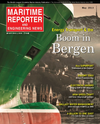
Page 48: of Maritime Reporter Magazine (May 2013)
Energy Production & Transportation
Read this page in Pdf, Flash or Html5 edition of May 2013 Maritime Reporter Magazine
48 Maritime Reporter & Engineering News ? MAY 2013 SOFTWAREA century ago this year, the Þ rst ocean-going diesel ship in the world, the M/S Selandia, embarked on her maiden voyage. She was a technological won-der, and both her hull and engines were built by Burmeister & Wain (B&W) of Copenhagen, Denmark.B&W is now a part of MAN Diesel & Turbo ? a company with 12,000 em- ployees worldwide ? and the marine low-speed business unit is located in Copenhagen. The unit has capitalized on B&W?s historic expertise to pro- duce new engines that can weigh up to 2,800 metric tons and tower 16 meters high. Once such behemoth engines are installed, they have to be serviced in place?and they must require servicing as infrequently as possible. Reliability and durability, over a long and demanding life, are crucial to marine engines. They are built to perform over 30 years, roughly 6,000 hours a year, at a constant speed of about 100 rpm?a billion revolution cycles on full design load. Under these grueling conditions, fuel combustion and inertia of moving components can potentially cause high-cycle fatigue failure. ?It?s vital that ev- ery part of our engines is designed and analyzed with sufÞ cient safety margins against fatigue loads?right down to the welds,? says Tore Lucht, industrial re- searcher at the R&D department of the marine low business unit in Copenhagen.Simulation of cracks: A strong tool to design against weld fatigueThe criticality of paying full attention to every single weld detail in the huge complex engine structure became a fo-cus for R&D when a butt weld on a low speed marine diesel engine developed a crack. The weld was on the face of a sec- ond order compensator, a large rotating component that dampens engine vibra-tion for greater crew comfort. While the compensator was designed to withstand large loads and stresses, the engine had only been in service two years, logging 13,000 hours and approximately 78 mil-lion revolutions of the crankshaft when the crack was observed. The R&D department conducted a pre-liminary investigation using Abaqus Þ -nite element analysis (FEA) from SIMU-LIA, the Dassault Systèmes application for realistic simulation. ?We switched to Abaqus several years ago because we found it was the best tool for simulating engine structures,? says Lucht. ?We use it for all structural calculations of our low-speed engines.? In the initial inves-tigation they modeled a small cut-out from the engine undergoing centrifugal force from the ß yweights (see picture above). The centrifugal force was that of a MAN B&W 5S60MC-C diesel engine at 100% rpm?a 16-metric-ton load. The engineers were able to simulate all these loads accurately based on decades of Þ eld data from operating engines. ?Our engine analyses are highly realistic,? Lucht says, ?because we put so much effort into benchmarking against litera- ture, measurements, and service.?The initial simulation showed that small areas of the weld root had stress levels above a reasonable design limit. A different weld design might signi Þ cantly reduce stress amplitude and solve the problem, but how could the engineers make sure that the improvement was sufÞ cient? ?Clearly more investigation would be required to determine a repair procedure and a suitable weld for future engines,? Lucht says.The International Institute of Welding (IIW) recommends three different meth- ods to analyze welds: hot spot stress, effective notch stress, and fracture me- chanics. The Þ rst method evaluates the weld by comparing structural stress at the hot spot to the FAT (fatigue) class of different weld details. Effective notch stress analysis can assess both toe and root stress level, again comparing each to a special FAT class. Fracture mechan- ics can be used to simulate typical weld defects on any part of the weld, using lin-ear elastic fracture mechanics (LEFM).Based on previous research projects and experience, the analysts at the R&D department decided that LEFM would give them the most accurate answers, even though it potentially involved a great deal of model preparation. ?The applied meshing of the crack can be very time-consuming because a special mesh is required along the crack front,? says Lucht. However, the team employed Abaqus? eXtended Finite Element Meth- Realistic Engine Simulation Abaqus FEA and XFEM for a Weld Redesign Against Fatigue Cracks Step-by-step simulation in Abaqus of the welding process, adding weld Þ ller under incremental passes of heat.A diesel engine on the MS Selandia, built by B&W in 1911-12 and launched in 1912. MR #5 (42-49).indd 48MR #5 (42-49).indd 485/2/2013 9:58:22 AM5/2/2013 9:58:22 AM