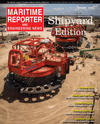
Page 76: of Maritime Reporter Magazine (August 2013)
Shipyard Edition
Read this page in Pdf, Flash or Html5 edition of August 2013 Maritime Reporter Magazine
76 Maritime Reporter & Engineering News ? AUGUST 2013 PRODUCTSTOOLS For consumable parts a typi-cal shielded plasma torch has an electrode, a nozzle and a shield. Many other torches are unshielded with an exposed nozzle and an electrode. The two consumable parts in any plasma torch that wear most rapidly are the electrode and the nozzle. The elec- trode is the negative side of the plasma arc; the material being cut is the posi-tive side. The torch nozzle is at positive potential at the beginning of each cut in order to get the pilot arc started (an arc between the electrode and the nozzle that is forced through the nozzle ori-Þ ce by air pressure), then, if the torch is within striking distance of the plate the arc transfers from the nozzle to the plate, and at this point the nozzle is electrically ?ß oating,? and the function of the nozzle is to constrict and create the cylindrical shape for the arc, as well as to increase the velocity of the arc.The plasma arc in an air plasma torch has a temperature in excess of 25,000 degrees Fahrenheit. The nozzle, made of copper for excellent heat transfer (which melts at less than 1100 degrees Fahren- heit) uses some advanced technology that internally swirls the air ß ow, which slings cooler molecules to the surface of the nozzle bore, which insulates the nozzle from the high temperature arc, al-lowing the nozzle to remain solid. The electrode has an insert made of Hafnium (an earth element), a great emitter of electrons and holds up well in an oxygen rich environment (air is 20% oxygen) so it becomes the arc attachment point.Under the high temperature conditions inside a plasma torch, the electrode haf-nium emitter eventually evaporates, ul-timately the cut quality will change and the torch will start misÞ ring. The nozzle bore also erodes, changing the shape and energy density of the arc, also affect- ing cut quality. Shielded torches have a shield that electrically isolates the nozzle from touching the plate and more ad-vanced shield designs dramatically im-prove nozzle life and cut quality through increasing the energy density of the arc and super cooling of the nozzle exit bore.When the nozzle oriÞ ce becomes erod- ed and out of round, cut speeds will slow down and cut edge angularity will suf-fer. You will get more dross, and eventu- ally the torch will not cut at all. When the electrode hafnium wears to a certain depth (differently affected on different torch designs) it will also affect cut qual- ity and will eventually stop working.With a hand torch, often you can run consumables until near failure as your hand can tip and change speeds to ac-commodate the changes in cut quality associated with consumable wear. On a mechanized torch, consumables often get changed sooner as cut quality is often more closely monitored on cnc cutting applications.Better quality torches that are well en-gineered will produce better cut quality as well as dramatically longer consum-able parts life, making for a more pre-cise cutting process with a much lower cost of operation. The best engineered plasma torches today can easily achieve between 500-1500 starts on a single set of consumable parts, with hundreds of feet of metal cutting achieved. How does air get contaminated? Unfortunately, the life and perfor- mance of an air plasma torches consum-able parts can be affected by a few dif-ferent factors such as air inlet pressure, air purity, amperage, cutting techniques as well as surface condition of the plate being cut (in some cases). In this article we will discuss the effect on consum- able parts life and cut quality that can be caused by contaminants in the com-pressed air supply. By looking back at the description above of the temperatures and the bal-ancing act of gas ß ow physics that occur inside the plasma torch, I still wonder (after 35 years in this business) how the consumables last for more than a few seconds of cutting. In reality, a plasma torch is a true design marvel that allows us to use an ordinary, safe, non ß amma-ble gas mixture (air is roughly 20% oxy-gen and 80% nitrogen) combined with a DC electrical power source to produce a high temperature arc that will melt vir- tually any metal in its path. Internal air swirl patterns are created, starting pilot arc current is accurately produced, con-trolled and timed, and ramp up and ramp down amperage in today?s systems are microprocessor controlled to ensure that the torch and consumables are adequate-ly cooled while maintaining a high level of energy density to get the cutting job done.A typical compressed air system in- volves a motor driven compressor and an air storage tank (known as a receiver). There also is an air delivery system that consists of pipe or hose that is designed to adequately deliver compressed air at the correct ß ow rate and pressure to the plasma cutting system. The pressure and ß ow rate will vary depending on manu- facturer and model of the plasma system, so the compressor and plumbing system must be sized properly to deal with the plasma system being used.The compressor simply takes the same air we are breathing and runs it through a pump (usually a piston type compres-sor pump) that delivers the air to the re-ceiver and increases its pressure. In most cases the compressor increases the air pressure from atmospheric pressure to somewhere in the range of 90-135 psi. By increasing the pressure of air, a much higher volume (as measured in cubic feet) can be stored in the receiver, which makes the system more efÞ cient.Unfortunately, many locations on this planet have relatively high levels of moisture or humidity in the air, and when compressing the air into the re-ceiver, the same volume of moisture per cubic foot of air is also stored with the air. The compressor pump creates some heat in the stored air so the air going into the receiver is rather hot as well. High humidity levels and warm air are then stored in the compressors receiver tank. As this warm air travels through the plumbing system on the way to the plas-ma cutter, the air cools inside the pipes and hoses, when air cools the relative humidity starts to react by condensing, and at this point we have air at 90-135 psi, with aerosol droplets of moisture. When the air reaches the plasma torch there is a pressure drop as the air reenters atmospheric pressure, and further rapid cooling and condensing of the moisture occur, which allows some air and a rela- tively high level of water to be present inside the plasma torch. On a hot humid day with a compressed air system with no moisture traps or protection, it is not uncommon to see a mist of water spray-ing out of a plasma torch head while in the test air ß ow mode (no plasma arc, just air ß ow). When this occurs, all bets are off in regards to plasma torch cut quality and consumable parts life.How does the water affect the torch consumables?As mentioned earlier, the plasma cut- ting process is a carefully controlled balancing act of physics. An air plasma torch is carefully designed to create the correct ß ow rate and gas swirl pattern that will provide a good combination of arc velocity, energy density and consum- able life. Clean dry air is close to 20% oxygen and 80% nitrogen, and the con-sumable parts are engineered and preci-sion manufactured to work best with this gas combination. When moisture is add- ed in the plasma torch inner plenum, the gas chemistry changes. Water is com- prised of oxygen and hydrogen mole-cules and as soon as it is subjected to the high temperatures inside the torch it rap-idly returns to the oxygen and hydrogen state, which mixes with the air mixture in the torch. The hydrogen and increased oxygen content alter the balance of phys-ics as well as cooling effects in the torch. The electrode?s hafnium emitter starts to erode very rapidly in turn damaging the nozzle bore and oriÞ ce shape dramati- cally changing cut quality and wearing the consumable parts at a rapid pace.Often, there can be other contaminants in compressed air as well. A worn com- The Importance of Clean Dry Compressed Air for an Air Plasma Cutting SystemBy Jim Colt, Applications Technology Manager at Hypertherm MR #8 (74-82).indd 76MR #8 (74-82).indd 768/2/2013 9:16:05 AM8/2/2013 9:16:05 AM