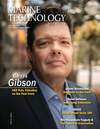
Page 16: of Marine Technology Magazine (July 2023)
Read this page in Pdf, Flash or Html5 edition of July 2023 Marine Technology Magazine
LANDER LAB #8 TITANIUM AND OCEAN LANDERS als, occasionally designers are faced with that challenge. It gall, and a higher melting temperature coupled with a sensitiv- is important to recall that corrosion requires both an electron ity to welding contamination. Welding requires shielding from path and an ion path. Seawater is assigned the role of ion path. air using Argon or Helium gas shielding techniques to avoid
Isolating dissimilar materials with a non-conductive material brittle welds. Galling can make tapping dif? cult.
breaks the electrical path, and thereby the galvanic cell. I have used ? anged Delrin washers to isolate titanium fasteners from
ANODIZING TITANIUM an aluminum frame.
Titanium can be anodized. One patented process is called
The frame has survived multiple year-long deployments “Tiodize”. The surface growth is ranges from 20-200nm, little without harm. I tried a similar approach with connectors of enough that no machining tolerance is required. Titanium an- one material into a housing of another material using Delrin odize is suggested for threads that would otherwise gall. The or Peek insulators (Figure 3).
use of zinc oxide lubricant is still recommended. While the
Tests in early 1965 of Titanium 721 at the Naval Applied anodize oxide is transparent, the parts can appear to have vivid
Science Laboratory showed signs of stress corrosion cracking. rainbow-like colors due to interference coloring.
Ti-6AL-4V ELI grade (Extra Low Interstitials) was developed to have more resistance to this failure mode.
BONDING
To manage costs, lander frames can be made from FRP
Titanium’s dense oxide layer creates a low surface energy structural elements, with side panels from HDPE, reducing substrate that is dif? cult to bond to. The oxide layer can be cost and weight. Lifting bales are preferentially made of ara- abrasively blasted then primed within 2-3 minutes to create a mid ? bers such as Kevlar, as they are lighter, stronger and can satisfactory bonding surface.
tolerate ? ex cycles normally experienced on recovery better than materials that are prone to work hardening.
CASTING AND 3D PRINTING
Casting of titanium parts is done in an inert atmosphere for
MACHINING AND FABRICATION reasons noted above. Laser sintering of titanium has been
Titanium fabrication requires an appreciation for the unique shown as a practical 3D print process, but also requires an characteristics of the metal including: lower modulus of elas- inert atmosphere. Both have less strength due to porosity and ticity, lower ductility, low thermal conductivity, a tendency to lack of grain structure found in wrought material.
ACKNOWLEDGEMENTS
The author gratefully acknowledges the contributions of Michael May, Decisive Testing; Mike Gomper (Clint Precision Manufactur- ing); Reed Jackson (RJ Machine); Rob Klidy, Manager, Scripps Institution of Oceanography/UCSD Machine Shop, Stephen Dexter “Handbook of Oceanographic Engineering Materials”; R. Frank Busby “Manned Submersibles”.
Photo by Kevin Hardy, Global Ocean Design
Figure 3
A brass MCBH bulkhead connector is isolated from an aluminum housing using a two-part Delrin insulator.
The adapter assembly is (left-to-right) Delrin internal/external threaded insulator, Delrin adapter plate, and brass adapter plate. The combination has been tested to 10,000psi. 16 July/August 2023
MTR #5 (1-17).indd 16 7/20/2023 9:07:09 AM