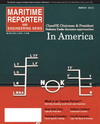
Page 46: of Maritime Reporter Magazine (March 2013)
U.S. Coast Guard Annual
Read this page in Pdf, Flash or Html5 edition of March 2013 Maritime Reporter Magazine
46 Maritime Reporter & Engineering News ? MARCH 2013 TECHNICALCOATINGS & CORROSION CONTROL The advance of modern marine coatings and related technologies is not unlike other technical sectors of the maritime industry, primarily driven by emerging regulation from the international, national and regional level, usually in regard to environmental concern.But in recent years, an increased focus on the reduc-tion of marine emissions in tandem with the capability to more directly correlate clean, well-maintained hulls with reduced fuel consumption and lower emissions has driven the industry further faster, as coatings manu- facturers globally strive for new formulations designed to apply easier, wear longer and ultimately become an indispensible tool in the vessel owner?s arsenal to run cleaner, more ef Þ cient vessels. The CoatingsLate last year Hempel launched Hemparea 55973, a fast-drying anticorrosive coating suitable for C3 corro-sive environments with a cure time of just one hour. Its quick dry time, along with a single-coat combination of primer and topcoat, increases line-speeds for heavy machinery by at least 50% in comparison to standard two and three coat systems, the manufacturer claims, helping to complete the coating process in a timelier, more cost-efÞ cient manner. New to the market are International Paint?s two latest antifouling coatings, Intercept 8000 LPP and Intersleek 1100SR. Intercept 8000 LPP, is a biocidal linear polishing polymer antifouling featuring patent-ed Lubyon technology that is designed to deliver pre-dictable long term performance for in-service periods up to 90 months, International reports, and Intersleek 1100SR, is a biocide free fouling control coating featur- ing slime release technology that combats micro foul-ing on ships hulls, maintaining performance throughout the docking cycle Lubyon polymer technology (found in Intercept 8000) aims to give the coating a ?superhydrophilic? surface. International explains, when the coating is immersed, the seawater has a lubricating effect, resulting in less friction, thus reducing drag and increasing vessel efÞ -ciency to give average fuel consumption and associated emissions savings of 5% annually compared to typical controlled depletion polymer antifoulings. Intersleek 1100SR, reported to be the shipping indus- try?s Þ rst biocide free, ß uoropolymer technology that tackles the ?slime challenge.? According to a recent formula produced by Michael P. Schultz, Professor, Department of Naval Architecture & Ocean Engineer- ing, US Naval Academy, at today?s bunker prices, the effects of slime potentially costs the shipping industry 44 million extra tons of bunker fuel, $28.6 billion in additional fuel costs and an extra 134 million tons of CO2 emissions every year. Designed for all commer- cial vessels, even when slow or ultra slow steaming, Intersleek1100SR slime release technology is designed to deliver macro and micro fouling control with static resistance even in warm waters. Sigma Ecoß eet 690 is designed to provide high per- formance antifouling for short sea and coastal shipping, the newest addition to the Sigma Ecoß eet range which provides predictable antifouling protection at variable operating speeds in aggressive fouling environments. Developed speciÞ cally for the dry dock, maintenance and repair market, Sigma Ecoß eet 690 has been for- mulated using PPG?s unique patented binder technol- ogy ensuring consistent performance levels and fouling control for in-service periods of up to 60 months. Fully compliant with the IMO AFS Convention, the product is suitable for a wide range of vessel types and contains an ultra-high volume solids content of 70% - thus reducing potential VOC emissions. Sigma Eco ß eet 690 has been formulated to be easy to apply, increasing productivity and reducing overall maintenance costs.Funded by the U.S. OfÞ ce of Naval Research and the Materials Research Science and Engineering Cen-ter, Duke University engineers have produced a hull coating that dislodges bacteria with the application of an electrical current, thus avoiding the use of bacteria-killing paints which can contain heavy metals or other toxic chemicals that might harm Þ sh or other sea life. The material works by physically moving at the micro-scopic level, knocking away bacteria. ?We have devel- oped a material that ?wrinkles,? or changes its surface in response to a stimulus, such as stretching or pressure or electricity,? said Duke engineer Xuanhe Zhao, assistant professor in Duke?s Pratt School of Engineering. ?This deformation can effectively detach bio Þ lms and other organisms that have accumulated on the surface.? Micanti, a Holland-based maritime technology com-pany, introduced an environmentally friendly antifoul- ing option called Thorn-D. A nontoxic adhesive foil used in place of environmentally contaminating chemi-cal coatings, Thorn-D has a textured surface that pre- vents marine growth from attaching to the hull. ?The basic thought behind Thorn-D is that a combination of prickliness and swaying of Thorn-D Þ bers makes the surface unattractive for organisms,? said Micanti founder, Dr. Rick Breur, in a recent press release. ?The technology provides a physical barrier in the shape of Marine Coatings & Corrosion Control Keeping hulls and equipment ship shape, coatings play critical role in vessel efÞ ciency, economy MR #3 (42-49).indd 46MR #3 (42-49).indd 463/4/2013 10:56:27 AM3/4/2013 10:56:27 AM