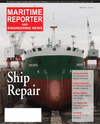
Page 72: of Maritime Reporter Magazine (March 2012)
The Ship Repair Edition
Read this page in Pdf, Flash or Html5 edition of March 2012 Maritime Reporter Magazine
final savings percentage achieved is sub- ject to the average speed and operational activity of the vessel, but it offers tailored cost saving specifications on request). Since the launch of the first generation SIGMAGLIDE in 1995, PPG has contin- ued a course of investment and develop- ment in the range, up to and including thelatest system, SIGMAGLIDE 990. This is a third-generation, pure silicone-basedfouling release system that offers en- hanced slime release properties and highvolume solids. As with other coatings system suppli-ers, PPG is driven to help reduce fuel consumption through the reduction offrictional resistance of the underwater hull. PPG claims that SIGMAGLIDE 990 reduces frictional resistance to the pointwhere fuel savings can be realized. The system is based on two coats of epoxy: the first being the primer and the second being an anti-abrasive coating; this is then followed by a tiecoat, SIG- MAGLIDE 790, and then a topcoat of SIGMAGLIDE 990. A key advantage is that this two-component system, with the volume solids content of the tiecoat at 72Maritime Reporter & Engineering News You?ve seen the claims from providers of marine coatings time and again?3% ? 5% ? 10% fuel & emission savings. With the number of variables that conspire to impact fuel economy of moving a ship from ?point A to point B? ? the weather, traffic, ma- chinery performance and quality of fuel to name but a few ? how can you be sure that Coating company claims are valid? International Paint, a leader in the market, set out to set the record straight. Specifically, International Paint, in conjunction with BMT Argoss, sought to tie strong academic research and ship operating evidence of the correlation between applying specific fouling control coatings and reduc- ing fuel consumption and CO2 emissions finds further backing, to prove the value of coatings to the ever in- creasing need to reduce ship fuel consumption andemissions. The pair came together and will use the new BMT SMARTSERVICES system to verify, through inde- pendent monitoring and software analysis, the contri- bution to vessel performance, fuel savings and reduced emissions made by International Paint?s highest per- formance fouling control coatings, Intersmooth SPC(self polishing copolymer) antifouling and Intersleekfoul release coating.International Paint claims fuel and emissions sav- ings for its Intersmooth SPC coating, citing evidence gathered from over 5,000 vessel drydock and inspec- tions for fouling rating, combined with AHR (average hull roughness) measurements. Behind this specific argument, the International Paint ?Dataplan? system has coating details of over 1.7 billion DWT, representing almost 200,000 drydock- ings that allow antifouling performance to be predicted and assessed. Results are derived from analyzing the in-docking condition of a vessel, its coating perform- ance and assessing the type, severity and extent of any fouling, if present. In conjunction with the vessel?s trading pattern, operational profile and drydocking in- terval, an antifouling performance rating can be cal- culated. Dataplan also records the vessel's coating con- dition, including the type, severity and extent of any corrosion, cracking, blistering, detachment and me-chanical damage, all of which contribute to and are in- cluded in, hull roughness measurement. International Paint also cites the report, ?Energy and GHG Emissions Savings Analysis of Fluoropolymer Foul Release Hull Coating,? dated December 10, 2010, by Professor James Corbett?s Energy & Envi- ronmental Research Associates. The report analyzed the latest fuel consumption data of three vessel types coated with Intersleek900: Prem Divya, a single en- gine 21,126 HP tanker; Ikuna, a twin engine 3,400 HP bulker; and five identical post panamax container ves- sels, three of which were coated with SPC antifoul-ings and two with Intersleek 900. The results are remarkable for the correlation they show between the coating applied and the fuel con- sumed. The report showed that fuel consumption was reduced by 10% on the Prem Divya, 22% on the Ikuna and by 5% in five container vessels (based on all five ships carrying a comparable load). The report stated that if similar fuel efficiency results were realized by all tanker and bulk cargo vessels within the commer- cial fleet that: "annual fuel oil consumption could bereduced by roughly 16 million metric tons (MMT) peryear, fuel expenditures could be reduced by $4.4 to $8.8b per year, and nearly 49 million tons of CO2 emissions could be avoided annually?. At a more detailed level, the report stated that the latest generation fluoropolymer foul release coatingcould offer average fuel and emissions savings of up to 9%.Proving Coatings Performance Coating performance is an integral part of whole vessel efficient operation, as a recent study by International Paint and BMT Argoss found. TECHNICALCOATINGS & CORROSION CONTROL MR March 12 # 9 (65-72):MR Template 3/6/2012 12:48 PM Page 72