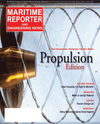
Page 54: of Maritime Reporter Magazine (September 2011)
Marine Propulsion Annual
Read this page in Pdf, Flash or Html5 edition of September 2011 Maritime Reporter Magazine
by Franz Evegren Transport development today is driven by cost-effectiveness. At the same time, improved safety of man, property and en- vironment is of highest concern. FP (Fibre einforced Polymer) composite is a lightweight construction material with ahigh strength to weight ratio compared tosteel. These properties, in combination with low maintenance, lack of corrosion, easy repair, prolonged lifetime and un- leashed design possibilities make FP composite an appealing alternative to steel in maritime applications. By usingFP composites in merchant ships, a re- duction in structural weight of up to 60is achievable, and the lower fuel con- sumption per ton-km payload will make additional costs pay off in short time of operation. Isolation at sea and the fact that FP composite is combustible make fire safety a key issue when considering ship structures in this material. The new SOAS fire safety regulation for alterna- tive design and arrangements provides an opening for these constructions and SPTechnical esearch Institute of Sweden can show several examples of where the novel material has been successfully im- plemented.Authorities, the public and customersare increasingly demanding sustainablesolutions, which will eventually lead to emission trading emerging, giving envi- ronmentally sound transport a competi-tive advantage. While land transport has become cleaner as a result of new regu- lations and new technology, the shipping industry still has a long way to go to re- duce its environmental impact. Accord- ing to recent reports, emissions fromland-based polluters in Europe are ex- pected to be cut in half by 200, but in the same period, emissions from shippingwill double if no actions are taken. The fact that emissions from shipping are in- creasing in both absolute and relative terms makes the problem acute. Prima- rily, the use of fossil fuels needs to be re- duced. Bunker fuel combustion results in atmospheric emissions including air pol-lutants, greenhouse gases, oone-deplet- ing substances and gases that contribute to acidification and eutrophication of both sea and land. A stronger focus on both energy efficiency and environmen- tal competitiveness makes lightweight applications and lightweight designs in-creasingly important. The lighter the ves- sel, the more it can carry, or the less energy it needs for propulsion. A suc- cessful project where this became prac-tise was in the development of two inland ships purchased by the Swedish shipowner Styrsöbolaget. They were required to cut transportation times in half andwere therefore built in FP composite. They are now the two first fully certified carbon fibre SC vessels in the world. As expected, during their first year of oper- ation in the archipelago of the Swedishwest coast, they decreased the time of transport by 50, but the fuel consump- tion is still the same as for previous ves- sels, which is remarkable. As above, a reduction in weight can significantly re- duce the energy necessary for propulsion. This applies not least to many ships today that carry additional keel weight in order to increase stability. If the vessel is large and the weight is reduced high up in thesuperstructure, several times the reduced weight may also be possible to withdraw from the keel (still achieving the former stability). In other cases, it is more oper- ative to be able to utilie the weight-sav- ings to carry more cargo or passengers. Any technique that allows an increase of the pay load/displacement ratio is obvi- ously economically interesting.In the research project ASS, investi- gations were done to see how much the weight could be reduced in different lightweight construction applications. Itwas found that a reduction in structural weight of up to 60 is achievable when replacing steel or aluminium construc-tions with FP composite in load-bear- ing structures, not considering areduction in keel weight (final report, 20091, is available at www.sp.se under publications; see also www.lass.nu). Another advantage of the FP com- posite material is the possibility to createcomplicated -dimensional forms that would be very expensive to produce in a metallic material. ence, the particulari- ties of the FP-material make it possible to reconsider basic ideas in ship design. Itwill also reduce the need for maintenance(no rust) and repair. Both from different design perspectives as well as from envi- ronmental and economical viewpoints, lightweight FP composite is an appeal- ing alternative shipbuilding material compared to conventional steel. ow- ever, the fact that load-bearing steel struc- tures will be replaced by FP composite, which has some characteristics very dif- ferent from steel, also implies new risks and invokes assessments of the impact on safety, environment and property. ASSESSN E MPAC F FP CMPSE CNS UCNS isks during building, operation and disposal of a ship with FP constructions will inevitably be, not necessarily greater but, different. A reduction in topside weight, implied by the lightweight mate-rial, could for example have a positive ef- fect on damage stability and thus reducethe risks entailed with collision andgrounding. Further increased building costs may on the other hand increase fi- nancial risks whilst disposal and recy- cling is still an area of research.Knowledge in how a FP construction will possibly affect economical and envi- ronmental risks is imperative. All new risks must be viewed in light of the ben- efits of the new construction and be eval- uated over the whole lifetime of a ship. This is generally investigated in ife Cycle Assessment and ife Cycle Cost Assessment. The former covers the im- pact on the environment from all parts of the life cycle; from the initiation and pro- duction phase via the operation phase andto the disposal of the ship, and the latterinvestigates the economical impact over the ship lifetime. The analyses have been performed for FP composite construc- tion applications in the research projectsASS and ASS-C (final report, 201112, at www.sp.se). In general they show that the environmental costs will be significantly lower than for steel ships and that additional costs will pay back inshort time of operation. The growing concern regarding envi- ronmental impact and increasing fuelcosts make lightweight material for ship building seem as an inevitable path for development and the performed life cycle assessments show that FP composite solutions are sustainable. owever, the use of such material is impeded, not onlyby technical difficulties, but also by in- ternational regulations. The fact that FP composite is not considered non-com-bustible, a foundational requirement in SOAS, makes fire safety a key issue when considering ship structures in thismaterial. There is, however, a way for- ward. AN PENN N M FE SAFE EUANS Fires have always been feared on ships. owever, the fire itself is typically not the primary danger to people onboard. The number one cause of death related to fires is smoke inhalation. The special condi- TECHNOLOGYINSULATIONS The Future: Lightweight &Risk-Based 54Maritime Reporter & Engineering News LeftThe first fully certified HSC vessel in FRP composite in the world,Valö, was built to cut transportation times in half without increasing fuel consumption.RightThe SOLAS regulation for alterna- tive design and arrangements forfire safety requires an analysis of plausible design fire scenarios.