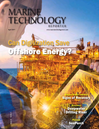
Page 35: of Marine Technology Magazine (April 2017)
Offshore Energy Annual
Read this page in Pdf, Flash or Html5 edition of April 2017 Marine Technology Magazine
Sea transport of drill riser buoyancy modules integrated with inverted helical grooves.
riser coupled with the occurrence of drag is ampli? ed for larg- riser buoyancy modules and therefore VIV suppression comes er structural diameters. These forces induce periodic oscilla- without the undesirable penalty of increased in-line drag. tions or vibrations of the riser, which transmit large amounts Obtainable VIV mitigation properties of the inverted tri-heli- of dynamic strain from the riser system to subsea equipment. cal buoyancy design with the elimination of required auxiliary
With exploration extending into deeper waters and locations equipment simpli? es and increases the running and retrieval with onerous environmental conditions occurring year around, times of the riser compared to traditional suppression technol- the offshore drilling market requires solutions that allow for ogy. Numerous locations across the globe are subject to the large magnitudes of buoyancy uplift without the penalty of sudden onset of onerous weather, requiring drilling vessels to increased drag and VIV forces. be able to respond quickly in order to transit out of forecasted storm paths. If these ? elds are subjected to high current or
Multifunctional Designs VIV inducing metocean conditions, as many of them are, op-
A new multifunctional buoyancy solution has recently been erators may opt out of drilling in these locations at certain developed to integrate drag reduction and VIV mitigation into points of the year or entirely, as retrieval of the riser and vessel
DRBM equipment, reducing the necessity for auxiliary sup- transiting speeds are not adequate with the increases in joint pression equipment and alleviating complicated and time in- handling time associated with auxiliary VIV mitigation equip- tensive riser running and retrieval procedures. ment. With the adaptation of the strake design to an inverted
Inverted helical straking of drilling riser buoyancy modules tri-helical groove, incorporated into the buoyancy itself, sup- allows for in-line drag reduction and VIV suppression of drill- pression of riser VIV and reduction of riser drag is obtainable ing riser systems through the use of a tri-helical groove design without an increase in riser retrieval time, offering a solution molded into the outer pro? le of the buoyancy modules. The for well sites with volatile environmental conditions.
origins of the design stem from external helical strake designs, which have been used in the offshore industry since the late Analytical Modeling 1970s to suppress VIV of slender structures. However, the in- Extensive engineering design work has been performed on verted strake design, unlike its externally protruding predeces- the inverted helical groove geometry through numerical mod- sor, does not increase the overall hydrodynamic diameter of drill elling in computational ? uid dynamics (CFD) software pack- www.marinetechnologynews.com
Marine Technology Reporter 35
MTR #3 (34-48).indd 35 MTR #3 (34-48).indd 35 3/30/2017 11:36:58 AM3/30/2017 11:36:58 AM