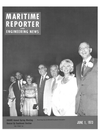
Page 48: of Maritime Reporter Magazine (June 1973)
Read this page in Pdf, Flash or Html5 edition of June 1973 Maritime Reporter Magazine
OCEANIC
ELECTRIC PRODUCTS 0C8MIC \ Bctnc products 50 1921-1971 sfSC "Over A Half Century of
Service in the Marine Industry"
Oceanic products are manufactured to meet the requirements of
U.S.C.G. Electrical Engineering Regulations
NON WATERTIGHT
SWITCHES AND RECEPTACLES
Coll or Write for Complete Catalog
OCEANIC
ELECTRICAL MFG. CO., INC
So/'e Manufacturers of Oceanic Electric Products 157-159 PERRY ST., NEW YORK, N.Y. 10014 • WA 9-3321
SHIP PARTS
MARINE EQUIPMENT
BARGES
SALE OR LEASE
ALMOST ANY SIZE GR TYPE
ALSO BARGE CRANES AVAILABLE
Various Whirley Cranes Available
Washington / Americans
Now Dismantling
Victories - Aircraft Carriers
Destroyers - C-3 Cimavis
Winches plus Booms, Engine Parts
Surplus Ship Parts and Supplies Available
Union Tank Car Plant Five Miles From Water
Builds And Launches A LASH Barge Each Day
SCHNITZER
INDUSTRIES 4012 N.W. FRONT • PORTLAND, OREGON
PHONE: (503) 224-9900
Mailing Address: 1 W.U. Telex: 36-0144 PTL 3300 N.W. Yeon Ave. I Coble Schnitzerbro, Portland
Building and launching 61-foot by 30-foot by 13-foot LASH barges is a project for any shipbuilding company. It is especially so for a manufacturing company whose plant is 'lo- cated five miles from the nearest navigable waterway.
Officials at Union Tank Car Company, sec- ond largest railroad tank car manufacturer in the United States, realized that last year when they offered their advanced plate welding tech- nology in a bid against established marine builders on an order for 440 LASH barges from Central Gulf Lines, New Orleans, La.
Both companies are affiliates of Trans Union
Corporation of Chicago, 111.
Their huge tank car fabrication facility in densely populated East Chicago, Ind., met every requirement except launching space. But they had a solution for that, ready to put into action when they won the contract.
Union Tank Car entered the LASH barge construction business with the $17-million or- der.
The first LASH barges ever built in'the Chi- cago area are now sliding into the U.S. Ship
Canal at East Chicago, Indiana, at the rate of one a day, according to their builder. To date, over 40 barges have been launched, adding to the "made in U.S." status of the nation's mari- time fleet.
R.D. McEvers, president of Union Tank
Car, said the company won the contract in competitive bidding against other barge and shipbuilders because of advanced plate fabri- cation technology gained in building railroad tank cars.
Mr. McEvers said the 440-barge order will be fulfilled by the end of 1974.
Their solution to the "five miles from water" dilemma is to modularize each barge in nine individual sections at the main tank car pro- duction plant in East Chicago, and transport them by truck to a much smaller, specially- built assembly plant on the U.S. Ship Canal that feeds into Lake Michigan.
The assembly plant was built especially for
LASH barge production. Its layout is ultra- simple, as can be seen in the accompanying illustration. The nine modules are assembled into a finished barge as they move via a spe- cial rail-mounted transfer table through six work stations, much as an automobile moves •through a Detroit plant.
Finished barges splash into U.S. Ship Canal to await movement into Illinois waterway on way to New Orleans.
The initial station is the bottom assembly, where five bottom modules are laid side^by- side and welded. The second or "fit-up" stage puts the remaining side and end modules in place and tack welds them.
Welding is completed at the next station, after which the unit transfers to the test and repair slot. After technicians examine the ves- sel to make certain it is completely leak-free, the barge moves to the painting and drying bay.
Finished barges are moved outside, fitted with watertight hatch covers and slid into the
U.S. Ship Canal at East Chicago, Ind., to await their maiden downriver towboat journey. Cur- rent production rate is one barge a day.
The 440 LASH barges to be built by Union
Tank Car will implement Central Gulf Lines' plan to expand LASH shipping and bring ocean transportation into reach of more and more inland shippers, particularly those U.S. companies located in the fertile Midwest wa- terway market. Central Gulf pioneered the
LASH system in 1969 and operates two LASH mother ships 'between the Gulf of Mexico and
Europe, and expects to launch an additional three U.S.-flag ships in late 1974 at a cost of about $84 million. These vessels are under con-' struction at Avondale Shipyards, Inc. in New
Orleans, La. Each vessel carries 89 barges. A total of 200 are needed in the waterway system to serve each mother ship.
The LASH ship and barge concept was de- veloped and designed by Friede & Goldman,
Inc., naval architectural firm of New Orleans.
BARGE
LAUNCHING
HATCH
APPLICATION
BOTTOM
ASSEMBLY
TEST AND
REPAIR
PAINTING
DRYING
WELDING
Modular approach to barge building at this six-station assembly building allows Union Tank Car to launch one barge a day. The partially assembled barges are moved from station to station with the rail-mounted transfer table, shown between painting and hatch application stations at right.
UNLOADING AND
STORAGE AREA 50 Maritime Reporter/Engineering News