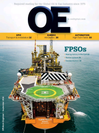
Page 23: of Offshore Engineer Magazine (Sep/Oct 2016)
Read this page in Pdf, Flash or Html5 edition of Sep/Oct 2016 Offshore Engineer Magazine
about three months. He notes that normally it takes longer. typical disconnectable buoys that are hollow steel. The buoy
Amann discussed the work scope and cited weather as a features 222 pieces of foam that need to ? t together in se- challenge. “It was winter time, and we didn’t have optimal quence. Lohr says that the use of 3D printing technology to weather conditions,” he says. InterMoor used the Seacor Keith create a model allowed Shell to ensure that there weren’t any
Cowan anchor-handling vessel (AHV) to perform ? rst phase safety issues or schedule delays.
operations, and later used a larger construction vessel on Shell produced a video earlier this year discussing how 3D charter and on standby. Amann says that the AHV was used printing came together to ensure the buoy construction went primarily to keep costs down. according to plan.
“A fundamental part of the design process is to visualize
Meeting challenges what the end product will be,” says Robert Patterson, execu-
In addition to rugged terrain and weather conditions, there tive vice president, engineering, Shell, in the video. “3D print- are other challenges to meet when working in deepwater ing allows for very rapid prototyping; allows you to engage frontier areas. with a design, installation sequence, safety risks of putting it
Lohr highlights designing umbilicals that could meet the together. If you do all of those things early, it leads to far bet- challenges associated with the extreme water depth. ter outcomes.” “It’s easy to say 9500ft of water, but more challenging to Amir Salem, construction engineering, Stones project, SBM execute,” Lohr says. “Because of the water depth, the tension Offshore, added: “Having a model like this bridges the gap and the load on the umbilicals becomes quite high, and we between design and fabrication.” actually had to work with the contractors to come up with something that works in this water depth.”
WATCH
Additionally, Lohr highlights the disconnectable tech-
See how Shell used 3D printing to further the nology used on the project. “The way we worked with our
Stones project. http://bit.ly/2bjkjCR contractors to meet the challenges of 9500ft of water is a very special thing.”
The 3D advantage
For Stones, Shell took advantage of 3D printing technology to
Curtis J. Lohr will discuss the Stones project at this year’s ensure the disconnectable buoy on the project came together
Global FPSO Forum, presented by OE, on 31 August 2016. ? awlessly during the construction process. The disconnect-
For more information, please visit: GlobalFPSO.com.
able buoy features a design that uses syntactic foam, unlike providing
INNOVATIVE
DESIGN
Looking forward to &
QUALITY
SERVICES the next 50 years years 1965-2015 © DORIS Engineering/ F. Lucazeau www.doris-engineering.com oedigital.com September 2016 | OE 25 022_OE0916_ Feature1_Audrey.indd 25 8/24/16 12:57 PM