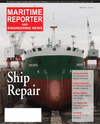
Page 60: of Maritime Reporter Magazine (March 2012)
The Ship Repair Edition
Read this page in Pdf, Flash or Html5 edition of March 2012 Maritime Reporter Magazine
liver this package as soon as we can back up the numbers and corresponding data,? says Booty Cancienne, production super- intendent for Textron Marine and Land Systems (TM&LS) in Slidell, La.Cancienne is production supervisor forthe TM&LS shipyard with four decades of experience. He?s worked at TM&LS for 35 years, and five more at other yards. He is responsible for all marine con-struction at TM&LS, including develop- ment of all processes, materials andmetals used, training of employees and schedule and cost for all programs. Hehas overseen the construction?and later the refurbishment?of dozens of Navy LCACs (landing craft air cushion). In his job, he makes recommendations for en- gineering changes to reduce cost and toimprove construction fabrication. At the workshop, when it came to welding, his was the voice of experience. Most recently, he has been involved in the TM&LS proposal for the T-Craft in- novative naval prototype being investi- gated by ONR. TMLS has fabricated a T-Craft side-hull section of aluminum, and will build the same structure from ti- tanium to provide comparison data. Cancienne says a titanium hull is pos-sible. ?We in industry must make the fear of high cost go away. We have to develop some processes to reduce cost and turneveryone?s attention to the customers? needs and how to meet commercial and Navy requirements.? The business case While a number advances have been made in processing, design, and fabrica- tion, the hurdles that the Navy faces re- garding the use of titanium are the same hurdles that we faced 10 to 20 years ago. ?It all boils down to material and fabri- cation costs. Until the program offices can overlook the acquisition costs asso- ciated with using titanium componentsand see that the long term benefits out- weigh the acquisition costs, there willstill be hurdles to using titanium,? says Kim Tran, a materials engineer at NSWC Carderock where she is the non-ferrouswelding lead.Tran says an all titanium ship is not re- alistic until industry can reduce the costof material to a more affordable price. ?In the past, $4 /lb was the target price for the DARPA low cost titanium initia- tives,? she says. ?With regard to titanium applications, if industry can reduce thecurrent material prices, there may bemore opportunities for titanium compo-nents on Navy ships. Reduced fabrica- tion costs are also important. Traditional processes for fabricating titanium com- ponents are expensive because of the cleanliness requirements for the handlingof titanium and complete shielding re-quirements for arc welding. Technolog- ical advances to reduce fabrication costs yet still enable the fabrication (casting, welding, forging) of quality products that meet design and material properties re-quirements will also enable more oppor- tunities for titanium applications on Navy ships.? To reduce fabrication costs, Tran says more research is needed to reduce thecurrent arc welding shielding require-ments. ?Complete inert shielding duringarc welding is the biggest cost driver as- sociated with welding titanium. In thepast, NSWCCD has investigated flux cored arc welding wire and using a fluxpaste to eliminate the requirement forbackside shielding. These were limited studies that should be revisited. Higher productivity welding techniques such as gas metal arc welding (GMAW) and hot wire gas tungsten arc welding (GTAW) should also be researched. GTAW is the primary welding process for welding ti-tanium because it is much cleaner; how- ever it is also a low deposition process requiring more weld passes to complete ajoint than GMAW. Using GTAW results in increased fabrication time and cost.? Walker agrees that more study is need to make the business case for a titanium ship, ?A credible business case study would be a significant accomplishment to solidify the benefits of titanium vessel fabrication and drive titanium into con- sideration for new vessel designs.? As an example, Walker points to the aerospace industry, which he says under- stands lifecycle ownership cost and has justified gas turbine engine investments to achieve thrust and fuel efficiency im- provements. ?Increased thrust relates to increased payload or passenger capacity. Fuel efficiency benefits rapidly multiply into very large life-cycle cost savings for both military and commercial aircraft. A similar case exists for a titanium vessel in terms of maintenance, corrosion man-agement, reduced painting and coatingrequirements, lower vessel weight, fewer shipyard visits, longer service life, and so on.? Existing shipyards view titanium as a specialized process that is a cost burden over the state of fabrication for steel, Walker says. ?A business case could also be supported by the fact that titanium vessel fabrication should be performed in an aggressively lean environment of a ?small shipyard of the future,? where ma- terial handling, welding practices and en-vironments, material flow, and modular construction methods are optimized to ti-tanium to drive down costs and are biased to light metal fabrication (aluminum and titanium). ? Cancienne says the Navy will save a tremendous amount of money with tita- nium ships just in upkeep of the hulls alone. It?s an issue of cost versus longevity. ?This is the bottom line,? he says. ?If a hull lasts 50% longer, say 60 years in- stead of 40, you get the same service lifeas three conventional hulls for price of two titanium ships. Upgrades in elec- tronics, machinery and propulsion are alot cheaper than building a new ship.? ?Titanium is a common metal, it is eas- ily formable, very weldable, has excellent strength, and is corrosion resistant,? Walker says. ?A titanium vessel is ab- solutely possible. There are plenty of pockets of titanium design and fabrica- tion expertise in industry that are pro- ducing titanium structures every day. Very little of this expertise resides in tra- ditional shipyards.? BoldMar, Inc. plans to build mega- yachts and commercial vessels at NASA once fabricated shuttle fuel tanks, and the Aries capsule is being built today using state-of-the-art welding techniques. The Michoud facility is also home to the Na- tional Center for Advanced Manufactur- ing, which is leading the way in new materials and welding methods, includ-ing friction-stir welding. Friction-stirwelding welds mated metal pieces with-out melting them, causes less damage to60Maritime Reporter & Engineering News FEATURE MARINE MATERIALS MR March 12 # 8 (56-64):MR Template 3/2/2012 8:40 AM Page 60