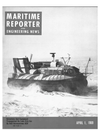
Page 10: of Maritime Reporter Magazine (April 1969)
Read this page in Pdf, Flash or Html5 edition of April 1969 Maritime Reporter Magazine
A Combination Of Skills Produces Scarabeo Completed late in 1968, the semi-submersible drilling unit Scarabeo II is currently at work in the middle of the Adriatic Sea, almost exactly half way between Italy and Yugoslavia. As the newest semi-submersible unit to be placed in service, it represents the latest technical advance in this relatively new and demanding field, drilling for oil and gas in waters far from shore. The Scarabeo II is a unique com-bination of American technology and Italian shipbuilding craftsmanship, and is owned by SNAM-Progetti S.P.A. of Milan, Italy. The design is by the firm of Friede & Goldman, Inc., naval architects and marine en-gineers, of New Orleans, La. The unit was built by the San Marco Yard of the Cantieri Riuniti del Adriatico of Trieste. The Scarabeo II may be considered a second generation development of a type of drilling unit conceived by Friede & Goldman, Inc., and first utilized in the design of the Sedco 135 class. While differing in dimensions and in many details from the earlier units, the Scarabeo II employs the three caisson principle. The unique appearance of this type of semi-submersible drilling rig stems from the basic requirement of provid-ing a low-motion platform for drill-ing purposes. The three vertical cais-sons offer a very small waterplane area to the buoyant effect of passing waves, thus minimizing heave, roll and pitch. Stability against capsizing is accomplished by having the three caissons centered at relatively large distances. The Scarabeo II has an overall length of 352 feet, a maximum breadth of 306 feet, and each of the three caissons is 36 feet in diameter. Each caisson rests on a stream-lined footing having dimensions of 120 feet long, 60 feet wide and 25 feet deep. The elevated main deck is 176 feet above the bottom of the unit, and provides a vast triangular area for machinery, storage space, and accom-modations of personnel. When under tow, the vessel has a draft in the range of 20 to 24 feet, and while drill-ing, the draft is increased by ballast-ing to the 70 foot range. The vessel can drill while resting on the ocean floor in water depths to 120 feet. In deeper water, the vessel drills while afloat. The unit has been constructed to meet the requirements of both the American Bureau of Shipping, and the Registro Italiano. Of all-welded steel construction, a considerable por-tion of the structure is made of high-tensile material manufactured in Italy. The constructioin of units of this type has taken place in many countries of the world, and each shipyard has usually differed in erection technique. The San Marco Shipyard elected a similar approach to that used in Ja-pan. Pile supports were driven in the harbor bottom, the three footings were separately launched, and were placed upon these pile supports. The caissons and the connecting bracing were installed by floating cranes and the elevated deck erected upon these supports. Only when fully completed, was the drilling unit lifted off these supports by the simple expedient of pumping out ballast water. The drilling machinery is typical of the giant equipment utilized offshore. The drawworks is an Ideco Model 2500 manufactured under license in Italy by Nuova Pignone, driven by Siemens electric motors. The two main mud pumps are 1,600-hp Na-tional Supply manufactured units and a third smaller pump is from Ideco-Pignone. The electric driven rotary table is an Ideco HS-275. The drilling mast has been supplied by Lee C. Moore Corporation. The underwater blowout preventer stack is by Ca-meron Iron Works. Rucker constant-tension units are fitted for both the riser system and the guide lines. Bulk mud and cement are stored in pres-sure tanks manufactured by Halli-burton. Three cargo-handling cranes are installed, all supplied by Clyde Iron Works. One of these is a 70-ton stiff-leg derrick and the other two are 40-ton revolving cranes. One of the most important systems aboard a semi-submersible drilling vessel is the mooring system. This unit is equipped with nine giant moor-ing winches, each powered by a 75-hp electric motor. Each winch has 3,000 feet of wire rope, inches in di-ameter connected to 30,000-pound anchors. This system will permit working in water depths up to 600 feet deep. Perhaps the most unique machinery onboard the Scarabeo II is the diesel -electric powerplant, incorporating for the first time on an offshore drilling vessel the principle of generating alternating current power with static conversion to d-c power where motor speed control is essential. The electri-cal generators, controls, switch gear and converters, have all been supplied by the German firm of Seimens A. G. The diesel-electric sets supply alter-nating current to a common bus, and in turn this bus can be tapped for any number of power using devices. Where d-c motors are used, namely, for the mud pumps, drawworks and the rotary table, the a-c current passes through a thyristor which converts the alternating current into direct cur-rent. The highly successful direct-current system used for drilling rigs up to now requires each d-c motor to be connected directly to an individual d-c generator in order to obtain speed control. This necessitates running many diesel engines even when the total amount of power used is a frac-tion of that operating on the line. ()n the Scarabeo II only sufficient gener-ators need be operating to satisfy the total load. This should result in a re-duction in wear on the diesel engines and in the total fuel consumption. Five diesel-electric units were in-stalled, each consisting of a 1,200-hp Fiat, Type A 238ESS, diesel driving a Seimens generator. The accommodations are of a very high standard. Accommodations are provided for a total of 66 persons? two private cabins, 18 two-man cabins, and 7 four-person rooms. The interior of the accommodations are of fire-proof construction and furnished with high-quality furniture. Air condition-ing is provided during warm weather, and heating for winter conditions. The galley is fully equipped with elec-tric ovens, ranges, refrigerators, dish-washers, etc.. all of Italian manufac-ture. Two large dining rooms and a separate large recreation room have been installed. While at this time the Scarabeo II has only been working for several months, reports indicate excellent performance in all respects. The ves-sel has already experienced an un-usually severe winter storm, during which motions were surprisingly small. The electrical system has been particularly satisfactory, and promises to become a major contender for fu-ture drill-rig applications. Engine room, showing five Fiat diesels and Siemens generators. Pump room with mixing pump and mud pumps behind it. 12 Maritime Reporter/Engineering News