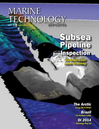
Page 43: of Marine Technology Magazine (April 2014)
Offshore Energy
Read this page in Pdf, Flash or Html5 edition of April 2014 Marine Technology Magazine
Challenges With Existing Technology
Existing subsea metrology techniques have been unable to provide the level of detail afforded by underwater laser scan- ner technology. Video on its own provides an easy to under- stand and interpret qualitative assessment of an asset. From imagery, damage locations can be observed but assumptions about the sizes of features observed are required when mak- ing decisions and this can lead to incorrect assumption result- ing in unnecessary expenses or asset failures. The use of laser scaling techniques can aid in size estimations but true mea- surements are not achieved.
Multibeam sonar is the traditional technique for collecting measurement data over pipelines. This technique is very good at collecting data over long ranges, particularly in high silt conditions where optical technique will fail. However, since sonar is a mechanical wave, as it propagates through the wa- ter, the wave front spreads apart like a ripple on the top of the water and thus the area over which the sonar signal takes its measurement is relatively large. Due to this large acoustic footprint, sonar systems are not able to resolve fi ne features and may incorrectly report there to be returns at the edge of a target where no target exists, resulting in potentially mislead- ing information.
Laser scanning, while not able to penetrate through silt and travel larger distances, is able to resolve very fi ne details and accurately defi ne the edges of structures. The graphic below demonstrates with a simple example the differences in the physics between sonar and laser prorogation.
View animations describing this behavior here: www.2grobotics.com/MTR201405
Laser Scanner Integration and Deployment 2G Robotics underwater laser scanners operate using a trigo- nometric approach. There are two key components, the laser emitter and the receiver. By projecting a 50 degree fan of laser light from the emitter, a stripe of laser light projects on the target surface. The light from the target surface scatters in all directions with a component of this light refl ecting back to the optical sensor (the receiver). The optical sensor measures the angle to the laser light all along the line, based on knowing this angle as well as the relative positioning between the laser emitter and receiver, a profi le of points is calculated. Moving the laser plane, either with an integrated rotary actuator or an external system, a series of adjacent profi les is collected to build a complete 3D point cloud representation of the surface of the object being scanned.
For profi ling pipelines, the laser scanner integrates with ve- hicles in a near equivalent manner as multi beam sonar. When using an external system to move the laser for capturing ad- jacent profi les such as pipeline profi ling, precise positioning is required. To synchronize the laser data with the position information, the data is time tagged and synchronization be- tween the clocks is accomplished with standard PPS (Pulse
Per Second) protocols. Additionally, an accurate understand- ing of the alignment between the positioning system origin and the sensor origin is required, and this is achieved through standard patch tests.
When integrating with an AUV, the laser and the sensor com- ponents can independently be mounted into the vehicle in a confi guration that preserves the hydrodynamics of the AUV.
A calibration process is then performed by the operators to determine the accurate relative positioning. Communication with the 2G Robotics system is accomplished through a bi- nary protocol and code libraries can be provided.
When integrating with an ROV, the laser and sensor hous- ings can remain on the spacer arm and installed directly onto the vehicle with no additional sensor calibration required. It is also possible to mount multiple synchronized systems to an ROV for scanning the sides of pipelines. The systems are controlled through a standard 10/100 Ethernet link to the sur- face and data is published in standard LAS format for use with standard survey packages.
C & C Technologies Results
C & C Technologies is a leader for subsea pipeline inspec- www.seadiscovery.com
Marine Technology Reporter 43
MTR #3 (34-49).indd 43 4/9/2014 11:02:19 AM