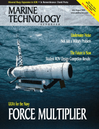
Page 43: of Marine Technology Magazine (July 2005)
Read this page in Pdf, Flash or Html5 edition of July 2005 Marine Technology Magazine
44 MTR July/August 2005
Principal Scientist/Director of Analysis & Applied
Research at BAE Systems and was one of the U.S. repre- sentatives on the working group which reviewed CRR 209. He notes that, CRR 209 was never intended to be used as a yardstick to "minimize potential harm to life in the sea." Before the 1995 report, there were numerous studies discussing and quantifying non-military vessel radiated noise. These studies started in the 1960's and were mostly conducted throughout Europe. While very little research appears to have been published in the
United States during this period, Dr. Holliday notes that significant research was conducted at the University of
Maryland on fish hearing reaction to noise.
Dr. Holliday notes that, "The risks, rationale and costs in the military applications of ship silencing are very dif- ferent than those for the fisheries assessment communi- ties. CRR 209 was a carefully reasoned (and) measured attempt to balance risks and costs (of ship silencing) as specifically driven by the data quality requirements of modern fisheries assessment fleets". However, as of today, the ICES CRR 209 remains to be the only non-military underwater noise limit. No U.S. equivalent standard has been created.
How to Keep the Waters Quiet
Designing a vessel to be quiet underwater (acoustically quiet) is not a simple task. It is also not something you can just add to vessel capability in the middle of con- struction and certainly not something that you can accomplish after a vessel has been completed. Building a vessel that is acoustically quiet requires concerted effort from the owner, operator, naval architect, shipyard and most certainly the marine acoustical engineer.
The phrase, "do not try this unless you are a trained pro- fessional" certainly applies. The reason for such snobbery is that the transmission of shipboard generated noise is pervasive. It can travel down any faulty machinery mount, piping run or faulty structure. Also, the noise control treatments required cannot be retrofitted after the vessel is completed. In some cases, the noise requirements can drive selection of the types of equipment such as pro- pellers, drives, diesel engines and propulsion motors.
Now that the appropriate warnings have been given, keeping the waters quiet involves many noise control ele- ments. Some of these treatments are the same materials used for making vessel compartments quiet and any vessel that meets the CRR 209 underwater noise limit should generally have quiet interior compartments. The only exceptions would be the engine room which will always have high noise levels and any compartment with noisy
HVAC systems.
Controlling underwater noise requires first and fore- most a quiet propeller. There are no noise control treat- ments that can be applied to a noisy propeller, so it must be designed to be quiet. This means minimizing cavita- tion. Briefly, cavitation is the vaporization of water due to a decrease of the local pressure which generates millions of very small vapor bubbles whose collapse generates signifi- cant underwater noise. The cavitation inception speed must be well below the speed at which the vessel is required to be quiet. Bow Thrusters are very noisy under- water and unless someone invents a new bow thruster they must be excluded from operation during quiet oper- ations.
As for the balance of propulsion and auxiliary machin- ery, the next most significant noise producing equipment are the diesel engines. As noted in CRR 209, the best propulsion train configuration for meeting underwater noise is a diesel electric plant. This allows for effective iso- lation of the diesel generators not always possible with direct drive configurations. The use of high-quality DC electric motors will also minimize vibration being induced into the hull. Other equipment which would need to be potentially treated includes large reciprocating machinery (such as refrigeration plants and air compressors), sea con- nected systems (such as sea water cooling systems) large pumps, large HVAC fans and hydraulic power units.
Any reciprocating machine generates high vibration which needs to be isolated from the hull. Generally, diesel engines are mounted on two stages of vibration isolators.
The same may need to be done for other reciprocating equipment. All but the very smallest pumps should be mounted on one stage of vibration isolation. Sea con- nected systems must be analyzed for fluidborne noise transmission. This is when sound from the pumping chamber (such as vane passage) is transmitted to the water via fluid in the piping. Mitigation of such noise can be accomplished with flexible pipe connections which atten- uates both pipe structural and fluidborne energy.
To determine what treatments are and are not needed, a marine acoustical engineer should be performing under- water noise computations. The Navy has developed such methods for submarine design many years ago, but all this technology is obviously classified. There are other meth- ods which are proprietary. Noise Control Engineering (Billerica, Mass.) has used portions of the SNAME
Design Guide for Shipboard Airborne Noise (SNAME
T&R 3-37) created in 1981 and unclassified data to con-
MTR#1 (33-48).qxd 7/19/2005 10:01 AM Page 44