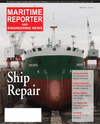
Page 61: of Maritime Reporter Magazine (March 2012)
The Ship Repair Edition
Read this page in Pdf, Flash or Html5 edition of March 2012 Maritime Reporter Magazine
the materials, and can be automated withprecision results.BoldMar has embraced friction-stirwelding and is able to use one ofNCAM?s three $20 million friction stir welding machines. ?This process will re-duce fabrication time by 40% and elimi- nate a majority of the harmful flash andfumes associated with fusion welding fora cleaner work environment,? Bolderson says.More importantly, friction stir welding could be very advantageous over fusion welding processes for joining thin tita-nium plates and structural forms fromboth weld quality and distortion controlpoint of view. Bold-Mar production of vessels is pri- marily of aluminum, but has its sights on building vessels from titanium, including offshore patrol and service vessels. Moving forward with titanium may be what America?s shipbuilding industry needs, Bolderson says. ?America today is an uncompetitive, third-rate shipbuild- ing nation, unlike what we were 70 years ago. Building in titanium will leap-frogus ahead of other nations in utilization ofTi as a superior material for shipbuilding; and using automated production tech-nologies will help re-establish America as a competitive and premier shipbuild- ing nation.? At UNO, Dr. Dong and Larry DeCan are leading an ONR-funded program on"Manufacturability and Structural Per- formance of a Titanium Mid-Ship Sec- tion." This program will advance the science and design/fabrication technolo- gies by constructing a full scale titaniummid-ship hull section. Dong and his teamare investigating structural performance assessment techniques and advanced metal fabrication technologies. ?To my best knowledge, this summit is perhaps the first of its kind,? says Dong. ?The workshop provided a terrific forum for experts of all related disciplines to ex- change experiences and ideas on how to make titanium a viable and cost-effective material for ship structure applications. Ithink we came out of the meeting with amuch more optimistic feeling that tita-nium ship structures will become a real-ity, sooner than we expected before the meeting. At this Summit, we got to know who is who in all relevant technological areas and major research and develop- ment initiatives in industry and academia. More specifically, as the Principal Inves- tigator of the ONR titanium mid-ship program, I?m very much encouraged that our approach and major findings reported at the meeting were validated by leading experts from various technical fields. Furthermore, insights provided by ex- perts on various unresolved technical is- sues will help us at UNO to devise research plans to attack some of the areasimmediately.? Dong agrees there are challenges, in-cluding the lack of experience in build- ing large-scale Ti structures and the lack of high-productivity Ti welding processes. He says Ti is also prone to buckling and distortion. But the biggest obstacle is cost. ?The key is reasonably priced titanium for ship hull applications.Aerospace grade Ti is not what we need,? he says.The ONR mid-ship section project willfocus on advanced fabrication and join- ing processes, such as high productivity MIG and friction stir welding processes;math-based design-for-fabrication methodologies; creating a database forsupporting welding process development and structural performance evaluations; development of fit-for-purpose-based definitions of ?ship hull? grade titanium or alloys and weld quality acceptance cri- teria through a test article construction.In addition to UNO, the team includesTM&LS, Keystone Synergistic Enter- prises, and MiNO Marine.?We are using some of the most ad- vanced modeling tools to save time and material costs in researching enablingtechnologies for building titanium ship structures,? Dong says. Chris McKesson, a naval engineer with over 20 years of high-speed craft design experiences (currently working on his Ph.D. thesis at UNO) says the ONR-sponsored research at UNO is developing mathematical models for practical prob-lems like welding. ?Dr. Pingsha Dong?s math-based approach gives designers in- sights that had not been explicitly avail- able previously; and provides it early enough and clearly enough to be taken into account early in the design process.It?s not surprising that we are driven to this type of modeling when using an ex- otic material like titanium, but I look for- ward to these same design techniques becoming ubiquitous, even in steel and aluminum shipbuilding.? Attendees noted that developing speci- fications for marine grade titanium was starting with a ?blank sheet of paper.? Ron Williams of Allegheny Technolo- gies Incorporated (ATI), a company that supplies mission-critical metallics, saysATI?s relatively new ATI 425® Alloy is cold-rollable, a less costly method ofmaking large flat plates that can be used in ship construction. ?Everybody talks about total ownership costs, but the thing that always gets in the way is initial acquisition cost,? Williams says. From a capacity standpoint,Williams says his company is ready to take orders. ?We don?t see capacity as an issue today.? ?We?ve got to get Ti down to a more af- fordable basis,? Williams says. ?We need standards, specifications and inspection techniques to be quick to market and keep costs in line.? Mys-ti-queAccording to Bolderson, there is a mys-tique surrounding titanium vessels and this scares potential buyers. ?The estab- lished shipyards are the biggest skeptics and this hurts potential development. I can only speak from my own experience in trying to bring a Ti project to reality. The shipbuilding industry is conservative and is reluctant to try new designs or ma- terials,? he says. Bolderson says the Navy has a prefer- ence for ?parent? designs. ?In mostcases, a foreign vessel design is chosen because it represents newer design fea- tures than anything available in the USA. In 2007, BoldMar approached Textron Land & Marine Systems to consider a Ti joint venture bid on the new USCG cutter that was eventually awarded to Bollinger Shipyards. BoldMar and Textron both re- alized prior to the RFP submission thatthe "parent vessel" issue would negate a Ti vessel being considered. The economics of inflation also is a fac- tor. Moore?s calculations suggest that the benefit in TOC is reduced, but by no March 2012 www.marinelink.com 61MR March 12 # 8 (56-64):MR Template 3/2/2012 8:41 AM Page 61