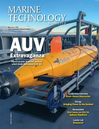
Page 25: of Marine Technology Magazine (May 2022)
Read this page in Pdf, Flash or Html5 edition of May 2022 Marine Technology Magazine
Photo Steffen Pausch, Nautilus Marine Service
Precision glass spheres by Nautilus Marine Service.
Figure 7 lizes their glass. Glass provides great compressive strength, is are buoyant, the epoxy is not. A 1mm sphere in a 1mm cube easily formed of readily available materials, can be drilled and takes up 0.52mm3 volume. The remaining 0.48mm3 interstitial even polished to be a camera housing. Bonding to glass with ad- space is ? lled with epoxy. It has a speci? c gravity of 1.1. Filled hesives is easily done. Equipment mounts can be internal or ex- with 30% microspheres, a syntactic block has a speci? c gravity ternal, providing some design choices. Work is still being done of 0.85.
on creating a metal ? ange to protect the ? nely polished glass Macroballoons can be used to cut the weight, ? lling the inter- sealing surfaces and provide an o-ring seal. Random surface stitial areas with smaller and smaller microspheres, but at the spalling may be due to residual stresses of the casting and form- cost of reduced depth rating.
ing operation. Rubber bumpers over the polished glass edge is Syntactic foams can cause excessive wear of machining bits crutial when the sphere is open to prevent inadvertent damage due to the glass microsphere ? llers. Dust control is important. from impact to the glass. Mixing too large a mass of syntactic is challenging as the resin is exothermic, and can get hot enough to crack the block.
Syntactic Foam: Engineered Syntactic Systems (Attleboro, Like thick cake batter, free pouring the thick resin can pull
MA) [www. esyntactic.com/], Trelleborg/Ecco? oat (Boston, in inclusions of air, which can be a problem at depth. Vacuum
MA), DeepWater Buoyancy, (Biddeford, ME) [deepwater- degassing is one technique used to control this.
buoyancy.com], SynFoam (Livingston, NJ). To maximize microspheres in a structure, some companies
Syntactic foam embeds hollow glass microspheres in a rigid cast the parts, allowed the microspheres to ? oat to the top, let it epoxy matrix. This allows machining to a particular shape. The cure, then ? ip the part over and machine off the resin rich layer.
microspheres have diameters ranging from 10 to 300 microm- The resin is hygroscopic, and will absorbed moisture over time. eters, providing the compressive strength. While the spheres That won’t affect the buoyancy of the microspheres. Painting or
EMPOWERING www.marinetechnologynews.com 25
MTR #4 (18-33).indd 25 4/25/2022 10:18:05 AM