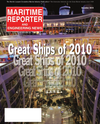
Page 23: of Maritime Reporter Magazine (December 2010)
Great Ships of 2010
Read this page in Pdf, Flash or Html5 edition of December 2010 Maritime Reporter Magazine
“Paint stripping robots magnetized to the bottom of the ship … How cool is that?” – Sean Riley, f020f020 Host of National Geographic’s television series “World’s Toughest Fixes” “When we meet owners and shipyards from around the globe, it is more of a matter of getting the word out to ensure that com- panies are aware of the system and its capa- bilities,” said Eric Johnson, Executive
Director Sales and Marketing.
Joe Corvelli, CEO of Gibdock, the Gibral- tar-based ship repair and conversion com- pany, could be considered the ‘new guard’ in ship repair and conversion. Corvelli, a
Long Island, NY-native and Webb Institute graduate, has in three short years helped to foster a safety and quality management cul- ture on this growing company. First use of the Chariot Robotic’s advanced blasting technology enabled Gibdock to redeliver three Danish-owned containerships that re- quired full hull blasting and coating ahead of schedule. The Gibraltar yard undertook blasting and painting for all three ships within the owner’s time requirements of 29 days. However, Corvelli said that the intro- duction of ENVIROBOT™ Ultra High Pres- sure (UHP) Robotic System from Chariot
Robotics on the third ship made a discern- able difference to work-rates. “The way the
Envirobots work in any position on the hull offers clear scheduling advantages,” said
Corvelli.
The UHP ENVIROBOT™ was used to blast 2,000 sq. m. of hull underwater in the ship’s mid-section, with wetblasting used on the curved bow and stern sections. “The UHP standard is perfect and there is no flash rust due to the combination of vac- uum and warming of the steel during the process, which causes the residual water to evaporate quickly,” said Corvelli. “What im- pressed us was the reliability of the Chariot
Robotics equipment. This has been an issue with some UHP systems in the past.”
Earlier this summer the company was able to demonstrate its system to a very impor- tant potential client, the U.S. Navy, in a
Navy sponsored event in Norfolk, VA. From that demonstration, and through Stephen
Johnson’s and John Odwazny’s longstand- ing contacts with executives at the BAE shipyard in San Francisco, the company re- cently completed a job stripping the paint and preparing the steel on the USNS Tripoli, which was built in the 1960s but is currently used as a missile launching platform.
While opportunities abound in their home country, Chariot views the international ship construction and repair market as most promising. “We see the Middle East as a growth op- portunity for us,” said Stephen R. Johnson,
CEO of Chariot Robotics. “We already have four systems in place at Dubai World Dry- dock, and they are using the systems on some very large ship projects. To date we have done more than 80,000 sq. m. of blast- ing work with our systems.” “We are pleased to have selected this tech- nology for its beneficial environmental fac- tors and to enhance our own productivity,” said Mr. Mohammad Rizal, Director – Pro- duction of Drydocks World –Dubai. “As we become increasingly at home with the oper- ating systems, we will consider upping the number of units.”
Singapore has also proven to be fertile ground. “We are in the hull treatment specification for Petrobras ... we are in their paint and coating manual,” said John Odwazny, COO. “The company is progressing on some very large FPSO conversion projects, and our
Singapore JV operation recently stripped the hull of the P-58, a job that literally saved the owner and the yard 10 docking days. In ad- dition, we have several interesting projects coming up with Princess and Costa cruise lines.”
Ultimately, Chariot envisions itself work- ing in tandem with shipyards to help attract new and long term work by helping to save man hours, drive down the cost of steel strip- ping and prep per square foot, ultimately helping to return the vessel to service more quickly. Chariot Robotics has begun work- ing on new prototype systems that will achieve production rates even higher than their current standards.