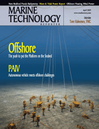
Page 33: of Marine Technology Magazine (April 2005)
Read this page in Pdf, Flash or Html5 edition of April 2005 Marine Technology Magazine
www.seadiscovery.com Marine Technology Reporter 33
WiFi surface system. The final communications system will include: • WiFi Transceiver; for high data rate surface commu- nications over short ranges. Iridium satellite transceiver; for long range (global) communications with a vehicle on the surface. In case that the rendezvous plan is altered this system will act as part of the emergency tracking system. Acoustic modem transceiver; for underwater commu- nications and positioning. On-deck USB 2 cable link.
Emergency Systems
To date the testing of the vehicle has been restricted to test tanks and there has been little need for an emergency recovery system. The next phase of the work takes the vehicle into open water and some or all of the emergency recovery systems listed below will be fitted. Iridium satellite transceiver Drop weight Emergency Xenon strobe light
PAIV Software Architecture
The PAIV control system is built using a modular soft- ware architecture. The modules interact with an Abstract
Layer Interface ensuring ease of use and compatibility when prototyping. The design allows for real modules to be replaced by simulation modules ensuring that de-risk- ing and testing can be done in a controlled manner.
At the core of the PAIV lies the SeeTrack DP Core. This is made up of the Mission Executive, World Model,
AutoPos and Navigation modules. The Navigation mod- ule is responsible for fusing the sensor information and providing a real-time optimal estimate of the position, velocity and orientation vectors. The Autopos module is responsible for guiding the vehicle. It can interpret way- point requests and, by using the output from the
Navigation module as a reference, place demands on the different thrusters to meet those requests. The World
Model keeps a representation of the world. The Mission
Executive module interprets the mission, goals and assigns new waypoints to the AutoPos module.
The PAIV will be used as a de-risking platform for new modules and capabilities, for example 3D tracking of structures and navigating in the mid-water column with- out Doppler lock. These new capabilities can be easily interfaced as new payload modules or be made to replace existing core modules.
De-Risking Program
The program developed by Subsea 7 and SeeByte is a structured three-phase plan to de-risk the technologies required to provide the services necessary to support Life of Field operations. The stages are:- Prototype Vehicle Development: This includes build- ing the vehicle, developing the control software and test- ing to provide a stable vehicle platform capable of operat- ing in test tanks, inshore and offshore locations. De-Risk Applications: This is the development, in- water testing and qualification of the operational systems. Detailed Project Application Qualification: This phase concentrates on tailoring the technology to provide a specific service to a defined field development. This could involve producing a vehicle designed specifically to match the requirements of the particular work area. This development will use all the proven and qualified software models and operational procedures.
In general the de-risking process follows a simple and structured approach. This can best be described by con- sidering the de-risking of the software components, which follows a carefully structured plan consisting of: Simulation: Each module can be simulated to ensure the interfaces are operational. Hardware-in-the-loop: Real modules can be integrat- ed to the simulated modules and tested as part of the sys- tem. Tank Tests: In water tank tests can be carried out for each component in isolation, as part of a more realistic hardware-in-the-loop exercise, and for the whole system.
It is important to ensure that the AUV can react to failures of components in a predictable and safe manner. Inshore Tests: These include in water tests in lakes and harbours. Inshore tests are an economic and safe way to test the whole system. Infield Testing: In the form of a demonstration this test will show the procedures and systems qualified oper- ating in a real work environment.
Current Status
The PAIV has been built in order to test the initial soft- ware modules in a series of experiments carried out in a water tank. The tests also serve to demonstrate the systems capability. As previously described the physical form of
PAIV is relatively unimportant and the status of the soft- ware development is more critical. To date the PAIV vehi- cle software has integrated the 3D sonar tracking payload module and an enhanced mid-water navigation module.
The 3D sonar tracking module can be used to build a 3D picture of the environment by detecting and tracking tar- gets in sonar data. PAIV can then hover and maneuver
MTR#3 (18-33).qxd 3/27/2009 2:23 PM Page 33