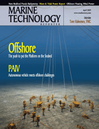
Page 31: of Marine Technology Magazine (April 2005)
Read this page in Pdf, Flash or Html5 edition of April 2005 Marine Technology Magazine
www.seadiscovery.com Marine Technology Reporter 31
Life-of-Field Concept of Operations
When deployed into a field development, there are some basic tasks that the hover-capable AUV will have to carry out during every mission and some that will be mission specific. Some typical mission elements are described below. It is important to note that, unlike the seabed survey AUV where its task is to find out what is on the seabed, the hover-capable AUV will be deployed into a field development where the seabed infrastructure is relatively well understood.
Launch and Recovery
The vehicle is deployed using a deck winch or vessel crane. As the launch and recovery of AUV systems is currently recognized as being one of the major difficulties in operations, the solution to be used is both simple and robust and it taps into the tech- niques developed during many years of ROV operations.
Navigation
Once the vehicle is on the seabed, as part of the launch and recovery method, it will have a position error limited to a few tens of meters. This accuracy is sufficient to seed the initial frame of reference for the vehicle to start navigating by. As it moves off to locate the start point of its first task it uses real time data from the vehicle sensors to identify known features and uses this to refine its position estimate. Although the intelligence in the onboard software to achieve this is very advanced, the process adopt- ed is well understood. We all do this when driving to a new address. Generally we find the district then look for the street and once found look for the house number. This method of navigating is different from the prescriptive script based navigation of sur- vey AUVs, they have no real knowledge of the outside world, except that provided by absolute coordinate sensors, such as GPS or acoustic sensors. The survey AUV must therefore dead reckon using way points achieved by precisely measuring distance, heading and speed and they must fix their navigation using depth sensors and the aforementioned acoustic or GPS updates.
Inspection
As the vehicle navigates closer to the start point of the first task, the position estimate and sensor data interpolation reaches a confidence level that positively identifies the start point of the task. When this occurs the vehicle will navigate relative to the structure using the sensor data as a relative position input to the control system. In the case of a riser inspection for example, the riser will be tracked by the vehicle in three dimensions. For flexible riser inspection this active tracking is very important as any movement of the riser caused by environmental conditions will be taken into account as the vehicle maintains the optimum inspection position. The SpiNav [3] program de-risked this technology using an ROV platform in tank experiments in 2005 and off- shore work in 2006.
As the vehicle moves along the riser image, condition information is gathered and stored digitally onboard the vehicle. This tech- nique of sensor enhanced navigation, positive identification of the task start point and relative sensor based positioning of the vehicle while on-task, provides a very accurate navigation system. A high level of accuracy is achieved using relatively simple sen- sors that do not require the level of complexity and investment seen on the seabed survey AUVs.
Intervention
It is expected that the development path of hover-capable AUVs will follow the same path that the ROV evolution has followed, from observation tasks to simple manipulation then to intervention (look, touch, act). With the vehicle positioned relative to a structure the vehicle based senor package will be used to positively identify the intervention point and initiate the maneuver.
Development of docking techniques is already well advanced. Details of this are covered in the paper entitled "Autonomous
Docking for Intervention-AUVs using Sonar and Video-based Real-Time 3D Pose Estimation" [5]. Tooling required for intervention will have to be tailored to operate from an AUV. At this point in the development tooling has not been looked at in great detail as a solution is considered to be an engineering exercise rather than a technology challenge.
Communications
When the vehicle is subsurface, communication are limited to acoustic or short range electromagnetic modems. The acoustic systems will generally be used for long range communication in support of specific tasks. It might well be the case that some operations require the vehicle to report a finding or change of state. One such task could be the detection of hydrocarbons dur- ing an observation task or the change of state of a valve indicator. For this type of communication the amount of data to be sent has to be minimized to achieve robust communications. An option to install an acoustic array to provide communications and positioning information to the vehicle would be suitable for areas that require more immediate information updates.
To retrieve large volumes of data from a remote sensor in areas where direct communications is not possible requires the vehicle to be close enough to the user's receiver to use high data rate acoustic or electromagnetic modems. This type of mission to pick up data from a sensor or monitor for changes in a seabed asset over a long period of time is ideally suited to the hover- capable AUV.
MTR#3 (18-33).qxd 3/27/2009 2:09 PM Page 31