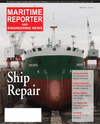
Page 71: of Maritime Reporter Magazine (March 2012)
The Ship Repair Edition
Read this page in Pdf, Flash or Html5 edition of March 2012 Maritime Reporter Magazine
Modern coatings systems traditionally have served as guardians of the vessel, the first line of defense in keeping lifecy- cle maintenance costs in check versus the highly corrosive marine environment. While ship owners still count on new, ever-better formulations designed to go on faster and easier, last longer, and pro- tect the vessel and environment, manu- facturers today are increasingly proving coatings systems value to help reduce fuel consumption and emissions. In addi-tion, new regulation, specifically the new IMO Performance Standard for Protec- tive Coatings (PSPC) rules for cargo oil tanks set to go into force in January 2013, has all majors busy proving prod- uct performance. On the mission to dis- cover recent innovations from coatings makers, MR reports. ClassNKrecently awarded type ap- proval for the world?s first alternative coating system under PSPC (Perfor- mance Standard for Protective Coatings) for ballast tanks to a single coating sys-tem manufactured by Nippon Paint Ma- rine Coatings Co., Ltd., which was the first to be issued by any classification so- ciety anywhere in the world. Under PSPC, conventional epoxy coat- ing systems are required to comprise two coatings. The standard does however in- clude a provision which allows for alter- native systems, such as the one approved by ClassNK, with only a single coating.A key function of the system developed by Nippon Paint Marine Coatings is the ?SI (Self-Indicating)? feature wherebythe color of the coating changes depend-ing on its thickness. The application of this coating system to ships will begin upon confirmation from relevant admin- istrations by ClassNK.The PSPC standard provides technical requirements for protective coatings in dedicated seawater ballast tanks of all type of ships of not less than 500 grosstonnage and double-side skin spacesarranged in bulk carriers of 150 m in length and upwards for which the build- ing contract is placed, the keels of which are laid or which are delivered on or after the dates referred to in SOLAS regulation -1/3-2 as adopted by resolutionMSC216(82).Jotun reports that it completed testingof coating systems consistent with thenew IMO PSPC rules for cargo oil tanks (COT), scheduled to come into force next year. The new IMO PSPC rules for cargo oil tanks (COT) will go into effect Janu- ary 2013. Focused on maintaining the long-term integrity of tanks, the new standard requires that all coatings used inthe tanks must provide long-term protec- tion against the corrosive effects of crude oil. Jotun has successfully completedtesting for coating systems at one of theIMO-approved test institutes (COT in the Netherlands), passing with several tank coating systems. Two test methods are used. The first test simulates the compo- sition of the vapor phase in crude oil tanks both in ballast and in fully loadedcondition. The second test simulates im- mersion in a crude oil tank with a modelliquid developed to replicate some of the most corrosive crude oils. According to Jorunn Holdhus Skovly, Jotun?s Product Manager for tank coat- ings, Jotun coating systems performedwell in these rigorous test. ?Jotun wel-comes the IMO regulations as they en- sure a given standard for the whole coating process, from steel preparation tocontrol measures,? she says. ?Type ap- proval for coating systems ensures that our customers can trust they are selecting appropriate and high-performance coat-ing systems, fit for purpose.? While new innovation is central to In-ternational Paint?s market leadership, reflection on the track record of a proven product is instructive as well, as is the case with its Intershield 300. The com- pany reports that Intershield 300 contin- ues to prove its durability in service, remaining in excellent condition after 15 years in the cargo oil tanks of the Samco Raven. The 301,653 dwt crude oil tanker had the upper and lower areas of her cargo oil tanks coated with the abrasion resistant,aluminium pure epoxy coating Inter- shield 300 immediately after delivery in June 1996. At its third special survey and planned maintenance at Yiu Lian Dock- yard (Shekou), China in 2011, nine of its 15cargo oil tanks were assessed and the coating condition was rated as excellent throughout. In addition, very little break- down was observed on edges, weld seams, cut-outs and scallops throughoutthe tanks with only a small number ofminor, isolated spots of corrosion pres- ent. No breakdown was visible directly above, at or below the cargo load lines and the coating was in excellent condi- tion in areas surrounding bellmouths andon sharp edges around cargo wells. ?After 15 years in service the coating is in very good condition; in fact, better than good,? said François Rascle, Super- intendent, V. Ships France SAS, who su- pervised the drydocking. ? The tanktops are in excellent condition with very few areas of breakdown.? ?The condition of the cargo oil tanks was astonishing after 15 years in service. With the IMO PSPC for Cargo Oil Tanks being introduced in 2013, this outstand-ing performance can give vessel owners confidence that when they select Inter- shield 300 as the anticorrosive protection system for their cargo oil tanks, they are investing in a coating that is proven to meet and exceed legislative requirements. With only minimal repairs, the coating is set to continue protecting the cargo oil tanks for many years to come,? said An- drew Cass, International Paint Business Development Manager. In January 2012, Intershield 300 passedthe demanding IMO PSPC Cargo Oil Tank laboratory tests in accordance with IMO MSC.288 (87) SOLAS regulations for cargo oil tankers. Fuel & Emission Savings The push from coatings manufacturers in the past few years has been a focus on the correlation between coatings and sav- ings on fuel use and emissions. Fuelprices have risen and maintained an ele- vated level, even in the face of global eco- nomic stagnation; and the globalshipping industry is faced with increas- ing mandates to reduce emissions.PPG Protective & Marine Coatings (PPG), for example, touts its SigmaGlide biocide-free system with guarantees onfuel savings. According to the manufac- turer, the SIGMAGLIDE system is proven to deliver cost reductions for new- build or dry docking and, with the launch of SIGMAGLIDE 990, offers guaranteed fuel savings of 5%. (PPG does note that Jotun Passes IMO PSPC for Cargo Oil Tank (COT) Tests. (Photo: Jotun)March 2012 www.marinelink.com 71MR March 12 # 9 (65-72):MR Template 3/6/2012 12:47 PM Page 71