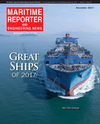
Navigating the New Norm
By Christopher J. Wiernicki
How technology, skills and expectations are shaping our maritime future
It is not business as usual in the world where we do business. Things are changing. And the speed and scale of these changes will be unprecedented and disruptive:
- Changing business landscapes and energy profiles;
- Changing market expectations and needs;
- Changing technology;
- Changing societal expectations toward policies and regulations that minimize environmental impacts and maximize safety;
Even regulations themselves are changing from less prescriptive in nature to more performance-based.
As Chairman, President and CEO of a global classification and technology-centric company that operates in 70 countries with 5,000 employees, I am continually assessing the impact of these changes on the capabilities ABS needs to fulfill its mission and maintain its leadership position in the maritime, offshore and government industries it serves.
To know where we are heading, we have to know where we began. There are four key megatrends that are shaping the future of the maritime industry.
1. The world economy and population are continuing to grow. Every year the world’s population expands, from 7.6 billion people today to just short of 10 billion by 2050. This population growth will provide more labor resources, develop new technologies and increase trade.
2. There are societal and regulatory pressures for the industry to operate cleaner and be more transparent: Ballast water management, the sulphur 2020 cap and EU-monitoring, reporting and verification requirements are taking hold.
3. The center of our global gravity is shifting to the east. China was the world’s largest economy in 1820. It’s the second largest today and on track to return to be the world’s largest once again in 2030.
4. Technology is quickly propelling us into the heart of the fourth industrial revolution.
The next five years will bring turbulence and change, shaking out our industry and setting the course for the next 20 years and beyond. Market cycles will continue to evolve and will be impacted differently than they are today.
For example, in the past, market cycles have been impacted by globalization and emerging economies, such as China. In the future, market cycles will be impacted by technology and regulations. This means that governments and organizations like the IMO will become even greater global industry-shapers, as they provide the frameworks that will need to be synchronized with emerging technologies.
Some may be frightened by this concept, but I see it as exciting and full of opportunity. Today, our business environment is changing and we have a new definition of what ‘normal’ means. The new normal means nothing is normal. Normal means change: rapid change, disruptive change and impactful change.
There are four big challenges facing the shipping industry:
- Digitization and connectivity
- Cyber security
- Emissions reduction
- Efficiency improvements in operational performance
The three biggest challenges facing the offshore industry are:
- Improving productivity and increasing standardization
- Building confidence in a stable oil price environment
- And digitization and connectivity.
The New Direction
The new norm we face today – and for the forseeable future – compels our industry to:
- Improve our productivity, efficiency and optimization
- Embrace digitalization and connectivity through greater integration of information technology and operational technology (IT/OT)
- Recognize the need for a shift in our approach to talent
- Leverage data so it becomes a competitive advantage and includes smart people, smart ships, smart fleets and smart business
- Build convergent mindsets that value not only technical viability, but includes economic feasibility and social sustainability
We know technology is going to shape our future. From that perspective, the fourth industrial revolution builds from the first, which started in the 1780s with steam and water power to mechanize production.
A century later, assembly lines and electricity moved us into the second revolution for mass production. The start of the third revolution, in 1969, brought electronics, IT and automated production. And now, just half a century later, we’re well on our way into the fourth revolution, which is the fusion of technologies in the cyber world that are blurring the lines between physical, digital and biological spheres.
Today is distinctively different from the third revolution due to:
- Velocity, the speed of current technology breakthroughs;
- Scope, disruptive technologies are affecting nearly every industry in every country, and;
- Systems impact, because the monumental transformations of how we work and manage are changing fundamentally.
We are moving from a vertical world to a horizontal world. In fact, you could argue that the first three industrial revolutions were somewhat singular and vertical. The fourth revolution, which is data and digital technology driven, is more horizontal in that today, we have unprecedented processing power and unlimited access to knowledge. These trends transcend industry.
Digitization and connectivity is transforming our industry through the use of great connectivity, sensors, data and autonomy. Performance improvements and marine regulatory compliance will be driven primarily by digital-related technologies, and secondarily by traditional technologies. The new norm is data-intensive.
Disruptive technologies are impacting all of our daily lives. Look at what Uber and Air BnB have been able to accomplish, impacting legacy industries such as public transport and accommodation. So it is naïve for the maritime industry to think it is immune from such disruption, or a new definition of normal. The marine and offshore industries are seeing the early effects now of managing and leveraging data, but the full impact is still years away, with major changes on the horizon.
There will be obvious benefits to autonomy: lower operational costs; better operational efficiency; less human error; fewer carbon-based emissions; and increased safety. But it is important to understand the subtle differences between autonomy and autonomous. Autonomy is defined as the quality of self-governance and freedom from external control or influence; it is also used often with the word independence.
Autonomous, on the other hand, can take different meanings when speaking of vehicles and ships. An autonomous vehicle is a motor vehicle that uses artificial intelligence, sensors and the coordinates from a global positioning system to drive itself without the active intervention of a human operator.
An autonomous ship is a marine vessel with sensors, automated navigation, propulsion and auxiliary systems, with the decision logic necessary to follow mission plans, sense the environment, adjust mission execution according to the environment and potentially operate without human intervention.
The concept of the autonomous ship is accelerating globally, primarily driven by governments.
Vendors and shipyards also are accelerating the activity in this space alongside governments, with activities primarily contained locally, within countries, rather than expansive international projects at this time.
Autonomy Challenges
None of this development is without challenges. The journey from automated to autonomous is complicated, but logical. As vessels adapt to more sensors, health and performance monitoring and performance optimization, they will become smart assets.
In addition to increased monitoring and optimization, factors such as data integrity, software integrity and cyber security are now factoring into the equation to allow vessels to become semi-autonomous. Once machine learning and automated decision-making take hold, only then can a vessel achieve autonomy. Of course, each of these progressions must come with rigorous verification and validation for every step.
Verification involves asking: ‘are we doing the thing right’? Validation is asking ‘are we are doing the right thing’? Both questions are critical throughout the logistical progression to smart and autonomous. Finally, the societal need for safety must be addressed in a digital progression to semi-autonomous (reduced manning) or completely autonomous (unmanned). In this context, the next generation of safety system is the cyber-enabled physical system – beyond traditional safety systems such as hull and structure, mechanical and electrical.
Cyber and software are the third leg of the safety stool, adding a new dimension to a vessel’s safety system. Maritime safety – in shipping and in offshore – will depend increasingly on cyber-enabled physical systems and integrated IT/OT efforts. Safety-related regulations and standards must recognize this and address this because software is the safety system nobody sees.
The Human Factor
In addition to developing and adopting new technologies and regulatory frameworks, the maritime industry also must take a hard look at what type of people will be required to work effectively in this ‘new norm’, and also – and perhaps more importantly – what academia needs to do to prepare this new talent and what organizations need to do to retain it. New mindsets, skill sets and leadership will be required. This is what I call the absolute value of talent.
As I lead a global digital company operating at the frontier edge of technology, the biggest and most important asset on our balance sheet is people. People are the engine that drives my company and talent is the energy source or fuel that makes it happen.
Analog talent is different from digital talent. With digital technology transforming us almost daily and companies planning and executing growth strategies, talent needs to be looked at in the context of seven questions:
- What talent is needed in a technology-driven world?
- How does it look different from the past, and why?
- How do we get there?
- Does sustainable growth require a talent rethink?
- How does the future talent equation drive us to look at ‘the absolute value of talent’ over different dimensions and greater magnitudes than traditional, more singular looks?
- How do we evaluate and develop this talent…not just what are we looking for in new graduates, but how do we handle a multi-generational workforce?
Historically, age + experience + skills = training has defined talent and led organizations to determine where someone was in their career, and possibly what their trajectory should be in the company. Today that talent equation is being redefined.
Now, we have technology and people coupled together, which is creating a new dimension that requires a new approach to talent development. New technology is redefining the types of skills we need. The talent will require skills such as data-driven decision making, predictive data analytics, systems and design thinking, integration engineering and cyber awareness and impact.
And the pace of technological change is redefining how we measure talent with regard to mindsets for learning and the ability to rapidly embrace change; after all, innovation is nothing more than fast learning.
Technology is moving us toward a requirement for more condition-based, continuous, real-time, risk-based and cyber-influenced decision-making. So what does this mean for the requirements of an emerging workforce?
When we take a closer look at technology in the context of new mindsets, skill sets and leadership, it is necessary to consider how we got here.
Today, our industry is at a crossroad in terms of skills development. We need to:
- Recruit and develop traditional skill sets from traditional sources to work in a more connected and complex shipboard environment.
- Supplement and compliment traditional skill sets with non-traditional skill sets from non-traditional sources
- Create an industry (and company) culture to blend both together
- Blend the need for specialists vs. generalists for strategic decision making
We must develop a workforce capable of handling the traditional areas such as structures, machinery and marine operations that tend to focus on isolated systems, with the emerging, non-traditional areas of integrated cyber networks that interconnect, monitor and control shipboard systems and equipment.
Civil and mechanical engineers and naval architects have to be blended with systems engineers, cyber engineers, risk engineers, data analysts and computer scientists. The boundaries of what we do in maritime are expanding and deepening – the lines are becoming blurred – and we’re all doing more on a larger scale with more technical sophistication.
The regulatory and policy landscape is also changing. Regulators and governments are becoming more complex, more performance-based and more data-relevant. New technologies are being developed and applied at unprecedented speeds to meet regulatory and operational demands.
Global shipping operations are becoming increasingly dependent on integrated networks supported by software and data-transfer solutions. Onboard systems are connected to shore-based systems and are redefining the traditional ship-to-shore interface and responsibilities.
Beyond the more integrated systems, owners, operators, crews, vendors, governments and classification organizations all are looking at the benefits of collecting, analyzing and harnessing the power of big data. It’s no longer optional.
Cyber is rapidly growing in importance because reliability is a safety issue. And you can’t have cyber anything without software; so keeping all the systems on every vessel safe and secure poses new threats and challenges. To address these, our industry will require talent with non-traditional skill sets that can handle a future of complex, integrated systems that are managed with data-driven thinking.
Next in the new talent equation is people. The people we look to hire today are those who can continually adapt and re-adapt to the environment. They have an ability to learn fast. We look for a different kind of skill set in these people, because we require more systems thinking, design thinking and a ‘convergent mindset’. By this, I mean the ability to take a strategic perspective, focused on risk versus risk thinking, with a strategic focus on three areas:
- technical feasibility
- economic viability
- social desirability or sustainability impacted by policy and regulations
The talent-development programs for these people must focus not just on technical disciplines, but on an integrated path to building skills in strategic operations and systems thinking. Our world is changing. But change does not happen in a linear fashion anymore; it’s fast, it’s disruptive, and people need to be prepared to think that way, and embrace it.
The fourth revolution is cutting across all technical areas, horizontally. Beyond hull design and structure, and beyond propulsion engineering on ships and offshore platforms, are emerging technologies propelling our industry on a new course. The future naval architect must understand the latest software, as well as the traditional hardware.
Understanding and managing data is more important than ever. Our people need to have the capability and insight to manage predictive data and analyze the results to make quick decisions about how we tackle engineering challenges.
It has already been five years since the world economic forum declared data to be “a new class of economic asset”, like a currency or gold. Still, when analysts talk about data, it sounds less like currency and more like sand: absurdly plentiful and barely useful unless you know what to do with it. Just as sand can be turned into glass and concrete and used to build a skyscraper, or just poured into sacks for dead weight, big data can be used to revolutionize a business or just bog it down in a senseless series of correlations.
Success or failure in the analysis of data, whether big or small, depends on the quality of the analytics and the abilities of the analyst. But as we seek the global talent we need to meet these challenges, the technical talent pool is shrinking.
With fewer candidates available from traditional talent sources, we will have to go outside and recruit talent from non-traditional sources with non-traditional degrees. And we will have to look beyond what’s required to just fit a role today.
When we couple the escalating emergence of disruptive technologies with the increasingly varied skill sets people will need to bring to the table, we are essentially creating a new talent ecosystem that is reshaping work.
This ecosystem is comprised of a multi-generational workforce, because people are working longer. The responsibility for creating that has moved from an institutional level to a global level, given the near universal demand for the new skill sets, and our common interest in its success.
We need to approach developing this talent from multiple angles, because when new types of talent are combined with traditional corporate cultures it requires innovative training and development programs, which need to deliver measurable results quickly.
The right talent strategy helps people to be productive faster and it ultimately accelerates getting new technology to the market.
The next generation of talent needs a culture of continuous learning, where training is more than just a one-time event; it’s a small piece of an overall learning experience that measurably improves performance and efficiency.
Instead of one-and-done training sessions, the new normal for learning is having on-demand content that’s coupled with richer, in-person learning and on-the-job training, with competency and retention checks at regular intervals. The on-demand information is searchable, can be accessed on mobile devices and is made available in subject-specific communities-of-practice or knowledge networks that allow people to tap into the experience of others, as well as formal coursework.
Today’s emerging workforce tends to crowd-source their information from a network of peers or experts just as much as it looks to more formal channels or training courses. In our interconnected world, training and development is expected to be as readily and rapidly accessible as a Google search.
For traditional maritime companies to thrive and attract the right talent to succeed, fresh thinking, new technologies and alternative business models will be essential. For the maritime industry, the next generation of naval architects and marine systems engineers must be like the next generation of aerospace or automotive innovators: capable of engineering, design thinking and, most importantly, they must have a convergent mindset.
It’s clear that the next generation of talent – regardless of the industry in which they work – will need to possess a convergent mindset. The emerging needs of the future require all of us to change the way we see people and how we develop the next generation of leaders.
For academia, this means educating students who can:
- anticipate, leverage and exploit rapidly emerging technologies, with a greater emphasis on integration
- make techno-economic and risk vs. risk decisions within a policy framework
- create a better balance between innovation and creativity within the technical education curriculum by focusing on non-traditional areas such as architecture and sustainable design, engineering product development, engineering systems and design (including cyber-enabled physical systems) and information systems and data analytics
Academia and businesses must be open and responsive to change to survive. This means five things:
- Bringing in non-traditional skill from non-traditional sources and blending them with our traditional skills of structures, machinery, mechanics and electrical systems to address the next generation of safety systems.
- Creating a culture that recognizes the importance of data, data monetization and rewards continuous adoption and relearning.
- Identifying talent in terms of: analytical capability; fast learning; convergent thinking; an ability to thrive in an environment of generational diversity, team dynamics and continuous adoption; an ability to manage and exploit disruptive technologies
- Recognizing our responsibility to invest in continuous in-house training and development programs that emphasize systems thinking and data-driven decision making
- Understanding and always remembering that technology lacks institutional knowledge, social skills and common sense
Autonomy
The transition to autonomy has steep challenges for all industry stakeholders, not least public stakeholders. As marine and moves along the progression from analog, to connected, to digitized, to autonomous, a regulatory framework that recognizes technical and cultural challenges is required.
Currently, IMO regulations and guidance for unmanned vessel operation are in the nascent stages. In February 2017, the maritime safety committee for autonomous surface ships was launched, and an ISO smart shipping working group was established to cover the standardization in the field of computer applications (such as big data and processing the internet of things and sensors) in shipbuilding, ship operations and marine technology.
The testing of unmanned vessels is currently limited to areas with local regulatory approval until there is global regulatory acceptance. In the U.K., the maritime autonomous systems regulatory working group is planning to draft a best practice regulatory framework for unmanned vessel operations.
From their present conditions, ships’ architecture, reliability and availability must evolve to include extra redundancies, so that recovery can occur without human intervention. Recovery may range from onboard fire fighting to switching to a backup antenna when one fails.
Essentially, the operational elements of voyages will drive the technical advances, which are already impacting ship-systems architecture and design. Some of the technical challenges that autonomous vessels will face include:
Machinery systems-related:
- designing for long-term, unmanned operations
- control systems, condition monitoring, condition-based maintenance
- for short-sea shipping: electric propulsion and battery-powered systems
Navigation and collision avoidance:
- situational awareness
- data fusion with artificial intelligence
- automated collision avoidance systems
- simulators running in parallel
- keeping a human in the loop for any emergency intervention
Data handling:
- sensors, data collection and transmission
- connectivity, satellite systems, real time analysis
- storage
- cyber security
Everyone – classification organizations, vendors, shipyards, academia and regulators – are all developing technologies, systems engineering and use cases to address these technical challenges. And beyond the technical challenges, there are cultural challenges.
In the maritime industry, it is challenging for organizations that are steeped in tradition and regimented ways of doing things to transform their mindsets from being experience-driven to becoming data-driven. Many things must evolve – values, priorities, beliefs and the overarching culture of the industry – to fully benefit from data-centric solutions.
From the ABS point of view, we’re already augmenting human resources and reducing the onboard footprint today. This allows the more routine tasks to be done onboard without humans, but retaining them for reference, supervision and/or override.
Next year, we will see crews further reduced and remote support increased. By 2030, we will see remotely operated vessels and local autonomous voyages. By 2035, humans increasingly will be replaced to accom¬modate remote-controlled vessels and unmanned coastal voyages. At this stage, a ship’s system will need to be self-sufficient without human capacity to override any action taken remotely, or by a machine.
By 2040, the continued adaptation of remote-controlled operations will see unmanned vessels take ocean-going voyages. By 2045, we will see completely autonomous ocean-going vessels and voyages. At this point, there will be completely new functions that implement processes outside any organization’s current abilities.
These milestones only can happen along these timelines if technological, industrial and regulatory accomplishments occur and mature simultaneously. Everything must come together in tandem and be synchronized. When everyone and everything works in unison, the digital journey becomes a logical progression.
Our ‘new norm’ is about change, rapid, disruptive change. In the maritime industry, this change will be driven by technology but it will also require new mindsets, new skill sets, new regulatory and classification relationships and leadership roles. In our new norm, future maritime regulations should be characterized as international-aligned and IMO-developed, not disconnected, local and regional. They should be risk-driven, technology sensitive and, in terms of availability and reliability, practical and balanced.
They should be holistic in their approach and integrated over the lifecycle of the vessel system, extending beyond design and construction to address operations and lifecycle performance.
For class to continue to be effective, it also must change with the times. The class of the future, to support the regulations of the future, must be characterized as independent, risk-based, more efficient, less intrusive, technology-driven and monitoring-based. We must be continually focused on supporting the next gener¬ation of safety, performance and management systems that extend well beyond the hardware. The class of the future needs to be recognized as even more of an active partner in the establishment and application of regulations. We are built exceptionally well for this role: an independent structure, a wealth of in-service data, experience in interpreting this data and a model that each year incorporates in-service data and trends into its standard development processes. Quite frankly, the regulations and class of the future go hand-in-hand in our new norm. Their continued alignment is one of the keys to the new normal, and will drive the winds of change in shipping and the maritime industry. The new norm will be shaped by:
- New technologies and an accelerated rate of technological change.
- New mindsets and skill sets.
- New expectations and regulations that are more risk-based and performance-based, and,
- A new people balance between data-driven and experience-driven decision making.
People will continue to play a pivotal role, regardless of machine learning or unmanned autonomous vessels … in many ways, regardless of the technology in our interconnected world, how fast it evolves and how fast we adopt it, because the new norm is ultimately about people.
Consider this … if Henry Ford had had access to big data – without human knowledge, common sense, instincts and the capability to interpret it – would he have invented a faster car? Or simply a faster horse?
This preceding was distilled from a speech that was part of the Kinney Lecture Series delivered October 10, 2017 at the World Maritime University in Malmo, Sweden
The Author
Christopher J. Wiernicki, Chairman, President and CEO, ABS
(As published in the December 2017 edition of Maritime Reporter & Engineering News)
Read Navigating the New Norm in Pdf, Flash or Html5 edition of December 2017 Maritime Reporter
Other stories from December 2017 issue
Content
- Interview: John C. Pfeifer, President - Mercury Marine page: 8
- El Faro and Perceived Deficiencies in the ACP page: 12
- Maritime Cyber Security: The Wrong Formula page: 14
- Navigating the New Norm page: 16
- Driver-less Ships: Autonomy in the Maritime Sector page: 22
- Maritime's Digital Transformation & Simulation-based Training page: 26
- Ship of the Year: MOL FSRU Challenger page: 36
- LNG: Maritime's Fuel of the Future page: 48