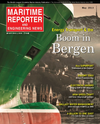
Page 49: of Maritime Reporter Magazine (May 2013)
Energy Production & Transportation
Read this page in Pdf, Flash or Html5 edition of May 2013 Maritime Reporter Magazine
www.marinelink.com 49od (XFEM) technology, which reduces modeling time while offering an enriched environment for exploring fracture failure, even when the crack doesn?t follow el- ement boundaries. Lucht adds, ?Since we already had advanced numerical models of our engines in Abaqus, that cut simulation time even further.? The engineers submodeled the area of the crack in XFEM with a Þ ne mesh. ?Investigating a crack of a few millimeters growing in a four-story engine undoubtedly requires some mesh reÞ nement in the pertinent area,? Lucht says. ?This submodeling strategy made our task easier and less time-consuming.?Opting to model the most severe dynamic loading on the crack, the engineers excluded contact in the crack deÞ nition, leaving a weld gap?which could occur in such a structure due to either residual stresses from welding or from a slight misalignment between the parts that the weld joins.After calculating the stresses on the original design, the engineers performed similar analyses on proposed welds for the engine repair and for weld designs on new engines going forward. One Þ nal load check was need- ed to conÞ rm that the repair was suf Þ ciently strong: the residual stress state caused by the welding process itself. This stress was not included in the other LFEM calculations, and it could potentially alter the strength of the Þ nal weld. To determine the residual stress state of the weld, the R&D department used a weld simula-tion tool for Abaqus developed in a previous research project with the Technical University of Denmark: a specialized modeling principle for simulation of a mov-ing heat source by weld Þ ller, body ß ux and surface ß ux. The simulation adds the weld Þ ller incrementally, with the elements representing the weld Þ ller assigned a temperature above its melting point. The elements were activated in groups with the mod-el change command and with predeÞ ned values of tem- perature, body ß ux, and surface ß ux. New groups were automatically activated in subsequent steps as the old groups cooled as a function of the heat transfer. ?Real- istic simulation of the moving heat source of the weld is a key to this type of simulation,? Lucht says. ?By ad-justing the active parameters like weld sequence, heat, and ß ux, it has been possible to obtain a high level of validation by comparison to experiments using meth-ods like neutron diffraction measurements.? In this case, the simulation helped the engineers see the result of welding an additional supporting structure onto an engine. This predicted both the deformation of the existing engine structure and the size of the re-sidual stress Þ eld around the crack front. The analysis assumed that Þ ller material was welded in only three strings, and the welding was simulated along the side of the model, where it would introduce residual stresses perpendicular to the only critical weld defect that could cause an opening or closing of the crack. These Þ nal simulation results enabled the engineers to relate both the residual welding stress Þ elds and the crack simulation to obtain realistic fatigue assessments. As expected, large tensile residual stresses remained at the toes of the weld, but the stress level was close to zero at the weld?s root. This meant that the stress intensity factor evaluation of the critical root of new weld designs would only be marginally in ß uenced by the residual stresses of welding. ?Even so,? Lucht points out, ?It would be good prac-tice to take precautions, such as adding a peening step to the weld toes, to limit the inß uence of high tensile stresses on the safety margin against fatigue failure, so that we don?t introduce a new problem with the repair.? Analysis Results: Clear Sailing Ahead Realistic simulation revealed why the original weld design performed as it did and conÞ rmed that the new design would be safely within the recommended limit curve. The demonstrated lack of tensile stress in the weld root proved out the integrity of the new design. ?This combined method of weld process simulation and fracture mechanical evaluation of weld defects with XFEM is a strong tool to evaluate the structural integrity of complex welded structures,? says Lucht. ?From this analysis, we were able to verify that our new weld design is safe, both for repair of existing engines and for use in future engines.? MR #5 (42-49).indd 49MR #5 (42-49).indd 495/2/2013 9:58:37 AM5/2/2013 9:58:37 AM