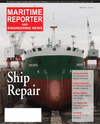
Page 73: of Maritime Reporter Magazine (March 2012)
The Ship Repair Edition
Read this page in Pdf, Flash or Html5 edition of March 2012 Maritime Reporter Magazine
79% and the topcoat at 80%, consider- ably reduces packaging waste costs and reduced solvent emission at application. Hempelis another global coatingscompany that has worked hard to prove the value of its product in helping shipowners save money. While it also of- fers volumes of technical detail and spec- ification, perhaps its greatest proof came last year when United Arab Shipping Company (UASC sailed nine newbuild containerships directly from the new- building yard ? Samsung Shipyard in Korea ? to drydock for recoating with its Hempasil X3 immediately after delivery. With bunker fuel costs rising to record triple-digit highs and drydocking inter- vals now up to 90 months, ship owners and operators are realizing the value of new generation of fouling release sys- tems. Guaranteed fuel savings, lower CO2 emissions, less time in drydock andmore time in the water ? these are just some of the benefits offered by HEMPASIL X3 system. The HEMPASIL X3 system, particu- larly on vessels that typically use $90,000 of bunker fuel per day for example, can save at least two percent of fuel per day, making the payback period on the coat-ing system less than five years. In addi- tion the contract includes the one-coatNEXUS X-SEAL tie coat solution, theSea Trend fuel consumption data moni- toring software and the HEMPASIL HELIX propeller coating, maximizingfuel saving efficiencies and constantly monitoring them.?Umm Salal? was the first of the nine UASC A13 newbuilds to drydock in Shanghai in April 2011. First a conven- tional antifouling coating is applied to thenine 13,000-TEU capacity containerships at the Samsung shipyard before proceeding for a sea trial. The newbuilds then sailed to Shanghai, where they are hosed with high-pressure fresh water in preparation for the HEMPEL NEXUS X-SEAL tie coat, which seals the existing antifouling coating and ensures thatHEMPASIL X3 adheres perfectly to the anti-fouling coating applied in Korea. Ecospeed Non-Toxic Fouling Control Ecospeed is a hard, inert, specially-for- mulated glassflake vinylester resin sur- face treated coating system that includes routine underwater cleaning without the risk of chemical pollution to the environ- ment or of damage to the coating.Ecospeed can be cleaned aggressively and rapidly and will only improve in smoothness with each cleaning.One of the unique factors of this un- derwater hull coating system is that with repeated underwater hull cleaning, the coating?s surface aspect does not degrade but gradually improves. This procedure is made easy by the coating?s technical properties. Cleaning can be carried outwhenever needed, at any point in its lifes- pan, without causing damage.Regular underwater cleaning of the coating results in improved hull smooth- ness each and every time the hull is cleaned. Tests have shown that a very large number (+500) of repeated under- water hull cleanings improves its surface texture without any adverse effects. In addition, and particularly relevant in today?s market, Ecospeed is suited for ships which have a stationary period be- cause an impermeable barrier is createdduring application. This gives the coating its excellent and durable anti-corrosive properties and protects the underwater hull against mechanical damage. In 2008, stringent tests were carried outwithin the framework of an EU LIFE demonstration project to provide scien- tific data and to authenticate the non-tox- icity of the Ecospeed hull performancetechnology. This research proved that the coating is 100% toxin-free and that thereis no negative effect on the water quality or the marine environment at any point of its application or use. Moreover, the mas- sive amounts of VOC and zinc anode emission associated with conventional hull coating systems are reduced to al-most zero. March 2012 www.marinelink.com 73Hull CleaningMachine OK?dfor Use in Vancouver Port The global shipping industry remainsstuck between international and re-gional regulatory requirements and ef- ficient cost effective ship operations. Environmentalists continue to keep ships in the spotlight by focusing their at- tacks on the air pollution produced by ships. Regional and local port authorities remain focused on keeping their waters free of invasive species and metals like copper, nickel and other harmful chemicals potentially released during routine hull maintenance cleaning and propeller polishing. Considering that more andmore local port authorities are closing the door on hull cleaning and propellerpolishing, the Subsea Solutions Alliance has been focused on finding methods of performing these maintenance items in an environmentally friendly way that keeps regulatory authorities happy and customer ops efficient. Investing more than two years of time and resources and almost a $1m into the R&D program for an innovative method of Hull Cleaning, the Subsea Solutions Alliance announced that its environmentally friendly cleaning machine has been approved for use in the port of Vancouver, Canada. With the port of Vancouver, Canada being closed to hull cleaning for several years now, the Subsea Solutions Alliance saw a mar- ket need, strengthened by the fact that customer inquiries for this service contin- ued to pour in to All-Sea Enterprises LTD, the Subsea Solutions Alliance member company in Vancouver. With many customers making trans-pacific transits once they leave Vancouver, the owners were interested to have proper hull maintenance performed in order to save fuel and flat line their operational costs. As such, the method of hull cleaning has been established to capture the spoils produced dur- ing the hull cleaning process and properly disposed of through a process approved by the regulatory bodies of Vancouver, Canada, which has been employed on sev- eral vessels already in Vancouver with successful results. MR March 12 # 9 (65-72):MR Template 3/6/2012 12:49 PM Page 73