be ad- dressed to achieve a successful end result.
In fact while basic welding tasks can be completed using readily available equip- ment, consumables and procedures, the positive outcome of more complex tasks can only be ensured by deploying the specific technology and knowledge that is available in the market. Advances in naval architecture including the use of thinner section, higher yield steels have put a premium on high-quality welding.
Fatigue has become a major issue so new procedures have been developed focus- ing on ensuring appropriate weldment material and geometric properties. There has also been a move towards advanced containment systems for LNG vessels that require greater attention to weldment quality than for the hull itself. In a com- mercial and project management context, welding deserves proper consideration, not only because of its high labor-cost and proximity to the critical path but also because of the financial implications of getting it wrong.
In order to maxi- mize outputs and minimize risk, BMT
Fleet Technology has developed a value chain that sup- ports the physical welding operation.
The importance of high-quality welders must not be over- looked, but they should also be sup- ported by welding engineers and welding technologists that add value to the process. The welding engineers’ role is to take a broad view of the project includ- ing the proposed or available welding processes and welding technology. Weld- ing engineers tend to lean towards naval architecture or structural systems and op- erate at this level. The welding technolo- gists act to bridge the gap between engineers and welders, often translating theory into practice. They understand the theory behind welding, they understand the equipment and they are themselves, top notch welders. Welding technologists can optimize the technology of the sys- tem and can offer training to suit by op- erating at the production level. By deploying the knowl- edge and experience held by all three of these groups it is possible to consider projects in a far more holistic manner and deliver solutions that provide an innova- tive approach as well as improved effi- ciency or quality.
The parameters that need to be con- sidered range from key design features where a structural connection needs to be made or a combination of materials joined, to selection, storage and use of consumables. Economic factors such as productivity must also be reviewed along with the design of procedures, quality control issues and compliance with regu- latory requirements. There might also be project specific issues such as the need to preserve cladding or material properties during welding operations. The health and safety of the welder must always be a consideration when designing a welded structure. Where options exist, the welder’s position and type of electrodes should be selected to ensure a comfort- able working environment that will aid productivity.
The value chain can also be extended to include the manufacturers of consum- ables such as welding rods and wire.
Welding procedures often refer to a clas- sification of rod or wire. However there are often a variety of options within any given classification. By working closely with consumable manufacturers it is pos- sible to identify which consumables are best for different applications and help the fabricator to select the best consum- ables for the job. This relationship can also drive improvements in quality and technology as it delivers and level of feedback that would otherwise not exist.
Rather than purely relying on empirical methods, BMT Fleet Technology has de- veloped unique numerical modeling and computer simulations that can be used to analyze the welding process or the appli- cation of a weld. By applying specific pa- rameters it is possible to assess the suitability or outcome of a particular welding scenario very quickly and with far less trial and error than traditional methods. The computer simulation also provides a better understanding of the mechanics, physics and metallurgy. One example where computer simulation can pay dividends is analyzing the effects that the environment has on the weld. Any moisture, grease or paint local to the weld can drive hydrogen into the molten metal.
Hydrogen is undesirable as it embrittles the steel when the molten metal has cooled and solidified. To make matters worse, the hydrogen is mobile, in a process called effusion, and is attracted to high stress locations where the effect of embrittlement increases the risk of cold cracking. The rate at which the hy- drogen moves is temperature dependent so in colder weather there will be a longer delay before a crack can be identified by manual inspection. By running the com- puter simulation with all the relevant pa- rameters it is possible to minimize hydrogen cracking risk, minimize the delay time for cracking and for final in- spection, reduce the wait time, and get the structure into service quicker.
COLUMN SHIPBUILDING
A Weld of Difference
About the Author
Aaron Dinovitzer received his
BASc and MASc in Civil Engi- neering from the U. of Wa- terloo where he specialized in probabilistic structural op- timization. He is currently
President of BMT Fleet Tech- nology Limited (BMT Fleet) in
Ontario, Canada.