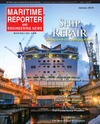
Page 21: of Maritime Reporter Magazine (January 2018)
Ship Repair & Conversion
Read this page in Pdf, Flash or Html5 edition of January 2018 Maritime Reporter Magazine
In addition to constant routine and preventative maintenance, you will always ? nd a variety of capital projects underway at the BHC maintenance facility each winter. Over the past ? ve years, BHC has reinvested almost $10m into capital ? eet retro? ts and repowers. shear diversity of vessels and equipment seen with, and implementing new regulations in an here at BHC. ef? cient, timely and cost-effective manner can prove to be a challenge for operators big and
What is the biggest challenge to running an small. Today as an industry, we are watching ef? cient and pro? table ? eet of tour boats?
with particular interest the implementation of
First, since we are located in New England, Tier 4 and what it will mean for our small pas- our excursion offerings – and the resulting ex- senger vessel industry regarding repowers, new cursion revenue – are highly seasonal. With construction and available compliant machin- excursion services making up about half of ery in the marketplace.
our overall operations, the seasonality can bring about challenges with ? uctuating cash
What technology do you consider to be the most transformational in terms of making ? ow, changing staff requirements, maintenance your operations safer and more ef? cient?
planning and more.
At BHC we are excited about technological
Second, operating and maintaining a large and vastly diverse ? eet of passenger vessels advancements and how we can use them to is a signi? cant responsibility and ? nancial manage a safer and more ef? cient ? eet. Tech- nology is at home here in every aspect of our commitment. A ? eet like ours requires a sub- business from human resources to websites, stantial capital maintenance and machinery re- placement program in order to ensure on time maintenance monitoring to insurance reporting performance, passenger safety and the highest and crew training. As our company and ? eet quality of service year after year. The BHC ? eet becomes larger and more diverse, BHC must increasingly rely on technology as a tool in requires scheduling 60 annual Coast Guard in- spections and on average 30 out of water Hull managing and monitoring our business.
Most recently we implemented Wheelhouse inspections each calendar year.
Technologies across our ? eet, a preventative
In addition to constant routine and preventa- maintenance and compliance tracking program tive maintenance, you will always ? nd a va- riety of capital projects underway at the BHC that provides alerts and reminders regarding maintenance facility each winter. Over the past vessel maintenance and compliance milestones. ? ve years, BHC has reinvested almost $10m In addition, the use of Wheelhouse allows for into capital ? eet retro? ts and repowers. This an informative data collection source that can be analyzed for future operations and plan- becomes even more impressive when you con- ning. As our ? eet has grown larger with higher sider that these projects occur in our diminish- hour and higher horsepower vessels, tools like ing off season of November to April.
Wheelhouse Technologies are increasingly im-
What regulation has had the greatest impact portant to hitting our maintenance milestones, on your business … or promises to have the managing operations, interdepartmental com- greatest impact on your business?
munications and empowering our managers,
For nearly a century, The Jones Act has regu-
Captains and crews. Without technologies like lated the U.S. domestic passenger vessel indus-
Wheelhouse, managing a 60-vessel ? eet like try. As the world has become an increasingly BHC’s which encompasses 326 pieces of major global marketplace, Jones Act compliance has machinery representing over 13 major manu- created its own set of special challenges for factures would be a monumental task.
U.S. passenger vessel operators when sourcing new construction. The increasing cost of do-
What do you consider to be the greatest “les- sons learned” about running the business mestic vessel construction has required private- from your family?
ly held passenger vessel operators like BHC to
Over 90 years our family has learned the per- think very carefully about new construction.
At BHC, for nearly two decades now, this has spective of the long haul. There will be good led us to grow our ? eet exclusively through years and bad, but the key to success for any the purchase and refurbishment of previously business is all about prioritizing and remain- owned vessels. The contracts, services and ing focused on the people you serve. Without routes available with conditions favorable for sustainable ridership and revenue, you cannot privately ? nancing new construction vessels accomplish any growth or improvements. The are few, particularly in seasonal areas like the single most important thing at BHC is to make sure our passengers are safe and happy, so our
Northeast.
In addition, the passenger vessel industry and hard-earned reputation and repeat ridership individual operators are subject to a variety of endure. Customer service has always been, regulations from multiple agencies such as the and continues to be, our top priority. And, we consistently strive to do everything we can to
U.S. Coast Guard, FTA, EPA, as well as Fed- eral and State employment laws. Keeping up ensure that each person’s experience at BHC is www.marinelink.com 21
MR #1 (18-25).indd 21 MR #1 (18-25).indd 21 1/9/2018 12:08:23 PM1/9/2018 12:08:23 PM