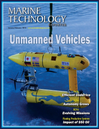
Page 56: of Marine Technology Magazine (January 2015)
Underwater Vehicle Annual: ROV, AUV, and UUVs
Read this page in Pdf, Flash or Html5 edition of January 2015 Marine Technology Magazine
Deck Machinery
Outf tted for Heavy Lif ing
The R/V Sikuliaq, the Alaska Region- al Research Vessel (ARRV) operated by the University of Alaska Fairbanks, boasts the latest in cutting edge electric deck machinery that was engineered and manufactured by Rapp Marine. Rapp
Marine served as the Scienti? c Handling
Systems Integrator on the ARRV proj- ect. In order to effectively operate and conduct surveys in subzero climates,
Rapp Marine designed a ? exible suite of winches and handling equipment that is designed to lower and raise ROV units deep into the frigid, Arctic waters.
Rapp Marine has also recently supplied newly built equipment
Baltic Room Over-the-Side for the R/V Investigator in Australia
Handling Gear
A Load Handling System (LHS) which works together with the CTD and Hydro side of the vessel and is rated to handle Oceanographic Traction Winch winches, which are capable of Electric a maximum working load of 11,100 lbs. One electric oceanographic traction
Active Heave Compensation. The LHS winch system with two storage drums,
System is con? gured to deploy scien- ti? c equipment over-the-side through Hydrographic\CTD AHC Electric model TRW-4000EB, is installed on the
Winches in the Baltic Room vessel. The traction winch system is ca- the Baltic Room door on the starboard
The combined system consists of both pable of handling 0.680-inch diameter
Hydrographic and CTD winches. The ar- electromechanical cable, 0.681-inch rangement will allow both the CTD and ? ber-optic cable and 9/16-inch diameter
Hydro winches to be capable of leading 3 x 19 torque-balanced GEIPS IWRC over the side via the Baltic Room Sys- rope, the storage drums has Lebus tem, or to the aft deck via the ? ag block sleeve installed. The traction winch has to starboard at the aft end of the hangar. a maximum working load of 25,000 lbs.
The primary routing for the CTD will be with minimum retrieval speed of 60 m/ over the Baltic Room hydroboom and min at maximum load.
the primary routing for the Hydro winch shall be to the aft deck through the ? ag PTS Pentagon R Computer System block to starboard on the aft end of the Rapp Marine provided the PTS- hangar. From the ? ag block, the wires Pentagon R computer system for the shall be capable of leading to the stern Oceanographic Traction, Hydrographic,
A-frame or to the hanging block on the and CTD Winch System. The system starboard knuckle-boom crane. monitors and controls the speed, line
The Hydrographic winch has pull of pull, power/amp and wire length as well 11,000 lbs and wire capacity of 33,000 as Active Heave Compensation of all feet of 0.322 EM cable or 26,000 feet of winches. Logging of each sequence ac- 0.375 EM Cable. A bolted Lebus shell cording to user speci? cation is integrat- and Rapp electric level wind system that ed in the system. Each winch has local can automatically adjust to the cable controls on the winch as well as controls diameter without having to change any in the Winch Control Room. mechanical component when the drums Currently, Rapp Marine is supply- are changed out shall be provided for the ing equipment to 8 new research vessel winch projects.
January/February 2015 56 MTR
MTR #1 (50-64).indd 56 MTR #1 (50-64).indd 56 2/4/2015 9:13:59 AM2/4/2015 9:13:59 AM