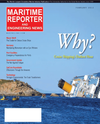
Page 47: of Maritime Reporter Magazine (February 2012)
Cruise Shipping Annual
Read this page in Pdf, Flash or Html5 edition of February 2012 Maritime Reporter Magazine
(reference 1: ?Surface Piercing Propellers for Displac- ing Vessels? Ferrando, Panarello, Scamardella, Viviani). While there are significant differences in their design approach, particularly with respect to propeller submer- gence parameters, the Interprogetti example is a land- mark in demonstrating both the feasibility and theperformance potential of PSP application to displace-ment hull ships.FURTHER RESEARCH The preliminary results validate the overall belief that this type of drive system can be successfully adapted to large, fully-displaced hull forms. As model testing of individual hull shapes can be very expensive, a numer- ical prediction approach is presently being pursuedbased on the initial findings. Flexitab, in collabora-tion with sister company Victory Design, are presently developing specific analytical tools in the form of proprietary software to standardize the test- ing protocols, which will incorporate advanced vir- tual fluid dynamic analyses. The aim is to provide a unique set of computations that will allow the predic- tion of performances and efficiency gains when retro- fitting existing ship hull forms with the K-Drive PSP system. The tools being developed will take into con- sideration the amount of fuel burn reduction likely to be encountered, the overall projected installation and op- erating costs for specific vessel types based on age, re- maining useful life and operational considerations, suchas intended use. One area that shall need further inves- tigation is the transmission of power from the engine to the propellers. In the case of PSP, the nature and opera- tional characteristics of their design tends to induce agreater degree of cyclical loading on marine transmis- sion components as compared to fully submerged pro- pellers. The blades of a PSP operate both submerged, when maximum loading occurs, and ventilated, where loading is essentially zero. The resultant variations of the stresses coupled to the transmission gear could resultin fatigue, vibration and resonance problems transmitted to the hull, stern gear and the gearbox. While this has not been fully explored in the preliminary stages of the design application where larger classes of vessels are concerned, previous experience with the M.V. ?Alnilam? tend to suggest that technical solutions to these issuesare at hand. The final production solution will require an additional program of testing and development to cre- ate a new family of partially submerged propellers based on the initial designs by Sonny Levi. The new family of PSP would of course be tested at a suitable facility, such as the Genoa modified tunnel, in order to derive all the data and curves essential for proper hull to propeller matching.The axiom of the naval architect is that all designs are a compromise, and this is true when discussing the ap-plication of the PSP K-Drive from Flexitab as installed on large displacement commercial vessels. Not all classes of vessels will be ideal candidates. For example, certain types of bulk carriers and tankers, where the op- erational change in drafts between the loaded and bal-lasted condition entail large vertical excursions would initially not seem to be suitable. On the other hand,more research might show ways of getting around this issue: the flow control plane inserted between the transom and the propeller of the K-Drive did prove very effective at various drafts during the model tests.Presently, the ideal type of vessel envisioned for this propulsion system is the large and medium sized container vessels, RoRo passen- ger ferries (with transom ramp modifications) and Cruise ships. Cruise ships are uniquelyadaptable since their typical overhanging flat tran- som design lends itself well to the K-Drive system. In addition, the chance to reduce operating andmaintenance costs as well as lessening environ- mental impacts should appeal to their inherentlygreen nature. It should be borne in mind that whilethe initial effort for this project has been towards the modification of existing vessel designs, it is cer- tainly not limited to such. The technology is equally adaptable to new construction. In fact, new construction affords greater opportunity to benefit from the projected reduced fuel consumption andpropeller maintenance costs when factored into the life expectancy of new vessels. Incorporating the structural details necessary for the K-Drive mount- ings, transmission gearing arrangements as well asthe engine plant layout is more easily accomplishedin the preliminary design phases.Increased efficiency aside, one has to acknowl- edge that economical cost factors will play the major role in whether or not an owner would chose to fit or retrofit this type of propulsion system to a new or existing vessel. In some cases the potential to recoup the installation costs would not be possi- ble given the remaining useful life expectancy of a particular vessel. This is one of the prime areas that Flexitab is presently working towards with the develop of the tools necessary to identify all possi- ble cost factors so that a potential owner can make a valid assessment of the financial risks involved in pur- suing the state of the art in marine propulsion. Flexitab is confident that this innovative design will be success- ful and, buoyed by the encouraging preliminary results thus far, have filed for European and International patents based on the K-Drive principle. On-going re- search and developmental work is continuing and fund- ing has been sought through various European grant programs in order to sustain the drive to bring this tech- nology to fruition.February 2012www.marinelink.com 47K-Drive A Next Generation Propulsion System(Continued on page 41)MR Feb.12 # 5 (42-48):MR Template 2/7/2012 10:13 AM Page 47