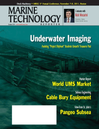
Page 40: of Marine Technology Magazine (October 2011)
Ocean Engineering & Design
Read this page in Pdf, Flash or Html5 edition of October 2011 Marine Technology Magazine
40MTROctober2011 Remember the last time you dug through the toolbox looking for a specific tool? Having the right tool for the job makes all the difference, while using the wrong one can create more work and increase the odds of making mistakes.While the scale of the project may change, the principle still holds true. And this is certainly the case when choos- ing the right subsea technology to bury power cable? using the equipment best suited for the job based on anumber of variables can make all the difference. This paper explores the key criteria to consider when selecting subsea equipment for burying and protecting the power cable that connects the turbines of an offshore wind farm (OWF). OWF technology might be considered relatively new, but undersea cable has been around for quite some time. The first successful trans-Atlantic subsea cable was laid in 1866 and carried telegraph signals. Burying subsea cable and pipe to protect it has become much more common in the last four decades. Many tools have been engineered and used successfully to install and maintain telecommu-nications (telecom), oil and gas (O&G) pipe and power transmission cables. Likewise, many methods and products have been devel- oped for subsea cable protection, tailored for a range of scenarios. These types of protection measures are all gen- erally much more costly than cable burial and are beyond the scope of this paper. Given the enormous distances that protection efforts entail, the most cost-effective approach is likely to use burial equipment, which is detailed in thispaper. The OWF industry is growing rapidly, but is still new compared to telecom and Oil & Gas (O&G). While some subsea installation practices and procedures are transferable to the newer OWF industry, many are not. The inter turbine array cable, or infield cable, requires unique procedures because of the multiple runs of cable within a confined, precisely planned area of the turbine foundation array. General Lay and Burial Methods Here we will outline the pros and cons specific to off- shore wind farms. Please note that different pros and cons can apply for other applications like O&G pipe and tele-com cable. Circumstances can even change significantly between wind farm locations. Since there are many possi- ble vehicles that could theoretically bury inter-array (IA) power cable, it is important to consult with experienced installers and fully examine the positives and negatives of any given system relative to a specific project. Inter-array power cable connects all the turbines to the substation or substations. Once consolidated at the sub- stations, the power travels through ?export? cables as HVAC or HVDC to the shore station. The cable plan will optimize the orientation of the cables from turbine-to- turbine and turbine-to-substation. The two main meth- ods for laying and burying power cable within an OWF array are: Ploughing Simultaneous lay and burial of the cable from point A to point B in one pass. A plough uses a mechanical share tocut a trench that the product cable is depressed into. The seabed falls back on top of the cable to provide instant protection once the plough passes. For long-distance bur- ial, the plough is the most economical method ? when itcan be used.Burial EquipmentHow to choose it for Offshore Wind Inter-Array CableBy Phil Walker and Cliff McDougall, Pharos Offshore Group Ltd.Right:SMD Nereus, Telecom Cable Maintenance Trenching ROV. MTR#8 (34-49):MTR Layouts 10/10/2011 11:33 AM Page 40