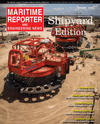
Page 75: of Maritime Reporter Magazine (August 2013)
Shipyard Edition
Read this page in Pdf, Flash or Html5 edition of August 2013 Maritime Reporter Magazine
manufacturing controls are worked out, rigorous internal prequaliÞ cation testing is carried out in preparation for regulato-ry Type Approval testing requirements. Victaulic replicates known scenarios that could be encountered, applying pro-cess technology and even re-engineering products as necessary. External assessmentOnce the product passes internal test-ing, Victaulic initiates the external as- sessment process by sending a compre-hensive data ?package? to each agency that will issue its own unique Type Ap- proval CertiÞ cation. The information includes application forms, detailed product speciÞ cations, manufacturing drawings and any performance data already validated by one of the IACS members within the past Þ ve years. The speciÞ c approval objectives along with a test proposal outline is also provided for the agencies? technical review. The com- ponents of this package must be accurate and complete, and can take weeks and often several months to compile.Mechanical bolted couplings are gen-erally understood by the agencies to have pressure holding capabilities that meet or exceed the performance ratings of ß anged, welded or threaded systems. This makes the review process a bit easi-er, yet each system application being ap- plied for will be examined individually, along with any limitations or restric-tions imposed by the IACS standards. The agency engineering review process is typically completed within a four- to six-month period for any given product category. Following the design review and ac-ceptance of the proposed test plan, the agency will advise the scope of testing required and the number of test samples that will need to be prepared. At this point, the difÞ cult and time-consuming task begins to coordinate all of the re-quired testing with a number of indepen-dent laboratories which are accredited by one or more of the participating IACS members. To facilitate performance testing, prod- uct samples, pipe of various speciÞ ca-tions and other related equipment must be sent to the appropriate test facilities. This is another time-critical operation ? as any delays on the part of a manufac-turer could result in a lost position in the testing laboratory?s queue. At this stage, documentation must already be available in multiple languages for examiners to assemble equipment themselves, based on an assumed level of skill equal to that of the end user. The testing process can take many months and occasionally more than a year to complete.The approval authorities are also con-cerned with the manufacturing and as-sembly locations of speciÞ c Þ nished parts or sub-assemblies. Victaulic manu- factures in multiple locations globally to optimize supply chain logistics. How-ever, this can greatly increase costs, as each location must be certiÞ ed and au- dited, both for the initial Type Approval certiÞ cation as well as part of an ongo- ing surveillance program required to maintain valid certiÞ cation. In the event of a nonconformance at this late stage a manufacturer risks losing valuable time to market. Manufacturers like Victaulic can only go to market when they have secured all necessary Type Approval and manu- facturing certiÞ cations. Once complete, only then can results be reviewed and data fed back to the research and devel-opment teams. Audit management Audit management is the Þ nal phase in the regulatory cycle. This phase starts when a Type Approval is of Þ cially re- leased and only ends when the product is no longer produced. Through various follow-up procedures and factory pro-duction control audits, manufacturing procedures are reevaluated annually on a set schedule that coincides with the term of validity for each Type Approval cer- tiÞ cate. Auditing is important, since the gov-erning IACS standards are updated on a periodic schedule. These standards are likely to become ever more stringent fol-lowing the analysis of forensic evidence from equipment failures, accidents and other events at sea. Manufacturers may have little advance notice of pending re-visions to these standards and often need to act quickly to keep pace and maintain a competitive position in the market. Therefore clear understanding of the most up-to-date requirements is vital to the successful completion of the approv-al cycle and managing time to market. Responding to customer demands On occasions approval may be re-quired for a speciÞ c application which is not part of the normal Type Approval scheme. In one such example a customer wanted to use Victaulic products on hy- draulic winching equipment, which re-quired an extremely heavy load capabil-ity to lift chains and anchors up from the ocean bed at a depth of 200m. In a case like this, a manufacturer must refer to the approving authority to iden-tify speciÞ c tests that would be needed to gain special approval ? either as an addi-tion to the existing certiÞ cate or through a separate approval. The administration, time and cost implications of such pro-grams are evident.Sharing responsibility Victaulic views its role in the regula- tory process as going beyond simply re-specting the rules. Having direct involve-ment in developing and shaping them is equally important. With over 85 years experience in the mechanical joining of piping systems and related components in a wide range of materials including steel and stainless steel, aluminum, duc-tile iron, PVC and HDPE, Victaulic is a world leader with a strong message that is being heard globally on many codes and standards committees. Additionally, the company has a department dedicated to regulatory compliance, with oversight responsibility for product speciÞ cations, testing and certiÞ cation, factory produc-tion control auditing, codes and stan-dards development and customer related input to these processes. Victaulic invests heavily to achieve product and service excellence and sees regulation as an area of responsibility where it can contribute to the construc-tion of safe, efÞ cient and durable mari- time piping systems. The company?s philosophy is to create a set of meaning-ful tests that are rigorous enough to rep-licate known Þ eld conditions, yet realis-tic enough for manufacturers to conduct in a reasonable timescale without undue complexity and cost. Ultimately, product conformity brings peace of mind to ship builders, operators and owners. The safety and reliability of vessels at sea depends on it. The mechanical pipe-joining system begins by cold forming (roll grooving) or machining a groove (cut grooving) into the pipe end. The piping con- nection is secured by the ductile iron coupling which houses a resilient, pressure-responsive elastomer gasket. The coupling housing fully encloses the gasket, reinforcing the seal and se- curing it in position as the coupling engages into the pipe grooves. The mechanical joint creates a triple sealing characteristic that utilizes compres- sive forces from the initial gasket installation and coupling assembly, which is further enhanced when the internal system pressure is applied. This feature enables the assembled joint to accommo- date a wide range of pressure applications from full vacuum to the coupling?s maximum positive pressure rating. Grooved technology is used for class 2 and 3 piping systems and for class 1 systems outside category A areas. Typical applications include bal- last, sea and fresh water cooling, lube oil, re and deck wash, and bilge systems. The technology is also used for class 1 and 2 FiFi systems on tugs and support vessels. Victaulic mechanical couplings are currently categorized as ?Slip-on Joints? within the various classi cation societies? rules. Although the cou- plings are quick and easy to secure with just two nuts and bolts and a single wrench, they should not be overlooked as a reliable pressure- and end load-restraining device. The couplings themselves are cast of durable ductile iron in accordance with ASTM A-536, and are more than capable of han- dling the full thrust loads generated during pump operation and maximum system pressures to 34 bar. The fact that systems utilizing these products do not require external restraint in itself de es the term ?slip-on?. Whilst the standards catego- rization may not seem properly aligned with the product performance capability, maritime users of bolted mechanical couplings are fully aware of the strength, durability and long-term serviceabil- ity they afford to the designer, owner and ship operator. www.marinelink.com 75Manufacturing locales are subject to audits to ensure quality and consistency. Grooved mechanical joints explainedMR #8 (74-82).indd 75MR #8 (74-82).indd 758/2/2013 9:15:37 AM8/2/2013 9:15:37 AM