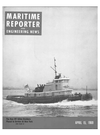
Page 46: of Maritime Reporter Magazine (April 15, 1969)
Read this page in Pdf, Flash or Html5 edition of April 15, 1969 Maritime Reporter Magazine
Priam-Class Cargoliners (Continued from page 46) holds along the length of the ship. This took into account the size and shape of hold and type of cargo gear, the aim being to load or dis-charge each hold in the same period of time. The concept has been ex-pressed by others, but it is not easy to achieve a perfect balance in a ship where the overall shape changes as rapidly along the length as it does in a fast cargo liner. Table 1?Principal Characteristics Length bet. perps. 521 ft. 0 in. Breadth mid. 77 ft. 6 in. Depth to upper deck 44 ft. 0 in. Summer load draft 30 ft. 0 in. Block coefficient 0.59 Displacement (tons) 20,400 Deadweight (tons) 1 1,140 Service speed (knots) 21 WvT~ 0.92 Shaft horsepower 18,900 Shaft rpm no Cubic capacity (cu. ft.) 737,000 Gross tonnage 12,094 Net tonnage 6,471 Cargo Working Speed in handling and stowing cargo was a prerequisite. In the holds there are therefore as few obstructions as possible. The frames, frame brackets, beam knees and ventilation trunking in the main holds have been buried in the wing tanks. These tanks (wa-ter ballast in Nos. 4 and 5 holds and fuel oil in No. 3) also have the effect of squaring-off the curvature of the ship sides. Admittedly, there is a loss of cubic space in doing this but the overall advantages justify it. Additionally, these wing tanks provide a facility for rapidly correcting heel while the liquid cargo tanks are pumped, or when the deck cranes are moved to one side. They also provide a means of alleviating the stresses in the hogging conditions. The cargo hatches were made as long as possible. Hatch width was a compromise between the 'open' ship on the one hand and the need for sufficient 'shelf space' in the 'tween decks on the other hand, be-cause of the number of ports of call. All hatches are fully power-operat-ed. In addition, the sections of each 'tween deck hatch can be subdivid-ed in several ways to give greater choice in the way the holds can be served, i.e., the ends of the hatch can be left in place and the center opened or vice versa. There are cofferdams around all the deep tanks. This undoubtedly casts away cargo cubic capacity but was considered to be worthwhile in reducing the cleaning costs which are an unavoidable part of deep-tank operation, as well as giv-ing better separation between li-quid cargoes. All the associated services such as bilge and ballast lines and sound and air pipes can also be led within the cofferdams which again makes for easier clean-ing and maintenance. In ships with flush 'tween decks, the support or 'tomming' of part cargoes in the wings can be a prob-lem as there is nothing at the deck to get a grip on. At the same time, there is the continual quest for quick stowing which means that less effort is called for in chocking-off the cargo. 'Priams' therefore have a series of vertical tomming stanchions, hinged at the top and for easy removal, slotting into a low shoe on deck, and made of alu-minum for easy portability. Fore and aft timbers can be laid between these as necessary. Cargo Gear The traditional derrick and winch system has been partly superseded. Each main hatch is served by a 5-ton crane at one end and some kind of derrick system at the other end. The cranes can traverse across the ship as required. As a 20 foot outreach beyond the ship side was required, this arrangement was considered preferable to hav-ing a fixed crane on the center line with a 59 foot outreach. All der-ricks have powered topping and those on the bridge front have powered slewing as well. With the cranes and the Stulcken 60-ton derrick, the A.E.G. or Hallen der-rick system at the bridge front and the remaining derricks convention-al in type, there are four different types of cargo gear on each ship. These undoubtedly involve a high-er first cost and also greater main-tenance but are more efficient in handling cargo. The exact benefit of installing and maintaining more expensive cargo handling gear and hatches is difficult to cost. Some indication of their value is gained from con-sidering the reduced time taken to prepare the ship for the stevedores each day. A ship with conventional hatches and cargo gear might in-volve a gang of 18/20 men in one hour of unproductive work in un-covering hatches and getting cargo gear into action. On the 'Priams' the corresponding unproductive time is about 10 minutes. Generally, the faster turn-around in port of these ships coupled with the higher sea speed has meant that even though the voyage is now around the Cape instead of by the Suez route, the intended monthly schedule is being main-tained. The 'Priams' are spending an average of 193 days at sea per year, as compared with 201 days for the Glenlyon Class. However, all the ships are now sailing around the Cape and so tend, with the larger sea mileage, to have higher time at sea. Main Structure The rather unusual distribution along the ship's length of the main cargo compartments involved a close examination of the longitudi-nal strength. The structure on the 'Priam' class is a combination of transverse and longitudinal framing and is shown in Figure 2. Figure 3?Comparison of building times between U.K. and Japanese shipyards. Heating Coils In this class of ship the deep tankage capable of taking heated oils represents a very sizeable pro-portion of the cargo space. Every effort was therefore made to reduce the capital cost, maintenance cost and operational costs of the cargo heating system. The heating in all tanks is by steam coils but three different types of coils were used. For the small 50-ton tanks in No. 1 and 7 hold, the heating coils are in the form of hollow D sections and are permanently welded to the outside of the tank, i.e., in the cof-ferdams. At first it was proposed that all deep tank heating coils should be permanently welded to the outside of the tanks, but difficulties regard-ing the required heating surface areas, and overheating in the coffer-dams made this undesirable for all spaces. The next step was to weld the permanent coils inside the other tanks but the use of fork lift trucks in No. 1 and 2 holds meant that the internally welded type of coil was only fitted in the No. 6 tanks. In the No. 1 aft and No. 2 deep tanks, the heating coils are of the normal circular piping within the hold but are constructed in grid sections and are capable of being hinged against the tank sides or, alternatively, of being lifted out altogether when the tank is used for general cargo or unheated oils. Construction Methods It is generally recognized that Japanese shipyards have introduced new techniques into the manage-ment and production aspects of building and the authors were fa-vored with an early insight into these during the building of the two Japanese-built 'Priams.' Fig-ure 3 shows the comparison of the building times required by each of the three shipbuilders. The build-ing period is shown divided into the time elapsed between placing the order and laying the keel; be-tween keel laying and launch, and for the outfitting period. As far as the owners are con-cerned, the effects of the Japanese performance are: 1. All major plans must be ap-proved, the major decisions must be taken, and subcontractors agreed during the pre-planning period, o*o 0-70 oeo 090 v//l" Figure 4?Ballast trial results for six ships. Both the Japanese and the Brit-ish shipyards built the ships in about 300 sections, the heaviest of which was 75 tons, the rest being nearer 30 tons. For the typical large tanker, the Japanese would certainly adopt heavier units, or blocks as they call them, but for this type of fine-lined cargo liner with almost double-skinned hull construction they were obliged to resort to smaller units. Trial Results Speed trials in ballast condition were conducted for six of the ships ; bad weather ruled these out on the remaining two. The power?speed and rpm?speed curves for these ballast trials are shown in Figure 4. 12.000 10.000 B.OOO 6.000 4.000 with little time to alter opinions subsequently. 2. There is a shorter but much more concentrated load on the owner's superintendents supervis-ing the steel construction, and a heavier load on the owner's plan approval staff at an earlier stage in the building period. 16.000 IOO -I RPM I BO-20.000 BMP. isooo 48 Maritime Reporter/Engineering News