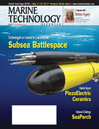
Page 40: of Marine Technology Magazine (May 2011)
Subsea Defense Edition
Read this page in Pdf, Flash or Html5 edition of May 2011 Marine Technology Magazine
40 MTR May 2011 elevator forward drag values were based on standard test data available for NACA airfoils. Forward drag estimates for all components were then combined, and an initial estimate for total vehicle forward drag based on forward speed was produced. These results provided a useful star- ing point, but as the vehicle design was evolved into a functional prototype design, significant shortcomings were identified, particularly the fact that the data available were only for forward drag; little published data were available for cylindrical hulls in very high angles of attack, such as when the vehicle is crabbing sideways or holding station in a current. As a result, it was decided to perform a series of hydrodynamic drag tests with an accurate scale- model of the SQX-500. A 0.88 scale model of the SQX- 500 was constructed and subjected to model testing in the
IOT Clearwater Towing Tank.
The three primary maneuvers of the SQX-500 AUV are forward transit, hovering while holding station, and trans- verse motion or crabbing. In order to provide sufficient hydrodynamic drag data for these maneuvers, three sets of drag tests were performed with the scale model to meas- ure resistance in forward transit, sway and heave. In each set of tests, the angle of attack of the scale model was var- ied in order to obtain data for the vehicle in all orienta- tions relative to the direction of vehicle motion. Angle of attack was controlled using a yaw table mounted to a tow carriage. These tests have resulted in a large number of drag force data sets for all forward and transverse motions at a large number of angles of attack. This data provided input to the design of the propellers and the thruster, and a 6 DOF motion simulator.
After searching for a commercially available propeller, it was decided to perform a custom design using the scale model resistance data as input. Extensive use was made of the IOT cavitation tunnel (interestingly, a device built by the German Navy in the 1930’s for the design of U-Boat propellers and given to Canada as part of reparations after
World War II.) The testing showed that the theoretical performance of a custom propeller design (estimated mathematically) was verified with real-world test data; real-world efficiency was up to 70%, agreeing well with theoretical efficiency. It was demonstrated that the cus- tom design and production of a cast urethane propeller is a viable and cost-effective solution for the design of AUV propulsion systems. An important observation was that high propeller blade rigidity is desirable in this design.
As blade deflection increases while under load, perform- ance decreases as the propeller shape deviates from the design. All remaining aspects of the design and prototype development were performed in the same way – analysis followed by mathematical modeling followed by full or scale model testing using the various state-of-the-art