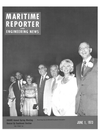
Page 21: of Maritime Reporter Magazine (June 1973)
Read this page in Pdf, Flash or Html5 edition of June 1973 Maritime Reporter Magazine
LASH And Sea Barge
Contract Awarded
Conditionally By Navy
A contract to build and charter to the Navy two new-type supply ships —a lighter aboard ship (LASH), and a sea barge—has been won conditionally by Marine
Chartering Corp., a subsidiary of
Marine Transport Lines.
The Navy's Military Sealift Com- mand (MSC) will operate the ves- sels once they are delivered.
Marine Chartering must obtain offers to build the two vessels from shipyards, arrange the financing details, and present the total plan to the Navy in about five months for final acceptance.
Jerome Shelby of Marine Trans- port, in confirming reports of the award, said the vessels will be own- ed by a trust made up of Citicorps
Leasing Corp. and First Chicago
Leasing Corp. Construction financ- ing will be handled by First Na- tional Bank of Chicago, and the sale of bonds for the long-term fi- nancing would be directed by Salo- mon Brothers.
Use of the vessels was part of the Navy-MSC effort to upgrade its lift capacity. Utilizing the char- tering of privately built and owned vessels saves heavy outlays for con- struction by the Navy.
Mr. Shelby said he expected of- fers to build from Avondale and
General Dynamics, which have built LASH and sea barges, respec- tively, and perhaps also from Todd and Sun Shipbuilding.
The LASH vessel sought was specified originally to be of 36,000 displacement tons, with capacity for 85 barges. The sea barge was supposed to be of 27,050 tons with capacity for 38 barges of 40,000 bale-cubic-foot capacity each. Ac- commodations for 250 troops each was to be included, plus facilities for containers and heavy lift heli- copters. Each was to have a speed of 21-22 knots.
The Navy has acquired the use of a number of tankers via this build-charter plan.
Pacific NW Section
Hears Paper On Jetties
Pictured at the meeting held at the Jant- zen Beach Thunderbird in Portland are
Howard Hinsdale (left), of the Umpqua
River Navigation Co., guest speaker, and
H.P. Sturdivant of Zidell Explorations, Inc. of Portland, Ore., host of the SNAME meeting.
Today's jetties are no longer con- structed by big trucks dumping loads of big rocks into the sea, the
Pacific Northwest Section of the
Society of Naval Architects and
Marine Engineers were told at a
Portland, Ore., meeting April 20.
In his paper titled "Rock Island
Offshore," Howard Hinsdale of the
Umpqua River Navigation Com- pany, with many years of jetty ex- perience, described the growth of jetty construction since the first
West Coast jetty was built at the mouth of the Columbia River.
A development of recent years is a method of depositing "armor" stone on the sides of the jetty per- pendicular to the sloping surface.
These rough quarried armor stones are brick-shaped, weigh about 25 tons, and are carefully placed— actually locked in place. This armor stone method has a near-perfect record for standing up against waves and weather.
The "Dolo," 43 tons of concrete shaped like the letter "H" with one leg rotated 90 degrees, has tremen- dous locking potential and has been used in jetty construction as a wave energy dispenser.
It is a natural step from jetties to rock islands—much of the con- struction is 'similar. Mr. Hinsdale sees a need for rock islands upward of 200 feet square built in 100 feet of water for oil drilling, for super- tanker terminals, and for nuclear power plants.
The color movie "Jetties Against the Seas," produced by the Ump- qua River Navigation Company, was shown following Mr. Hins- dale's talk.
On deck: the 4th of 20 mammoth LNG tankers, each slated to have innards of nickel alloys.
Construction of "Hull No. 196," blueprinted at left, is currently in progress at the shipyards of M'oss
Rosenberg Verft a s, Stavanger,
Norway.
When she's completed next year, the giant 555,000-bbI. ship with spherical tanks of 9% nickel steel will be the fourth in a whole new generation of larger-sized
LNG tankers scheduled for service by the mid-70's.
All 20 of the bigger tankers on the drawing boards to date have capacities in the 300,000-bbI. to 750,000-bbl. range.
And all 20 ships, like many of today's smaller LNG tankers, are planned to have cryogenic piping, pumps and cargo tanks of nickel alloys.
Proved in cryogenic service
Why nickel?
Because nickel alloys have proved themselves to have the optimum combination of prop- erties desired for LNG containment: toughness and ductility at cryogenic temperatures; high resistance to corrosive saltwater atmospheres; plus ease of fabri- cation and excellent weldability.
Why spherical design?
Use of the'spherical design for the five tanks of the new Moss
Rosenberg ship permits elimina- tion of the usual secondary barrier (at substantial cost savings). And it helps improve overall reliability of the containment system.
For large spheres, 9°/o nickel
The choice of 9% nickel steel as the particular nickel alloy for the spheres was made for several reasons.
First, of course, the design and large size of the spheres require great strength. 9% nickel steel was developed by International Nickel back in the early 1940's expressly to retain toughness and strength at cryogenic temperatures. (This is also a reason why 9% nickel is far and away the leading material for field-erected LNG storage tanks.)
Another consideration was 9% nickel's relatively low coefficient of thermal expansion.
And finally, the larger the project, the more important on-site weldability becomes. 9% nickel is amenable to both manual and automatic field welding.
Other designs, other nickel alloys
For your own LNG tanker, you can choose 9% nickel—or either of two other nickel alloys that have been used successfully in cryo- genic service: • Type 304L nickel stainless steel. • Invar* 36% nickel-iron alloy.
It depends, really, on the design you prefer for your ship.
For more details on nickel alloys in cryogenic service, write
Dept. 6573, The International
Nickel Company, Inc., One
New York Plaza, New York,
N. Y. 10004. inco
In Canada, The.International Nickel Company of Canada, Limited, P.O. Box 44, Toronto-
Dominion Centre, Toronto 111, Ontario.
In England, International Nickel Limited,
Thames House, Millbank,
London SW1 P4QF, England. *A Registered Trademark of
Societe Creusot-Loire (IMPHY)
June 1, 1973 23