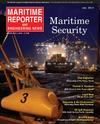
Page 39: of Maritime Reporter Magazine (July 2013)
Maritime Security Edition
Read this page in Pdf, Flash or Html5 edition of July 2013 Maritime Reporter Magazine
www.marinelink.com 39Recent DP Failures on MODUs In two recent incidents, dynamically positioned drillships lost func-tional thrusters due to an electrical disturbance when attempting to reconnect a faulty thruster after maintenance. When the thruster was reconnected it was not electrically isolated from other thrusters and the thrusters did not ?ride through? the disturbance causing loss of thrust. During these incidents the drillship crews were unable to restore all functional thrusters and as a consequence these drillships lost position and had to initiate the emergency disconnect sequence (EDS). In another incident a dynamically positioned drillship encountered severe weather with high, shifting winds that caused it to lose posi-tion and initiate the EDS. Despite receiving a weather alert for severe thunderstorms and high winds well before this incident, only half of the available diesel generators were on line when the storm hit and the DP Operator (DPO) ordered a signi Þ cant heading change with a high rate of turn when the drillship began to lose position. The drillship was unable to achieve the ordered heading or bring all generators online before it lost position and had to initiate the EDS. Based on these in-cidents, the U.S. Coast Guard recommends that owners and operators of dynamically positioned MODUs operating on the U.S. Outer Con-tinental Shelf:? Include appropriate material on preventing these incidents in training programs for DPOs and other key DP personnel. Train- ing programs should maximize use of DP simulators to gain proÞ -ciency in maintaining heading (dynamically positioned drillships) and ensuring equipment is ready ahead of severe weather, ensuring com- munications with the drill ß oor (e.g. use of ?blue advisory?/risk assess- ment) and re-establishing thrust in emergency situations. (See Marine Technology Society (MTS) MODU Operations Guidance Section 4.13 and IMCA M 117 Rev.1 Appendix 4). ? Develop and implement a Critical Activity Mode of Opera- tion (CAMO) and a Well Speci Þ c Operating Guideline per MTS, ?DP Operations Guidance? to ensure that the most reliable DP system conÞ guration is used during critical activities. Develop and utilize a CAMO for any activity you or your lessee identiÞ es as critical. When developing a CAMO, consider requiring open bus operation during critical activities to prevent a worst case failure with a potential for zero thrust in excess of your drift off time to the Point of Disconnect (See MTS DP MODU Operations Guidance Section 4.8 and Appendix C ?Example of a CAMO?, ?Power Distribution?). ? It may be possible to make a common power system fully fault tolerant in respect of single failure criteria for DP Class 2 and DP Class 3. However, in such designs fault tolerance depends on a very comprehensive range of protective functions and on many items of equipment being able to perform to capacity. Operating the power plant as two or more independent power systems reduces dependence on protective functions and vulnerability to hidden failures. It does not remove all common points between redundant systems. The potential to lose one part of the system is higher but the potential to lose the complete system is reduced (See MTS ?DP Vessel Design Philosophy Guidelines? Section 10.8).? Perform testing aboard MODUs to ensure functional thrust- er drives will ride-through a system disturbance. This testing should indicate how the system will react during a signiÞ cant bus disturbance such as a short circuit on the main switchboard. Where ride-through capability is an essential part of the DP redundancy concept it should be proven by live short circuit and ground fault testing per Section 9.2.5 of the MTS ?DP Vessel Design Philosophy Guidelines.? This testing should be incorporated into the vessel DP Proving Trial ( Þ ve-year).? Perform regular thermal imaging surveys of DP system elec- trical equipment (e.g., switchgear, drives, motor controllers, etc.) as part of a preventative maintenance program to provide early detection of faulty or loose connections.www.marineinvestigations.us Design study developed by NLI Solutions, Rolls-Royce & Wilhelmsen Technical Solutions Offshore oil and gas engineering specialist NLI Solutions (NLI) has developed a concept for a LNG Bunker Barge based on the NLI LNG tank design. The concept has been further developed in a design study together with the Marine division of Rolls-Royce and Wilhelm- sen Technical Solutions (WTS). LNG Bunker Barges are often described as the ?missing link? in the LNG supply chain. Today, only one example exists, capable of carrying 187 cu. m. of LNG, even though ocean- going ships need to bunker several thousand cbm. The HighTechBarge is designed to answer multiple demands for a cost-effective, high-tech high-volume barge. For safe operations and increased maneuverability, the HTB will be equipped with pod- ded propulsion similar to those used in offshore support vessels as well as state-of-the-art electronics for early threat detection. The NLI LNG tank is an atmospheric, prismatic steel tank, type ?B?, with a capacity of 4,000 cu. m. of LNG. It will be Þ tted with a new insulation system with very low levels of boil off gas. Onboard power and propulsion are fed by an environmentally-friendly gas engine. The HTB has a large pressure tank on the aft deck for boil off gas handling and gas delivery to engine. Planning for the study has been carried out between:- NVC ? Responsible for design, Bergen gas engine, pod drives and bridge systems; - TI Marine Contracting (part of WTS) ? responsible for insulation systems; - NLI ? responsible for tank, LNG/gas systems, bunkering systems; - DNV ? evaluation of the barge concept with respect to limitations and possibilities within the existing codes and regulations.For further product and company information please visit: www.lngtank.no www.nli.nowww.wilhelmsen.com/technicalsolutions NLI:NLI: Concept for Large Concept for Large Volume LNG Bunker Barge Volume LNG Bunker Barge MR #7 (34-42).indd 39MR #7 (34-42).indd 397/1/2013 9:35:57 AM7/1/2013 9:35:57 AM