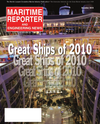
Page 22: of Maritime Reporter Magazine (December 2010)
Great Ships of 2010
Read this page in Pdf, Flash or Html5 edition of December 2010 Maritime Reporter Magazine
Robotics are increasingly penetrating all walks of life, from the military use of
Predator drones and land-based bomb de- fusing systems; to subsea units designed to work safely and efficiently in depths off-limits to man; to consumer’s adoption of innovative floor sweeping and clean- ing units. The common denominator is removing humans from jobs that are po- tentially perilous and dirty, or otherwise undesirable; providing a mechanized means to work more efficiently, safely and effectively, regardless of surrounding conditions.
Enter Chariot Robotics, which is rap- idly working to sow the seeds of its mechanized means to strip paint from ships and prepare its surface with a ro- botic system that can perform the task more safely and efficiently – according to the company’s estimation – than 10 men combined.
Stephen R. Johnson, CEO of Chariot
Robotics, is no stranger to the challenges inherent in shipyard operations. A vet- eran U.S. shipyard executive, much of
Johnson’s career was spent in the coun- try’s leading shipyards, more than 20 years with Bethlehem Steel Corp., and five years as the head of Atlantic Ma- rine’s ship repair and conversion facility in Mobile, Ala. For nearly the past decade, however, Johnson’s efforts have been spent in the development and com- mercialization of a robotics system de- signed to increase the safety, efficiency and environmental soundness of ship’s paint stripping and surface preparation. “We truly understand what the shipyard’s concerns are,” said Johnson during a re- cent visit in the company’s Palm City,
Fla. Office.
Adopting New Technology
As with any new technology – particu- larly a new technology in the tradition- ally conservative maritime market, one that is capital in- tensive that helps to reduce labor – half of the battle in sell- ing a system is sim- ply getting in the front door. “It’s new, and as with any new technology, you have to educate re- garding the system and its capabilities,”
Johnson said.
Used today prima- rily on cruise ships, tankers and above ground storage tanks, the ENVIRO-
BOT™ is equally appropriate across a range of marine ves- sels. Operated by an individual using a wireless joystick control, the robot uses magnetic air gap technology which al- lows it to sweep or full blast, back and forth across the hull’s flat bottom, vertical sides, bow and stern shapes equally. The
System cleans using the energy of water striking the hull’s surface, operating at pressures as high as 55,000 p.s.i. As no abrasives are used in the process, dust pollution does not occur and the need to dispose of spent abrasives is eliminated.
It is the only device that will sweep and spot blast at the same time.
The power and flexibility of the Chariot
Robotics system is highlighted when working, for exam- ple, on a VLCC sta- tioned pier side. “What’s really nice about the VLCC is that, when it’s light, the ship is riding much higher, giving an additional 60 feet or so of ship above the water while pier side. When we’re done working on the pier side, because the system elimi- nates discharge into the environment, we can put the system on a barge and strip the opposite side without moving the ship,” said John Odwazny, COO.
The Chariot Robotics units are not cheap, selling for up to $1m per unit de- pending on the configuration, and John- son admits that as the former head of a ship repair and conversion facility, he would cast a wary eye on anyone walk- ing in the door selling a system at that in- vestment level. But he and his team have meticulously built an analytical case for the investment, estimating that the system essentially pays for itself in as little as two years. In addition, while Chariot Ro- botics touts the unit as a major labor sav- ing device, he has encountered little pushback on this matter from labor, be- cause the robotic system helps to replace one of the least desirable jobs in any ship- yard. In addition, with growing pressure on industries worldwide to ‘clean up their act’ and become better stewards of the en- vironment, the cleanliness – via its closed-cycle waste removal system, with antifouling waste completely contained in vacuum boxes – of the Chariot Robot- ics operation is a major selling point.
While gaining acceptance of new tech- nology is a challenge, Chariot Robotics has met the challenge by building its own fleet of robotic systems and hitting the road, literally to shipyards around the globe, to put its system on display in real- world settings to prove the concept to po- tential clients.
Helping Gibdock Keep Ahead of
Schedule
As Johnson and his experienced mar- itime crew know, nothing sells in the ma- rine business like successful case studies, and the Chariot Robotics team is busy traversing the globe to build awareness and support, proving the value of the sys- tem in helping to get vessels out of dock more quickly.
COATINGS & THE ENVIRONMENTFEATURE
Chariot Robotics
Hull Stripping Robots for Efficiency, Environment
Traditionally, the process of preparing a vessel for painting has been a laborious task, fraught with potential hazards to workers and the environment alike. Chariot Robotics – with its ENVIROBOT™ Ultra High Pressure (UHP) Robotic System – is on a mission to change all of that, forwarding the de- velopment and implementation of its patented robotics technology one shipyard at a time. – by Greg Trauthwein
Stephen R. Johnson, Chief Executive
Officer, Chariot Robotics.