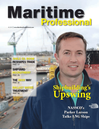
Page 56: of Maritime Logistics Professional Magazine (Q4 2013)
Shipbuilding, Repair
Read this page in Pdf, Flash or Html5 edition of Q4 2013 Maritime Logistics Professional Magazine
disinfection processes can be further classiÞ ed into physical or chemical treatment processes. The latter may involve residual control to meet discharge limits for active chemical substances or physical enhancement technologies to improve treatment performance.As shown in Figure 2, the global market for BWT systems is dominated by two treatment technologies -- UV and elec- trochlorination. These are manufactured by 26 equipment suppliers and compose 85% of the approximately 1,500 IMO type-approved BWT systems installed to date. The basic pro- cess trains are generally described above. UV Disinfection: This is a two-stage treatment process with a pressure-rated Þ lter unit (typically with micron-rated disks or membrane elements) to remove sediment and larger organisms, followed by a UV disinfection unit to inactivate smaller plankton, bacteria and viruses. No chemicals are re-quired to operate the system. During ballasting, water is typi- cally processed through both the Þ lter and UV stages as water is pumped into the ballast tanks. Solids captured by the Þ lters are discharged at the ballasting location. During de-ballasting, the Þ lter is typically bypassed and water is treated by the UV unit only before discharging overboard. Electrochlorination: This is a two-stage treatment process with a micron-rated pressure Þ lter or strainer followed by an electrochlorination unit. The latter is essentially an on-demand chemical system, which uses electrolytic cells to generate a sodium hypochlorite (bleach) solution from seawater and elec- tricity. Some treatment systems pump the entire ballast water ß ow through the electrolytic cells, whereas others use a small slipstream to generate a concentrated hypochlorite solution, which is then recombined with the main ß ow. During ballast- ing, water is processed through both the Þ lter and electrochlo- rination unit as water is pumped into the ballast tanks. A chlo- rine residual (or residual oxidant) is maintained in the tanks for a minimum contact time (typically a few days) to improve dis- infection and eliminate regrowth of organisms during transit. BALLAST WATER TREATMENT Shipboard installation of electrochlorination system for generating sodium hypo-chlorite. (Image courtesy of Severn-Trent deNora) 56 | Maritime Professional | 4Q 2013MP #4 50-63.indd 56MP #4 50-63.indd 5612/11/2013 2:14:39 PM12/11/2013 2:14:39 PM