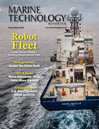
Page 36: of Marine Technology Magazine (January 2021)
Underwater Vehicle Annual
Read this page in Pdf, Flash or Html5 edition of January 2021 Marine Technology Magazine
feet below the hull “on a big metal structure that looks like a prove documents on a shared web based platform.” hammer head shark. It allows the bubbles to stay up next to the “We made the mistake in the past by having different ven- hull while the transducers are below them.” dors supply equipment,” said Mauricio. “The integration is al-
While the gondola was a boon for the science, it was one of the ways dif? cult, and on a retro? t like this, it’s one of the biggest major design and construction challenges in the project. “Build- deals. It’s inevitable that if you have multiple vendors with ing that and then recon? guring all the cable runs and moving multiple equipment there is always a problem, but it’s always the sonars down onto that thing was a big deal,” said Appelgate. ‘his problem, not mine.’” “You know, the ship is the science,” said Appelgate. “I cut To that end, according to Mauricio, minimizing the number my teeth on making and operating sonars that were towed be- of vendors and use COTS equipment was critical, as when the hind a ship. As we got better with sonars and motion sensors, ship was built it included a broad diversity of equipment and those evolved into multi beams. Then we put them onto the manufacturers, which ultimately made the ship more dif? cult ship. Now, all of a sudden, the ship is your sensor. I think it’s (and costly) to service. a valuable exercise to look at a ship holistically in that there’s “Our goal here was to simplify everything in common off- an instrument on the ship, let’s say a multibeam, that’s only the-shelf equipment,” and it was able to use experience build- as good as everything that it’s attached to. Just like vibration, ing the RV Sally Ride ? ve years ago to help in the process. “A if you’re transmitting a bunch of mechanical sound into your lot of our choices were driven by that familiarity with vendors, sonars, you’re going to get junk. The ship is the instrument.” our crew’s familiarity with equipment,” said Mauricio. “We felt that if the crew is more interchangeable and you’re
Cleaner Power familiar with equipment, we can keep our boats in better con-
The original ship contract value was for $35 million to take dition.” care of speci? c ship systems – propulsion, controls, HVAC, A point of focus too, for all machinery was to mitigate noise piping, ballast water management – and steelwork to extend and vibration. “We have learned a lot about power manage- the life of the ship another 15 years or more, said Appelgate. ment and ef? ciency,” said Mauricio. “We incorporated all of
But “we knew that other issues on the ship needed to be ad- that when we did the designs for the new propulsion systems. dressed, or the primary users of the vessel just wouldn’t be (Critical was keeping the vessel quiet as) Bruce’s sonars, their satis? ed.” That’s where the upgrades to science systems came data, relies on the vessel being extremely quiet as far as noise in, adding another $25 million to the project. transmitted through the hulls.” “The repower itself was intense,” said Mauricio. “We gutted To that end much time and effort was expended in the en- the entire engine room and we pulled about six miles of cable, gineering phase to evaluate noise sources and devise means and we replaced about six miles of cable. There was not a to mitigate. “Nothing makes direct contact with the hull; to square foot of that ship that wasn’t disturbed.” make it acoustically quiet, so we don’t interfere with the data “We ended up going with Caterpillars for our main engines, sonars,” said Mauricio. two 3516’s and two C32’s, running them at 1800 rpm,” said In addition, Vigor partnered with Bruce S. Rosenblatt &
Mauricio. “We put 2100 KW generators on the 3516’s and Associates (BSR) to provide detailed engineering support 940 KW generators on the C32’s.” He said while the addition of structural, mechanical and electrical systems. BSR used of the scienti? c gondola increased fuel consumption by about 3D modeling to develop detailed production level drawings 4%, the ef? ciency of the new machinery made it break even. suitable for material procurement and shop prefabrication. “The biggest challenge with this project is the integration The 3D modeling process also helped identify design issues of all new and existing systems,” said Benton Strong, Vigor. such as equipment and piping system clashes early in the “Nearly every major system was either replaced entirely or design phase. upgraded signi? cantly, merging elements of new construction
Autonomy versus Crewed Ships and ship repair into one cohesive project.”
To streamline the ? ow of information among multiple par- While there is a decided move towards increased use of au- ties, Vigor commissioned a custom document control system tonomous systems in the ocean study space, Appelgate con- that allowed key partners to upload, review, comment and ap- tends that there are still many jobs – particularly those that 36 January/February 2021
MTR #1 (34-49).indd 36 1/25/2021 12:25:50 PM